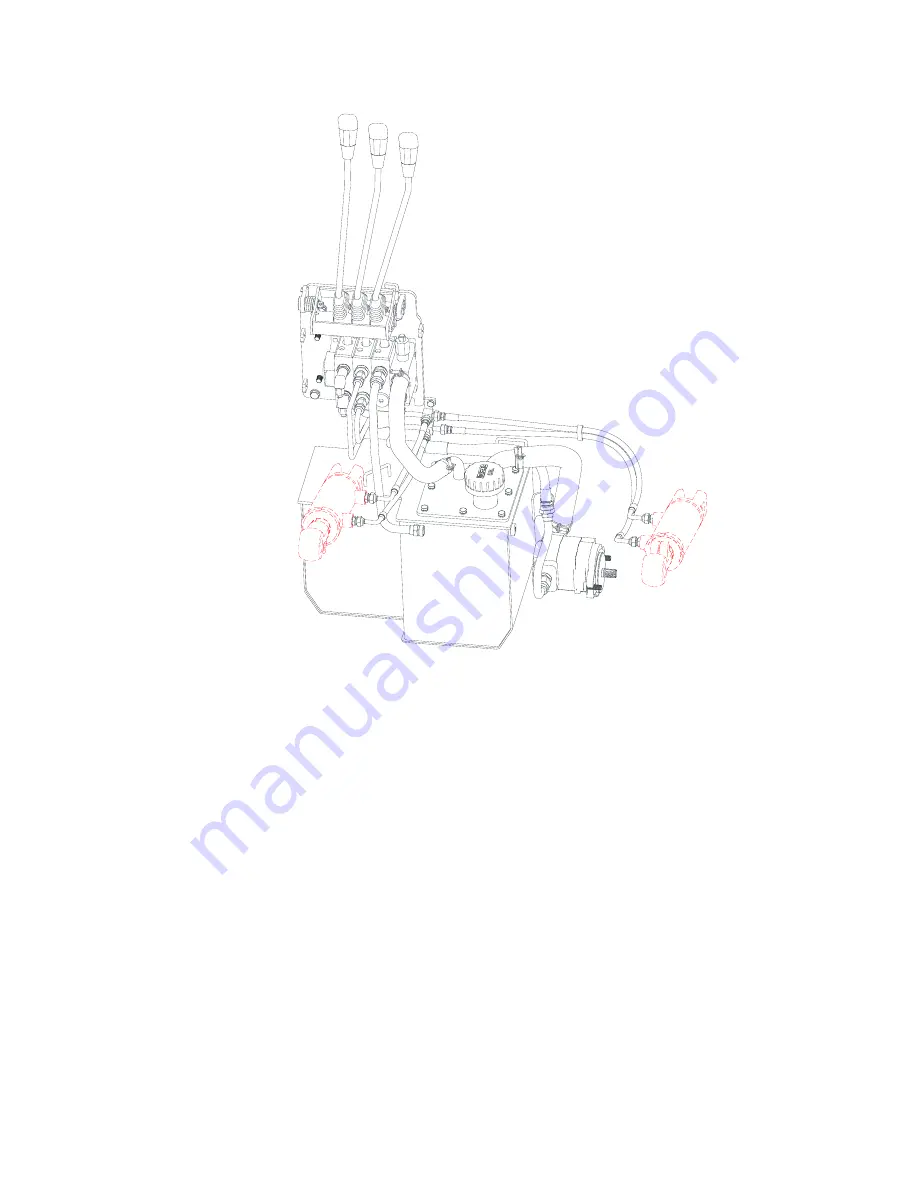
74
Figure 5-21 Hydraulic pipeline
5.2 Maintenance
,
Fault Analysis and Remedies
5.2.1 Maintenance
Check if there is any seepage and serious oil leakage on the pipe fittings of hydraulic
drive system, hoist cylinder, tilt cylinder, oil pump, before and after each shift. Check if
the working oil inside work oil tank is sufficient and check and clean the strainer mesh of
oil filter mounted in the work oil tank once every week.
Normally, change the oil in the work oil tank once every 1200-1500 hours of work
and mixed use of oils of different brands is not allowed.
5.2.2 Maintenance of lift pump
(1) Disassembly
Содержание CPD15
Страница 1: ......
Страница 9: ...7 Ⅱ Main Specifications of Forklift Truck Enternal view of forklift trucks ...
Страница 28: ...26 Figure 4 1 Electric system principle diagram CPD15SQ 20SQ GB2Li 1M1 2M1 μ ú é è ...
Страница 32: ...30 Figure 4 5 CPD15SQ GB2Li control device assembly ...
Страница 33: ...31 Figure 4 6 CPD16SQ GB2Li control device assembly ...
Страница 34: ...32 Figure 4 7 CPD18 20SQ GB2Li control device assembly ...
Страница 90: ......