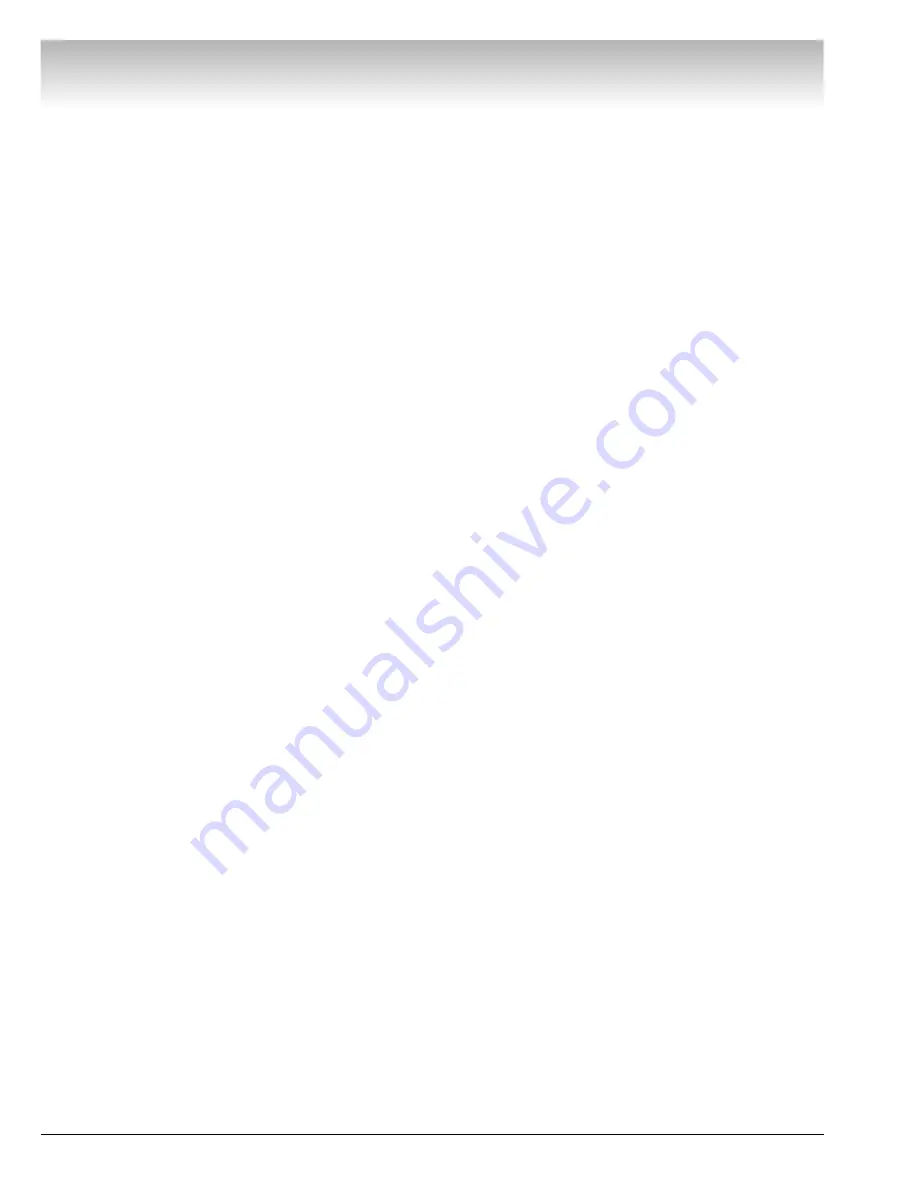
6 • Service Manual — COATS Models 950/950 ProRacer/1025/1050/1055
Direct Drive
long. This can be caused by a bad contactor, motor con-
trol board or a bad PCB. See WHEEL DOES NOT STOP.
Err 6 -
Displayed when there is no power to the
LEDs on the encoder. This can be caused by a defective
encoder or PCB, or improper encoder wiring. See
OPTICAL ENCODER CHECKING PROCEDURE.
Err 7 -
Displayed when a time out occurs within the
software. This can be caused by noise interference in
the encoder circuit causing a signal sequencing error.
Check for a defective ground circuit or line filter prob-
lem.
Note: The machine should be on a dedicated
circuit.
Err 8 -
Displayed when The most likely cause is noise
interference. Check for a defective encoder cable, or
defective PCB. Check for a defective ground circuit or
line filter problem.
Note: The machine should be on a dedicated
circuit.
Err 9 -
This message is displayed when the speed of
the wheel has decreased at too fast a rate. This could
occur if the machine is extremely cold and a small
wheels mounted on the shaft.
Err 10 -
This message is displayed when a sequence
error has occurred with the calibration of the A & D
arm. See the A & D ARM CALIBRATION PROCEDURE.
Err 11 -
This message is displayed when an unac-
ceptable A dimension was entered during the A & D
arm calibration process. See the A & D ARM CALI-
BRATION PROCEDURE.
Err 12 -
This message is displayed when an unac-
ceptable D dimension was entered during the A & D
Arm calibration process. See the A & D ARM CALI-
BRATION PROCEDURE.
Err 13 -
This message is displayed when the A pot is
not adjusted properly. See REPAIR PROCEDURES FOR
A & D ARM ASSEMBLY.
Err 14 -
This message is displayed when the D pot
is not adjusted properly. See REPAIR PROCEDURES
FOR A & D ARM ASSEMBLY.
Err 15 -
*Displayed when the motor has gone over-
speed prior to breaking. This could be caused by a
defective PCB, encoder, contactor or motor control
board, or incorrect wiring of either of the previous.
*Function Codes
The following is a list of function codes with it’s
description. Codes are entered into the balancer by
pressing and holding the SHIFT key and then pressing
and releasing the zero (0) key. At this time CDE will
appear in the left weight display. The two digit code is
then entered and appears in the right weight display.
There is a slight delay after the second digit is entered
at which time the display blanks temporarily and the
code is executed. There is approximately a 10 second
window from the time CDE appears for the operator to
enter the 2 digit code. If the code is not entered in this
time, the code entry routine will automatically be ter-
minated.
10
Calibrate the A & D arm.
20
Toggle stop-on-top ON or OFF.
21
Calibrate stop-on-top.
40
Displays the software revision on the weight dis-
play. The revision letter(s) is/are shown on the left dis-
play and the revision level is shown on the right weight
display.
41
Indicates presence or absence of A & D arm and
stop-on-top hardware as dictated by the electronics. If
there is no jumper connected between pins 15 and 17
on the 18 pin connector in the harness, the left display
will show AR to indicate an A & D arm is present. If
there is a jumper between these pins, the left weight
display will show NAR to indicate the absence of an A
& D arm. An analogous method is used for the stop-on-
top feature. If there is no jumper between pins 16 and
18, the right weight display will show SOT to indicate
the presence of the stop-on-top hardware; otherwise
the display will show NST. It should be noted that the
presence or absence of the arm and stop-on-top is not
detected directly so if the jumpers are improperly
installed, incorrect information will be displayed.
42
Keyboard Test -
After the code is entered all dis-
plays will be blank. When a key is pressed the number
of the key or a description of the function is activated
(MODE and SHIFT keys) is displayed on the wheel
parameter display. To exit the test, press and hold the
SHIFT key and press the zero (0) key.
43
Display Test -
All display segments are turned on
simultaneously including decimal points and individual
LED's. The test may be terminated by pressing and
holding the SHIFT key and then pressing and releasing
the zero (0) key. If the test is not terminated manually it
will terminated automatically.
44
Encoder TEST -
The encoder count is displayed on
the right weight display and the left display is blanked.
The count should be zero (0) when the top-dead-center
Содержание COATS 1025
Страница 2: ...ii Service Manual COATS Models 950 950 ProRacer 1025 1050 1055 Direct Drive ...
Страница 33: ...Service Manual COATS Models 950 950 ProRacer 1025 1050 1055 29 Direct Drive 950 Pro Racer Wiring Diagram ...
Страница 34: ...30 Service Manual COATS Models 950 950 ProRacer 1025 1050 1055 Direct Drive 950 Wiring Diagram Contactor Style ...
Страница 37: ...Service Manual COATS Models 950 950 ProRacer 1025 1050 1055 33 Direct Drive Mechanical Hood Switch Diagram ...
Страница 39: ...Service Manual COATS Models 950 950 ProRacer 1025 1050 1055 35 Direct Drive ...
Страница 41: ...Service Manual COATS Models 950 950 ProRacer 1025 1050 1055 37 Direct Drive ...
Страница 48: ...9111123 03 11 05 Copyright 1992 Hennessy Industries and COATS All Rights Reserved Printed in USA ...