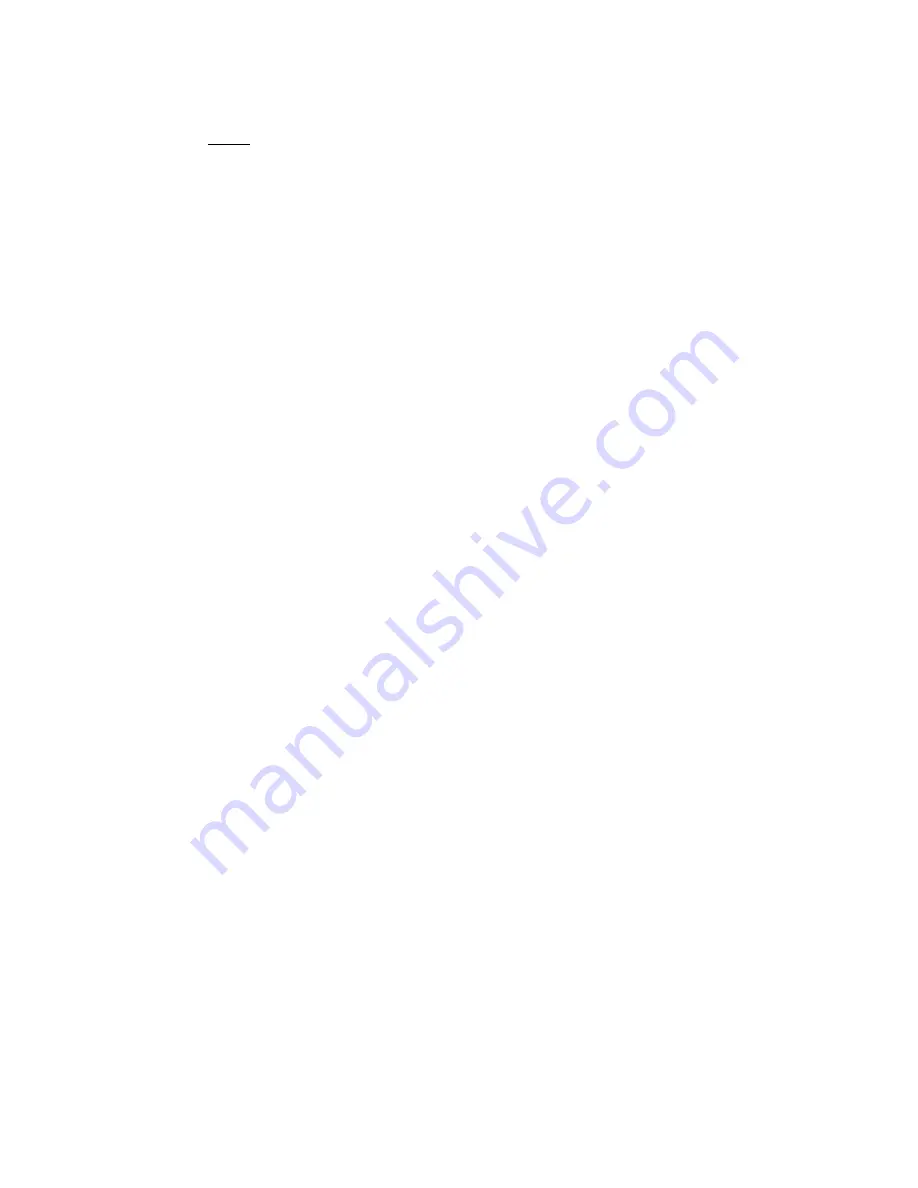
At last the blade holder arms 0116 are tightened to the blade holder 0114 using the corresponding screws and Loctite. Before
tightening the screws 0105b and 0105c pull the arms in the play of their holes towards the main rotor centre and make sure
that they rest properly on the bottom of the blade holder cutout. The threaded link ball 0116a is tightened using Loctite.
Attach the O-rings 0102s with the feathering spindle bushings 0109-2010 to the centre hub. Slightly grease the O-rings. Slide
the feathering spindle 0110 into the centre hub. Make sure that the seesaw 0140a is turned such that the grub screw 0140d
points to the top (do not yet thighten the grub screw!).
Push the preassembled bladholder onto the feathering spindle.
It can occur that the blade holder pre-mounted to the bearings cannot be slid on completely although the bearing can be
moved onto the feathering spindle easily. A shifted spacer washer 0111 that has moved and is not located in the middle
prevents it from being moved further. In this case use a stud and centre the washer such that it is aligned to the other holes of
the ball bearing in the blade holder.
Secure the blade holders using the washers 0117 and the screws 0119 (Attention! The black screw 0119 has a great rigidity
and may only be replaced by an original replacement part. Conventional screws may break. After tightening the screws the
blade holders must have centered automatically and they have the same distance to the centre hub. By tilting the seesaw to
the stop the blade holders strike the plastic bushing, so that the feathering spindle is better centered in the middle. If there is
a remarkable axial play, thin spacer washers can be added between the feathering spindle bushing 0109-2010 and the first
bearing 0113. Always use the same size on both sides (in the bag with the O-rings there are two spacer washers 0.2x 8x 14).
Now tighten the grub screw 0140d well from above through the 5mm hole in the centre hub. Use Loctite and slightly cover the
grub.
Attention!
Avoid adding Loctite to the threaded hole of the seesaw. Otherwise it is pressed by the grub into the passage hole
for the feathering spindle, which then gets stuck. Such a stuck feathering spindle can hardly be removed later without
destroying other parts.
Attention!
Do not yet attach the rotor brake 0103, because the planar supporting area of the main rotor centre hub is needed
as supporting area for a measuring bar to adjust the blades (see Chapter XIV – Adjustments).
After the assembly you will notice that the blade holders can be tilted up and down to a minimum extend around the centre of
rotation of the seesaw within the play of the feathering spindle bushing (The bushings are by two tenth of a mm bigger than
the spindle).
With mounted blades and after some flights you can measure about 3-5mm at the blade tips after all parts are set. The rotor
can be tilted without problems by this amount. This is intended and the reason for this construction.
Therefore no vibration pulses of the rotor are transmitted to the fuselage during hovering. Hereby resonances are avoided
and a smooth hovering during all speeds is assured. During intended cyclic control inputs the feathering spindle tilts against
the relatively hard-damped bushings leading to the desired quick reaction of the helicopter.
For pilots who prefer to fly very hard 3D, most of the time with high head speed above 1700 revs there is a option to get a
stiffer damping by changing the black spindle bushings 0109-2010 against white bushings 0109 which have no play.
Therefore the two inner of the black O-rings 0102s should also be changed against two red O-rings 0102r (please have also
a look at the TDR-manual 2009 for more details). In this case sometimes some fuselage resonances have to be accepted
when hovering between 1400 and 1700 revs.
After a crash do not try to pull the feathering spindle through the seesaw by using the deformed side. Take the undeformed
side.
Check the first visible bearing 0113. The other bearings are usually not affected. Use your finger to turn the inner ring of the
bearing and check if it runs smoothly. You can pull this bearing out without having to remove all the other parts from the blade
holder. Push the old feathering spindle only into this bearing and pull it out of the blade holder (if necessary heat blade
holder) by tilting it sidewisely and luffing it slightly. You can also strike the bearing out from the fork side using a spindle of a
thickness of about 6 mm that is positioned diagonally on the inner ring of the bearing. Do not use excessive forces when
hitting the blade holders on the new feathering spindle, if the bearings jam. It is recommended to clamp the shaft into a
drilling machine and to treat it carefully with a strip of sandpaper.
Attention! Do not use any other feathering spindle for the Rigid 2010 than the original feathering spindle RI-0110 (2010)
delivered by me. This spindle is inductively surface hardened and was spheroidised on both threaded sides to avoid the
danger of hardening cracks in this area with a low diameter. Due to the seesaw bearing the spindle is exposed to higher
forces. These are lower when using a conventional bearing with bending points at a greater distance from each other.
Therefore a normal soft spindle like the one I have used before will be deformed even at low flight loads. However, this
spindle can also be deformed due to certain flight manoeuvres. Avoid extreme pull-out manoeuvres during high air speed,
especially in combination with a low head speed. In this case the centrifugal forces are not yet sufficient to take load from the
feathering spindle and prevent it from bending.
The connecting rods 0121c are mounted according to the drawing. At first turn the 15mm ball links 0121b to the brass
bushing 0121a until they reach the stop. Then turn them, so that they are positioned at an angle of 90° to each other. This
can be facilitated by greasing the threaded rod. In the ideal case the imprint 2,5 is positioned, so that it points to the outside
during the assembly to the threaded link ball of the blade holder arm and the swashplate (lower forces are then necessary to
assemble the link). It will be fine-adjusted later during the adjustment of the blades.
11