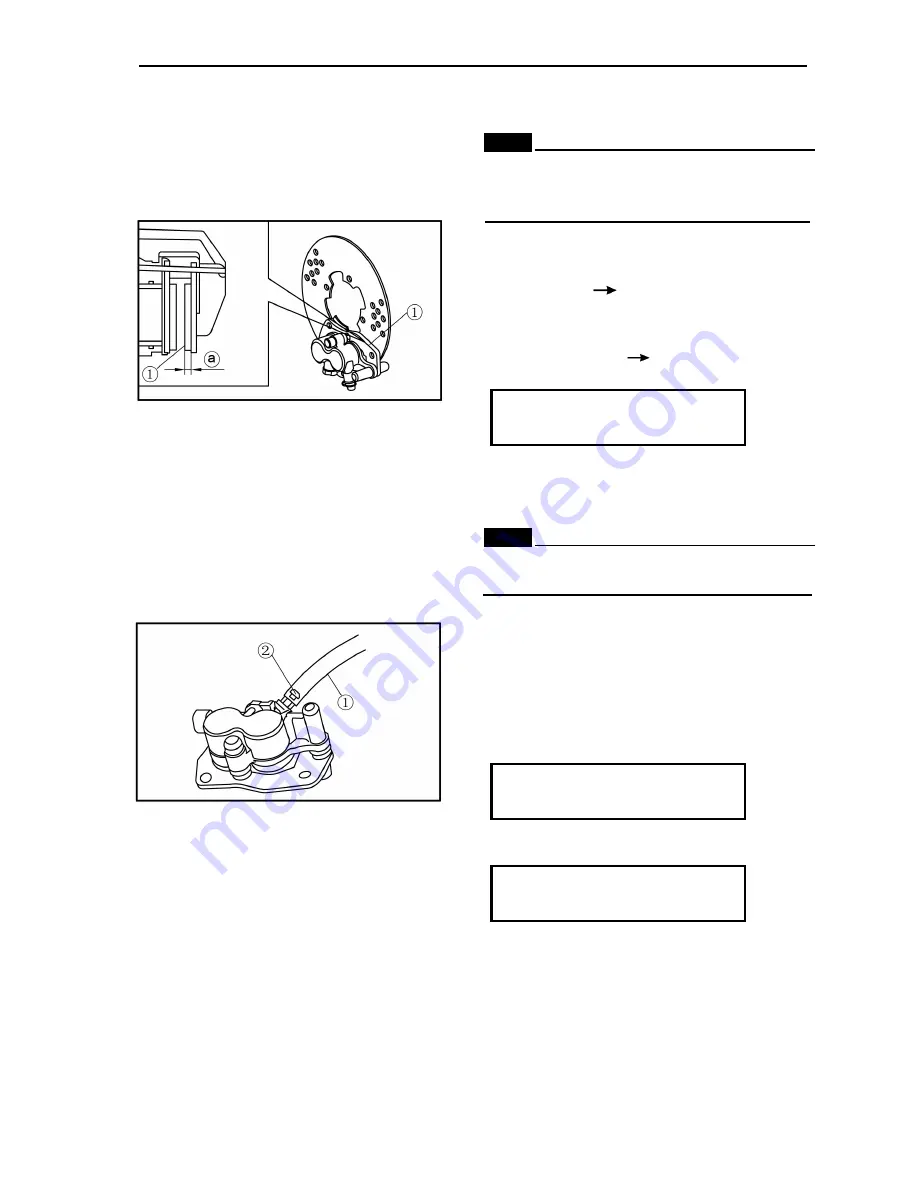
CHASSIS
- 198-
REPLACING THE FRONT BRAKE PADS
NOTE
:
It is not necessary to disassemble the brake
caliper and brake hose to replace the brake
pads.
1.Check:
• brake pad
①
Damage/wear
Replace
2.Measure:
• brake pad thickness
ⓐ
Out of specification
Replace the brake
pads as a set.
Brake pad wear limit
1.5 mm (0.06 in)
3. Install:
• brake pads
• brake pad spring
NOTE
:
Always install new brake pads and brake pad
spring as a set.
a. Connect a suitable hose
①
tightly to the brake
caliper bleed nozzle
②
. Put the other end of this
hose into an open container.
b. Loosen the brake caliper bleed screw and,
using a finger, push the caliper piston into the
brake caliper.
c. Tighten the brake caliper bleed screw.
Brake caliper bleed screw
6 Nm (0.6 m · kg, 4.3 ft · lb
)
d. Install the retaining bolts and brake caliper.
Brake pad holding bolt
18Nm (1.8 m · kg, 13 ft · lb)
Содержание HS800UTV 2014
Страница 91: ...SPECIFICATIONS 79 HYDROGRAPHIC CHART Hydrographic chart Pressure ...
Страница 92: ...SPECIFICATIONS 80 LUBRICATION OIL WAY LUBRICATION OIL WAY Pressure splashing oil ...
Страница 165: ...ENGINE 153 No Part Name Qty Remarks 12 Oil pressure sensor 1 For installation reverse the removal procedure ...
Страница 208: ...CHASSIS 196 No Part Name Qty Remarks 11 Pad spring 2 12 Brake pad holding bolt 4 13 Hexagon flange bolt M10 1 25 22 8 ...
Страница 216: ...CHASSIS 204 No Part Name Qty Remarks 11 Pad spring 2 12 Brake pad holding bolt 4 13 Hexagon flange bolt M10 1 25 22 8 ...
Страница 278: ...CHASSIS 266 No Part Name Qty Remarks 19 Impeller 1 20 Cover water pump 1 21 Clip 1 22 Water pipe 1 ...
Страница 289: ...CHASSIS 277 Fuel tank cap Remove the fuel tank cap by turning it counterclockwise ...
Страница 353: ......
Страница 354: ......
Страница 355: ......
Страница 356: ......
Страница 357: ......
Страница 358: ......
Страница 359: ......
Страница 360: ......
Страница 361: ......