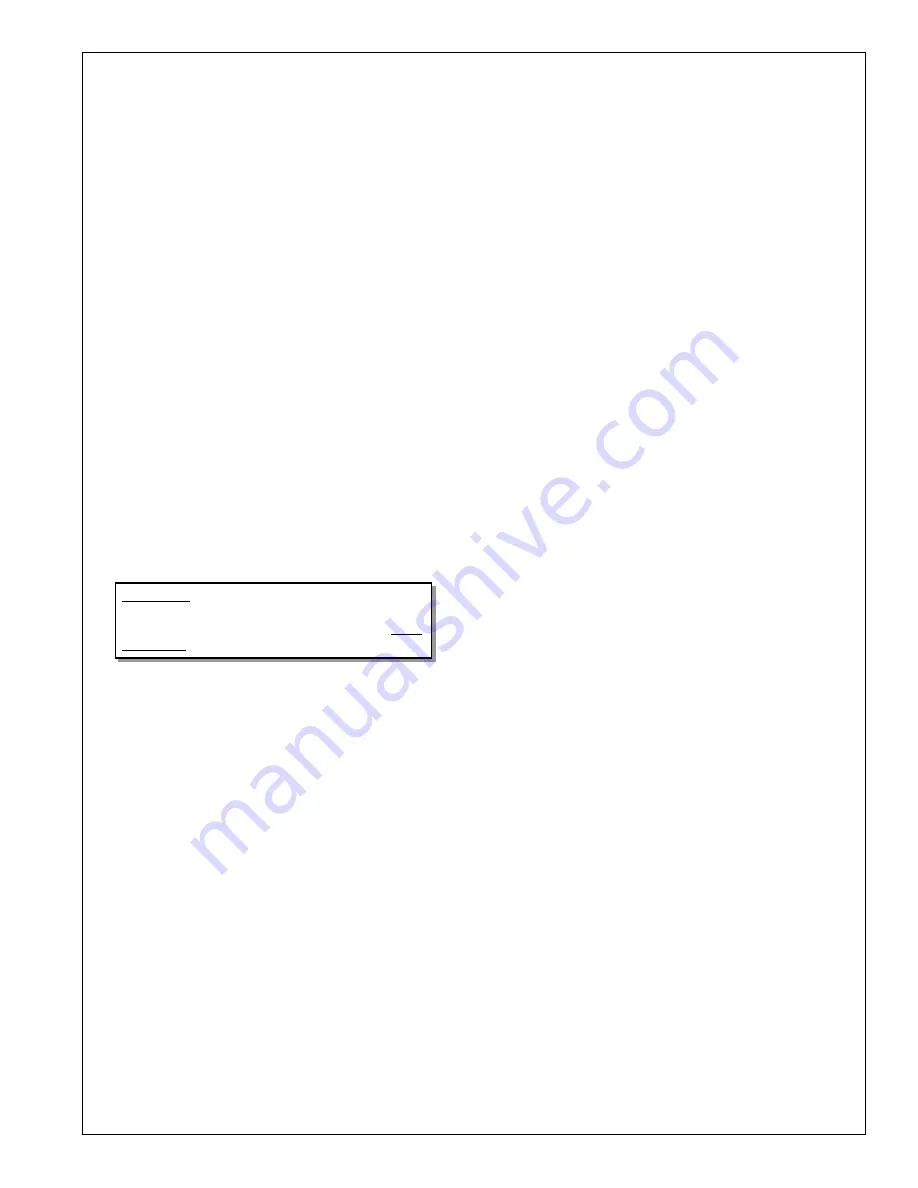
19
Electronic control system
The electronic controller has become the standard on parallel
compressor systems. The increased capabilities of the
controllers magnify the efficiency of the parallel compressor
system making it a very attractive accessory item.
The electronic control system preferred by Heatcraft is the
Computer Process Control (RMCC) controller. The RMCC
offers a complete control and monitoring package through
one or more input boards (16AI). The controller continuously
monitors the parameters for refrigerant pressures, defrost
operation, temperature control, and system alarms.
As the RMCC monitors the system in operation, it compares
the reported values against programmed set points it is to
maintain, thus cycling compressors, unloaders, condenser
fans, defrost periods and sounding alarms as required.
Interface with the actual devices being controlled is through
one or more pressure transducers, watt transducer,
temperature sensors, refrigerant sensors, humidity sensors,
refrigerant level sensor, phase loss, and output boards (8R0).
The 8RO boards can be mounted remotely for lower
installation cost, when controlling devices such as air cooled
condensers. These boards are connected to the RMCC via a
three wire network and are purchased as needed for the
application. Remote communications capabilities is standard
with the RMCC through a modem that is supplied.
System Balancing
Important: In order to obtain the maximum
capacity from a system, and to ensure trouble-
free operation, it is necessary to balance each
and every system.
System Superheat
This is extremely important with any refrigeration system.
The critical value that must be checked is suction
superheat.
Superheat is not preset at the factory.
Suction superheat should be checked at the compressor as
follows:
1. Measure the suction pressure at the suction
service valve of the compressor and determine
the saturation temperature corresponding to
this pressure from a “Temperature-Pressure”
chart.
2. Measure the suction temperature of the
suction line about one foot back from the
compressor using an accurate thermometer.
3. Subtract the Saturated temperature from the
actual suction line temperature. The difference
is Superheat.
If suction superheat is too low, it can result in liquid refrigerant
being returned to the compressor. This will cause dilution of
the oil and eventual failure of the bearings and piston rings.
In extreme cases, the compressor will fail as a result of the
diluted oil.
High suction superheat will result in excessive discharge
temperatures that can cause a breakdown of the oil. This
action results in piston ring wear, piston and cylinder wall
damage.
Also, as the superheat increases, the suction pressure
decreases resulting in reduced capacity. For maximum
system capacity, suction superheat should be kept as low as
is practical. HEATCRAFT recommends that the superheat at
the compressor be no lower than 20
°
F.
If adjustments to the suction superheat need to be made, the
expansion valve at the evaporator should be adjusted. See
instructions in next section.
Evaporator Superheat
Check Your Superheat after the box temperature has reached
or is close to reaching the desired temperature, the
evaporator superheat should be checked and adjustments
made if necessary. Generally, systems with a design TD of
10
°
F should have a superheat value of 6
°
to 10
°
F for
maximum efficiency.
To properly determine the superheat of the evaporator, the
following procedure is the method Heatcraft recommends.
1. Measure the temperature of the suction line at
the point the bulb is clamped.
2. Obtain the suction pressure that exists in the
suction line at the bulb location by either of the
following methods:
a) A gauge in the external equalized line
will indicate the pressure directly and
accurately.
b) A gauge directly in the suction line near
the evaporator or directly in the suction
header of the evaporator will yield the
same reading as above.
3. Convert the pressure obtained in 2a or 2b
above to saturated evaporator temperature by
using a temperature-pressure chart.
4. Subtract the Saturated temperature from the
actual suction line temperature. The difference
is Superheat.
Alternative Superheat Method
The most accurate method of measuring superheat is found
by following the previous procedure, Temperature / Pressure
method. However, that method may not always be practical.
An alternative method which will yield fairly accurate results is
the temperature / temperature method.
1. Measure the temperature of the suction line at
the point the bulb is clamped (outlet).
2. Measure the temperature of one of the
distributor tubes close to the evaporator coil
(inlet).
3. Subtract the outlet temperature from the inlet
temperature. The difference is approximate
Superheat.
This method will yield fairly accurate results as long as the
pressure drop through the evaporator coil is low.