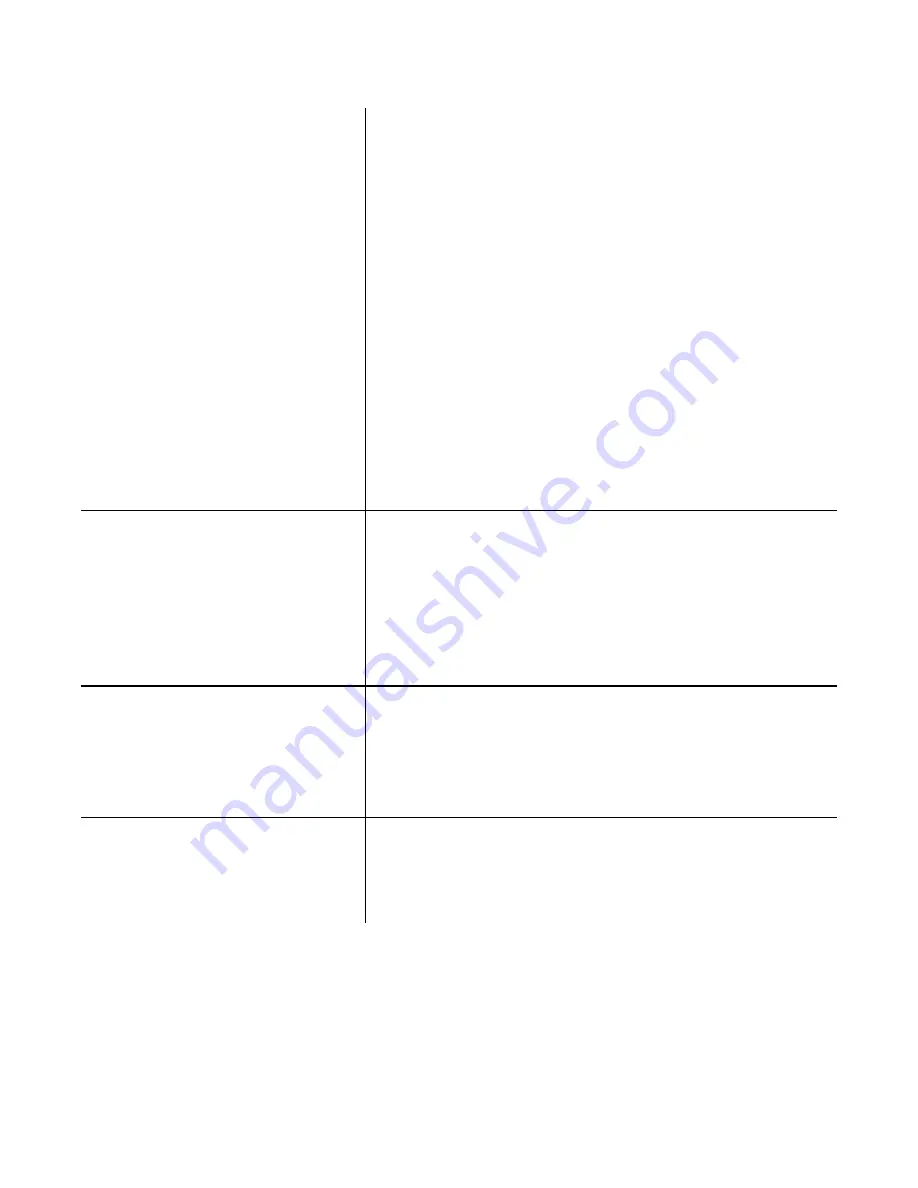
Henny Penny
Model 500/600/561
1-2. PROPER CARE
For your convenience, this manual consists of the following sections:
•
Table of Contents
•
Introduction
•
Installation
•
Operation
•
Troubleshooting
•
Maintenance
•
Wiring Diagrams
•
Illustrated Parts List
•
Distributor List
The conscientious use of the recommended procedures, coupled
with regular maintenance, should minimize the need for repairs to
the equipment. When such repairs are required, they may be
accomplished by following the repair steps contained in this manual.
1-3. ASSISTANCE
Should you require outside assistance, just call your local indepen-
dent distributor. (Refer to distributor list in rear of this manual.)
In addition, feel free to contact our corporate headquarters in
Eaton, Ohio. Dial 1-800-417-8405 toll free, or 937-456-8405.
1-4. MODEL VARIATIONS
This manual covers both gas and electric models, as well as, various
options and major accessories. Where information pertains to only
one model, it is so noted.
1-5. SAFETY
The Henny Penny Pressure Fryer has may safety features
incorporated. However, the only way to ensure a safe operation
is to fully understand the proper installation, operation, and
maintenance procedures, which are contained in this manual.
1-2
1000
Содержание 500
Страница 1: ......
Страница 30: ......
Страница 31: ......
Страница 32: ... ...
Страница 161: ...LINE CORD VALVE GAS W P THERMOSTAT IGNITOR SENSOR TIMER MODEL 600 GAS FRYER 24OV SOHz 1 PHASE SPARK IGNITION 55318 ...
Страница 168: ...SOLENOID HEATING ELEMENTS 27 UTRANSFORMER 12 35 HI LIMIT 23 12 I I 5 I jF11S 1 6 5 HENNY PENNY CORP EATON OHIO 45320 ...
Страница 177: ...MB FOR CTIOM usEco fa RE I I I 18 17 16 1 1 1 i TIMER THERMOSTAT MODEL 561 ELECTRIC FRYER 13 SKW 3PH 480VAC ...
Страница 180: ... F ISI E Ir a I 5 6 7 a 9 9 1 t t Y I r MODEL 561 ELECTRIC FRYER 11 25KW 3PH 208 240VAC 55653 ...
Страница 201: ...el 1 ...
Страница 203: ... f i ...
Страница 204: ... RING Trn ArcLatch KNOB RetainingPin e et Limit StopCollar s ...
Страница 205: ......
Страница 206: ...el 50 ELBOW S S DEADWEIGHT GLASS Pressure Gauge ...
Страница 207: ......
Страница 211: ...ASSEMSL D ON NGNUT TOWARD ...
Страница 213: ...MACHIN OTTOFU NOTE VALVE MUST BE ASSEMBLED ON E WITH ADJUSTING NUT TOWARQS I ...
Страница 217: ......
Страница 219: ......
Страница 221: ...odel ...
Страница 223: ...ire sse as ...
Страница 225: ...Y I561 ...
Страница 227: ...Y sse ...
Страница 229: ...Y els ...
Страница 231: ......
Страница 233: ......
Страница 234: ...CQNTACTORANDF ThreePhase ElectricModel SHROUD Galvanized CONTACTOR SCREW Contactor ...
Страница 235: ......
Страница 237: ...1 ean ...
Страница 239: ...Y l 4ITEMS 3 and 4 FILTE SCREENS FIT INTO FlLTE ...
Страница 241: ......
Страница 243: ...VIEW A ...
Страница 245: ... I I ...
Страница 246: ...DESCRIPTION FilterMotor andPump MOTOR 112Horse 50 60Hz PUMPASSEPVIBLY SCREW PumpCover SCREW PumpShield ...
Страница 247: ......
Страница 249: ...COUNTER TOP SOLENOID VALVE BACK RIGHT t v BJ 7 ...
Страница 251: ......
Страница 255: ...Y ...
Страница 257: ......
Страница 259: ......