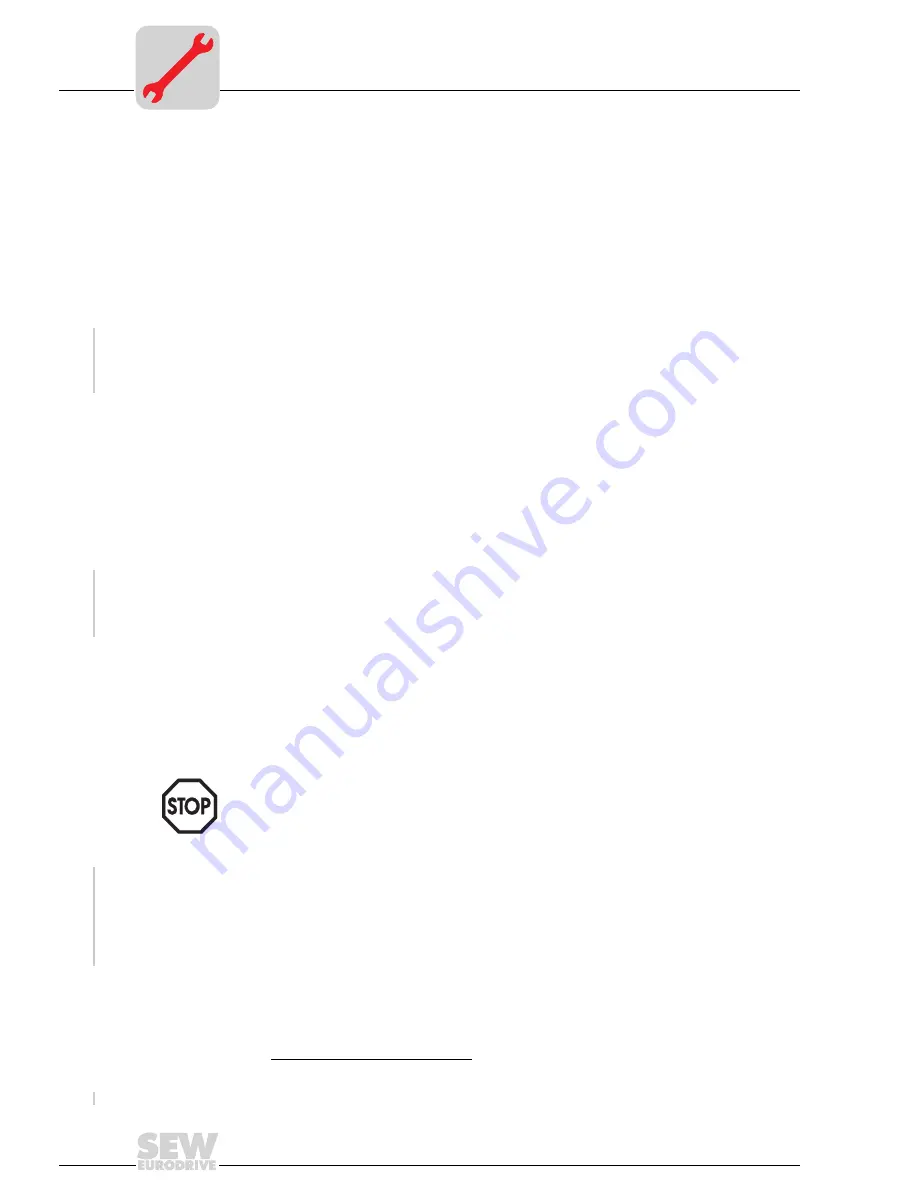
3
6
"R..7, F..7, K..7, S..7 , Spiroplan
®
W Gear Units" - Operating Instructions
Before you begin
3
Installation
3.1
Before you begin
The drive may
only be installed
if
•
the entries on the name plate of the drive match the mains power supply,
•
the drive is undamaged (no damage caused by transport or storage) and
•
it is certain that the following requirements have been fulfilled:
•
with standard gear units:
ambient temperature between 0 °C and +40 °C,
no oil, acid, gas, vapors, radiation, etc.,
•
with special versions:
drive configured in accordance with the ambient
conditions
•
with helical worm/Spiroplan
®
W gear units:
no large external mass moments of inertia which could exert a retrodriving load on
the gear unit
(where h’ (retrodriving) = 2 – 1/h < 0.5 self-locking)
3.2
Preliminary work
The output shafts and flange surfaces must be thoroughly cleaned of anti-corrosion
agents, contamination or such like (use a commercially available solvent). Do not let the
solvent come into contact with the sealing lips of the oil seals – danger of damage to the
material!
Please note: The service life of the lubricant in the bearings is reduced if the unit is
stored for more than one year.
Gear units of the “extended storage” type have
•
an oil fill suitable for the mounting position so the unit is ready to run (mineral oil).
Nevertheless, check the oil level prior to startup (see “Inspection / Maintenance” on
page 24).
•
a higher oil level with synthetic oil. Correct the oil level prior to startup (see “Inspec-
tion / Maintenance” on page 24).
3.3
Installing the gear unit
The gear unit or geared motor must be mounted/installed in the specified mounting po-
sition on a level
1)
, vibration-absorbing and torsionally rigid support structure (Spiroplan
®
gear units are not dependent on mounting position). Do not tighten housing legs and
mounting flanges against each other!
At this point of assembly, please check that the oil filling is as prescribed for the moun-
ting position (see "lubricant fill levels on page 49 or data on nameplate). In case of
mounting position change, adjust lubricant filling quantities accordingly. Please
consult our service department, if the mounting position for K gear units is changed to
M5 or M6 or within these mounting positions. Please consult our service department, if
the mounting position of S units in sizes S47 ... S97 is to be changed to mounting posi-
tion M2.
1) Maximum permitted flatness error for flange mounting (approximate values with refer-
ence to DIN ISO 1101): with
→
flange 120...600 mm max. error 0.2...0.5 mm
Oil check screws, drain screws and breather valves have to be freely accessible!