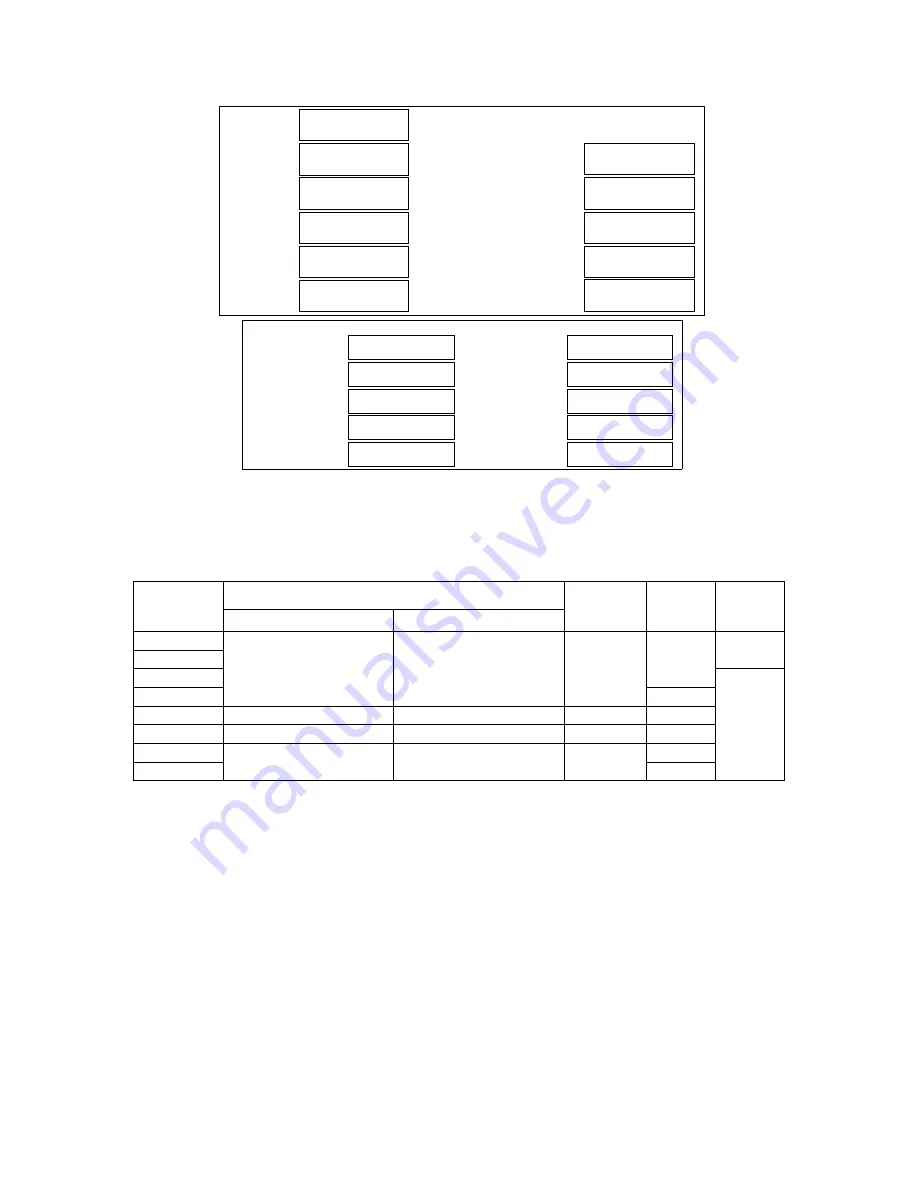
11
Max.Pressure PS
Max Temperatur
Volume V
Min. Temperatur
Volumen
Min. Temp. Tmin.
HYD.Test Pressure Ph
Hydrostaticher Testdruck
Maximaler Druck
Max.Temp.Tmax.
Datum
Design Code
Designcode
Serial No
Seriennummer
Act. Thick Vessel
Manufacture Date
Corrosion All
Korrosionsanteil
Wandstärke/Druckbehälter
Bar
Bar
°C
°C
lt
mm
mm
En 286-1
100
-10
TYP
TYPE
DRUCK
PRESSURE
KAPAZITÄT
CAPACITY
LEISTUNG
NOM.POWER
NENNSTROM
CURRENT
GEWICHT
WEIGHT
SERIENNUMMER
SERIAL NO
HERSTELLUNGSDATUM
MANUF. DATE
VOLTAGE
FREQUENCY
ELEKTRISCHER
SCHALTPLAN
ELEC.DIAG. NO
bar
m /dak
m /min
A
kg.
3
3
~
kW
NENNSPANNUNG
FREQUENZ
V3Ph
Hz
COMPRESSOR
PLATE
OIL TANK
PLATE
3.2 DIMENSIONS
MODEL
W X L X H (mm)
RECEIVER
VOLUME
(l)
WEIGHT
(kg)
NOISE
LEVEL
(dBa)
WITH RECEIVER
WITHOUT RECEIVER
HGS 2
1900 X 642 X 1178
900 X 642 X 830
200
260
68
HGS 3
HGS 4
69
HGS 5
300
HGS 5D
1820 X 550 X 1178
1000 X 550 X 625
200
280
HGS 7
1900 X 645 X 1500
1000 X 645 X 830
500
310
HGS 11
1900 X 650 X 1550
1150 X 650 X 910
500
340
HGS 15
350