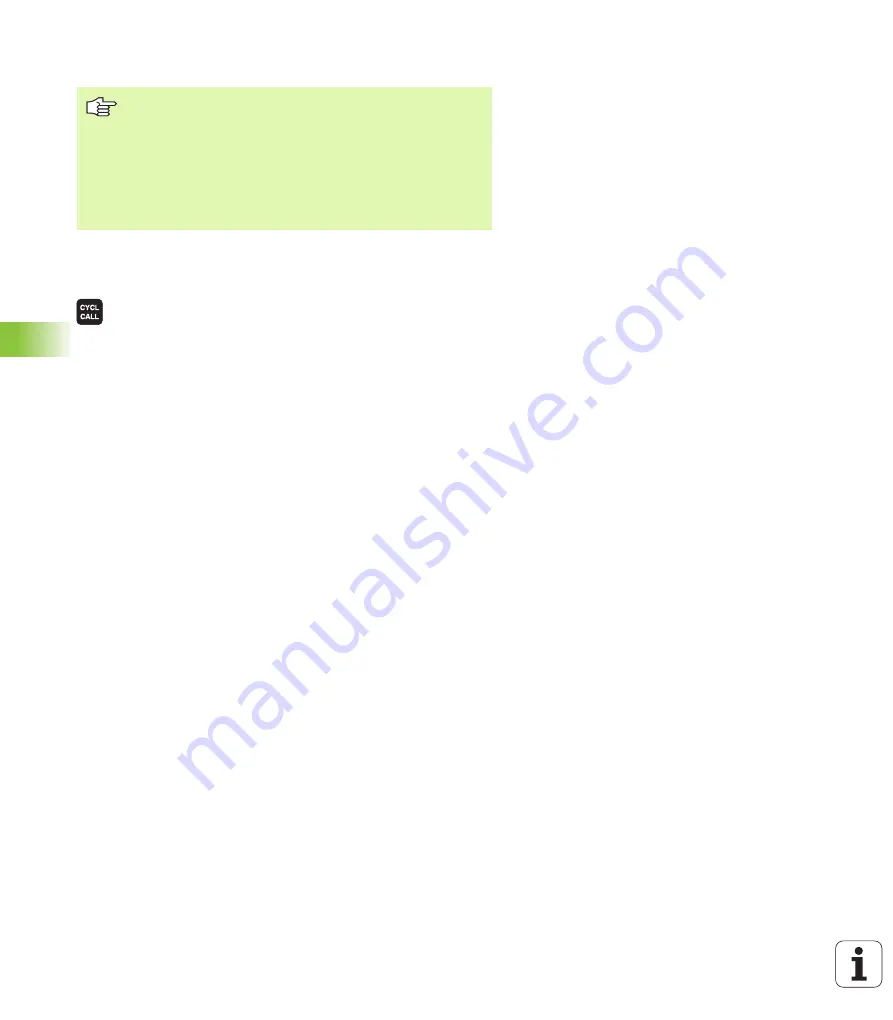
8 Programming: Cycles
8.2 P
o
int
T
a
bles
Calling a cycle in connection with point tables
If you want the TNC to call the last defined fixed cycle at the points
defined in a point table, then program the cycle call with
CYCLE CALL
PAT
:
U
To program the cycle call, press the CYCL CALL key.
U
Press the CYCL CALL PAT soft key to call a point
table.
U
Enter the feed rate at which the TNC is to move from
point to point (if you make no entry the TNC will move
at the last programmed feed rate, FMAX not valid).
U
If required, enter miscellaneous function M, then
confirm with the END key.
The TNC moves the tool back to the safe height over each successive
starting point (safe height = the spindle axis coordinate for cycle call).
To use this procedure also for the cycles number 200 and greater, you
must define the 2nd set-up clearance (Q204) as 0.
If you want to move at reduced feed rate when pre-positioning in the
spindle axis, use the miscellaneous function M103 (see “Feed rate
factor for plunging movements: M103” on page 183).
Effect of the point tables with Cycles 1 to 5, 17 and 18
The TNC interprets the points of the working plane as coordinates of
the hole centers. The coordinate of the spindle axis defines the upper
surface of the workpiece, so the TNC can pre-position automatically
(first in the working plane, then in the spindle axis).
Effect of the point tables with SL cycles and Cycle 12
The TNC interprets the points as an additional datum shift.
Effect of the point tables with Cycles 200 to 208 and 262 to 267
The TNC interprets the points of the working plane as coordinates of
the hole centers. If you want to use the coordinate defined in the point
table for the spindle axis as the starting point coordinate, you must
define the workpiece surface coordinate (Q203) as 0.
Effect of the point tables with Cycles 210 to 215
The TNC interprets the points as an additional datum shift. If you want
to use the points defined in the point table as starting-point
coordinates, you must define the starting points and the workpiece
surface coordinate (Q203) in the respective milling cycle as 0.
With
CYCL CALL PAT
the TNC runs the points table that you
last defined (even if you have defined the point table in a
program that was nested with
CALL PGM
.
The TNC uses the coordinate in the spindle axis as the
clearance height, where the tool is located during cycle
call. A clearance height or 2nd setup clearance that is
defined separately in a cycle must not be greater than the
clearance height defined in the global pattern..
Содержание TNC 426
Страница 3: ......
Страница 4: ......
Страница 8: ...IV...
Страница 10: ...VI...
Страница 26: ......
Страница 27: ...1 Introduction...
Страница 41: ...2 Manual Operation and Setup...
Страница 54: ......
Страница 55: ...3 Positioning with Manual Data Input MDI...
Страница 59: ...4 Programming Fundamentals of NC File Management Programming Aids Pallet Management...
Страница 122: ......
Страница 123: ...5 Programming Tools...
Страница 153: ...6 Programming Programming Contours...
Страница 201: ...7 Programming Miscellaneous functions...
Страница 226: ......
Страница 227: ...8 Programming Cycles...
Страница 366: ......
Страница 367: ...9 Programming Subprograms and Program Section Repeats...
Страница 381: ...10 Programming Q Parameters...
Страница 424: ......
Страница 425: ...11 Test run and Program Run...
Страница 443: ...12 MOD Functions...
Страница 472: ......
Страница 473: ...13 Tables and Overviews...
Страница 496: ......