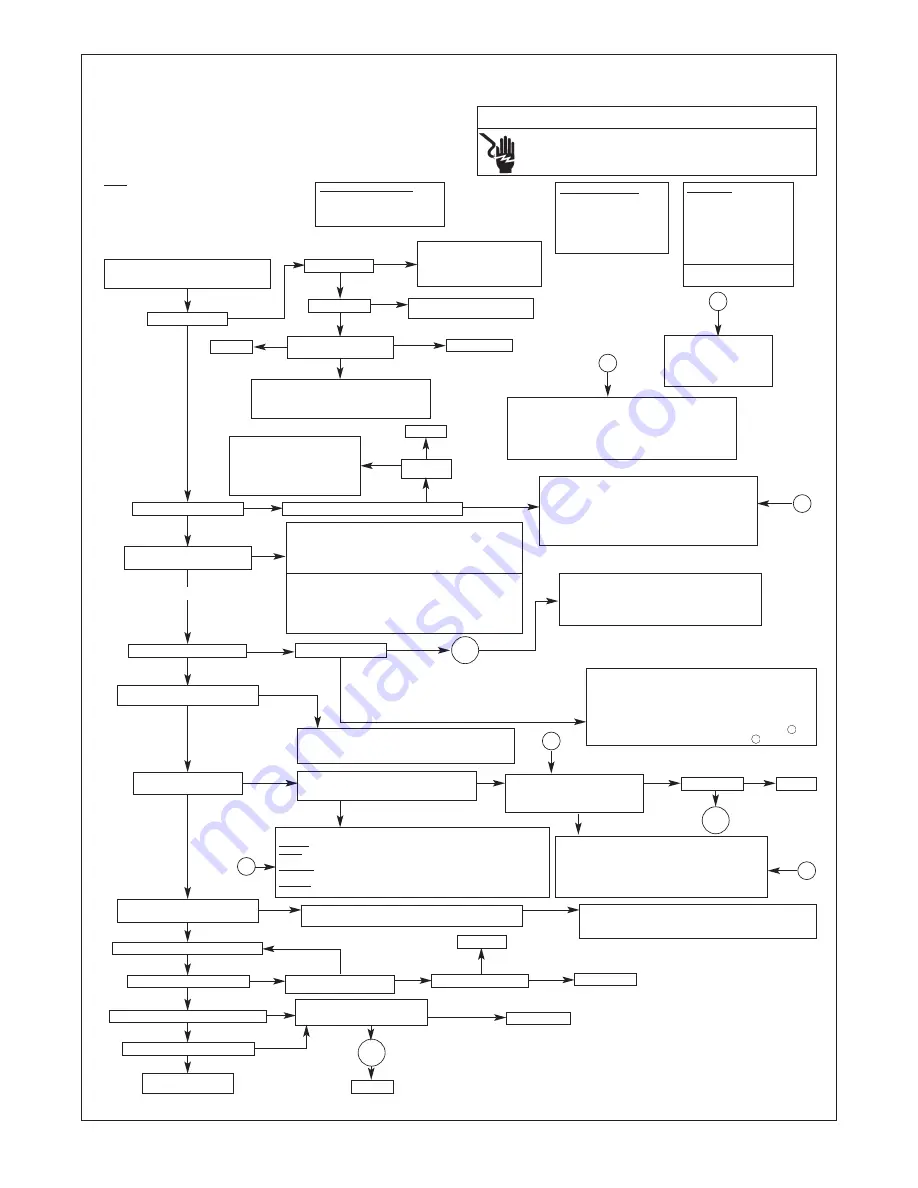
FIGURE 27
TROUBLESHOOTING FLOWCHART
GO TO
E
WARNING
INTEGRATED FURNACE CONTROL (IFC)
TROUBLESHOOTING GUIDE
HAZARDOUS VOLTAGE
LINE VOLTAGE
CONNECTIONS
DISCONNECT POWER BEFORE SERVICING.
SERVICE MUST BE BY A TRAINED, QUALIFIED
SERVICE TECHNICIAN.
NOTE: Most failures are not due to the IFC. Double check all other
possibilities, including the ground connection, before replacing the IFC.
NOTE: Always verify gas valve inlet and outlet gas
pressure.
KEY TO ABBREVIATIONS
IBM = Indoor Blower Motor
IDM = Induced Draft Motor
IFC = Integrated Furnace Control
PS = Pressure Switch(es)
SE = Spark Electrode
HSI = Hot-Surface Ignition
DSI = Direct-Spark Ignition
FLAME (AMBER) LED CODES
OFF = No Flame Present
RAPID BLINK = Unexpected Flame
SLOW BLINK = Marginal Flame Sense
STEADY ON = Normal Flame Sense
BLINK CODES (GREEN LED)
1 Blink - Soft lockout
Reset System power and
start over from beginning
2 Blinks - PS Circuit open
go to point “F.”
3 Blinks - Limit circuit open
go to point “D.”
4 Blinks - PS Circuit closed
Go to point “G.”
5 Blinks - Twin Fault (Optional)
*Go to point “H.”
1) Set FAN switch to “AUTO”
2) Set thermostat to call for heat (set temp. differ-
ential to greater than 10°F
Does the IDM Energize?
IDM Runs for 30 sec. pre-purge?
Spark Ignitor Electrode (SE) Energizes
or HSI Ignitor Glowing?
Does Main Burner Light and stay lit?
Is the gas valve energized?
PS dropping out?
Check IFC*
Does IBM start on heat speed 20 seconds
after burners light?
Does main burner remain lit until
heat call ends?
Does thermostat maintain reasonable room
temperature near setpoint?
Set thermostat to off position (W to C = ØV)
Does gas valve shut off immediately?
Does IDM shut off after ten second post-purge?
Does IBM shut off after a max. of 3 min?
END
Heat-mode troubleshooting
“POWER” LED ON?
24V on W to IFC?
Is “STATUS” LED blinking,
steady-on, or off?
Check IFC*.
Check IFC*.
Does IDM run
indefinately.
Does IDM Run for 60 sec. and then off for Five minutes
- Check thermostat in “heat” mode,
battery, wire, and connections.
SEE BLINK CODES
- Check 24V at IFC.
- Check Fuse.
- Check Door Switch and Line Power.
- Check Transformer.
- Check Breaker.
- Check PS contacts
- Check wires for short.
- Check IFC*.
- Check switches and hoses for
water or moisture
- For Twinned units, check that both IFCs are set for “TWIN” and wires
are connected between “TWIN” terminals.
- Check IFC*.
- For twinned units, ensure transformers are in phase.
(if out of phase, flame LED will be dim).
- For non-twinned units, ensure “TWIN” is in the single (OFF) position.
- For Twinned units – ensure both IFC‘s have same part number.
- Check PS, PS Hoses, and wires.
- Check for blocked vent, excessive vent length or elbows, or
blocked heat exchanger.
- Check IDM wired correctly.
- Ensure against excessive wind, which can open pressure switch.
- If downflow 90+, check aux. limit – shoud be closed
- Check for intermittent P.S. operation.
- Check switches and hoses for water or moisture.
- Check gas supply and manifold pressure.
- Ensure L1 and Neutral not swapped on IFC and junction box.
- Check SE alignment.
- Check orifice or other restrictions to gas flow.
- Check flame sense rod (clean with sandpaper).
- Check flame carry over.
- Check wires, continuity, and connection between IFC and gas valve.
- Ensure 24 V between appropriate pins on connector of IFC.
- Ensure manual switch on valve is in the “ON” position.
- 90+ check aux. limit open? Should be closed
- 90+ upflow models – check drain pressure switch between IFC and
gas valve – should be closed – replace drain pressure switch if drain
is not blocked or clear drain if blocked.
- Did a pressure switch open during ignition trial? If yes, go to F
- Did a limit open during ignition trial? If yes, go to D
- Check line voltage between “HEAT” and “NEUTRAL” on IFC.
- Check wires, connections, and continuity between IFC and IBM.
- Check IBM capacitor.
- Check IBM.
CHECK:
- grounding on IFC and unit.
- check for proper polarity between L1 & neutral.
- flame sense rod (clean if necessary).
- wire continually between flame sense rod and appropriate pin of
connector on IFC
- flame carries across all burners, and all burners stay lit.
CHECK:
AIRFLOW - ensure no restrictions, such as dirty filter, dampers, closed registers, etc.
LIMITS - ensure good wire and connections between IFC and all limits. Make sure
limits are not open when circulating air temperature is within a specified range.
ROLLOUTS - ensure rollouts or overtemperature limits do not need to be reset. Make
sure no flame rollout in burner compartment due to blocked flu or heat exchanger.
OVERFIRE - ensure furnace is not overtemperature (temp rise is above stated range).
Check gas valve, proper orifice size, gas pressure, etc.
Is Limit circuit or IDM wire through aux. limit open or
opening and closing?
Note: IFC Status LED should be blinking a Fault Code 3.
Is the IFC sensing a good flame: NOTE:
Flame sense light should be steady-on
when burners are lit. If flame LED blinking,
or off, flame sense is low or absent.
Ensure thermostat is properly placed and not improperly affected by
registers, fans, sunlight, heat through walls, pipes, or wires in walls.
- Check heat anticipator setting. Furnace may need an isolation relay.
- Check installation instructions under section titled “Isolation Relay” for
details.
- Verify correct furnace sizing.
NOTE: If IFC goes into lockout (“STATUS LED will blink code “1”), shut
off main power to unit, wait 30 seconds and then reset power.
PROBLEM
STILL
PRESENT
“STATUS” LED
BLINKING
“FLAME” LED BLINKING
OR STEADY ON
If “E” did not
resolve issue
Double check - Is W off at IFC?
(W to C = ØV?)
Voltage present at gas valve?
- Check gas valve.
SEE BLINK CODES
- Check IFC*.
Check IFC*.
*Most failures are not due to the IFC. Double
check all other possibilities, including the
ground connection or wire connections, before
replacing the IFC.
Ensure TSTAT is not in “FAN” position.
Is “STATUS” LED blinking?
Is “FLAME” LED blinking or steady-on?
**System will attempt to light 4 times. Voltage
is present at gas valve for only 7 seconds dur-
ing each trial for ignition. The entire system will
go into a 1 hour lockout after 4 attempts. The
main blower and IDM will run 180 seconds
between 2nd and 3rd ignition attempts.
- Check line voltage at IDM.
- Check wires and connections between IDM and IFC.
- Ensure line voltage on IDM pins of IFC connector.
- Check IDM capacitor (90+ only).
CHECK BLINK CODES
- Check for open limit or limit circuit.
- Check for intermittent PS operation.
- Check for vent restrictions.
- Ensure vent lengths not excessive or
too small diameter.
- Check for blocked heat exchanger.
FOR SPARK IGNITION
- Check SE wire & connections.
- Clean SE with sandpaper. Replace SE if necessary.
- If problem persists, check IFC*.
- Check SE gas and proper SE ground.
- Check SE wire for spark arcing to metal before electrode.
FOR HOT SURFACE IGNITION
- Check ignitor connected.
- Check ignitor wires.
- Check ignitor resistance. If open circuit, low or high resistance, replace.
- Check ignitor for fractures or cracking
- Check ignitor placement.
- If problem persists, check IFC*.
START
REPEAT THIS PROCEDURE UNTIL TROUBLE-FREE OPERATION IS OBTAINED.
NO
NO
NO
If “
I
” did not
resolve issue.
NO
NO
NO
NO
NO
NO
NO
NO
NO
NO
NO
NO
NO
NO
NO
BLINKING
YES
YES
YES
YES
YES
YES
YES
YES
YES
YES
YES
YES
YES
YES
YES
YES
YES
YES
STEADY-ON
I
D
F
H
E
G
YES
NO
YES
PREPURGE
IGNITION TRIAL
IBM “ON” DELAY
STEADY HEAT
END HEAT CALL
POST-PURGE
IBM “OFF” DELAY
STEADY OFF
NO
OFF
**
92-101654-01-00
GO TO
F
GO TO
I
PREPURGE
38
Содержание GMDA
Страница 40: ...40 CM 0810...