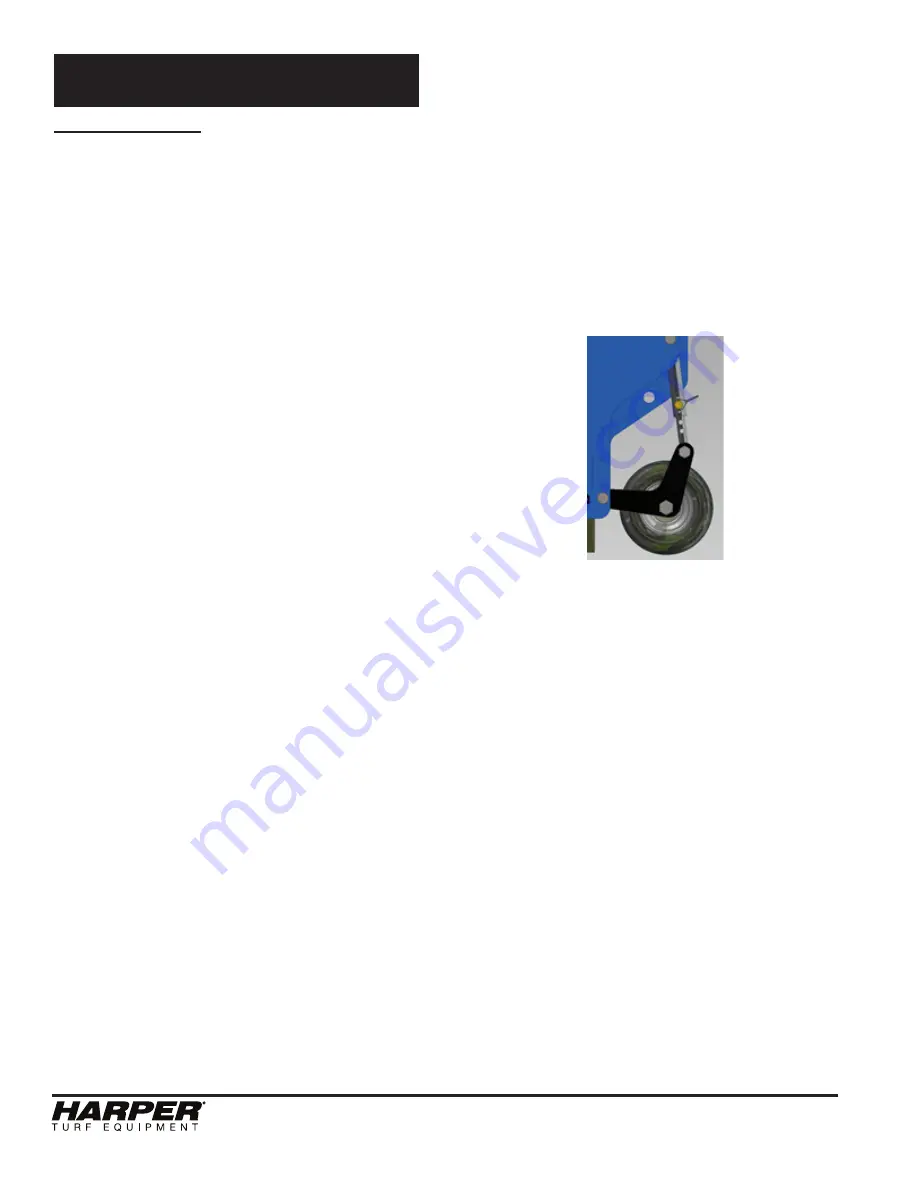
HK4400
Operation
Before Operation
Safety Checklist
□
Read and understand the Operator’s
Manual.
□
Ensure the machine is equipped with
safety stops for the hopper lift cylin-
ders and hopper door. Ensure that all
shields and guards are in place.
□
Check the seat belt to make sure that
it functions properly.
□
Know the location and function of all
controls and how to stop quickly in an
emergency. The machine controls are
identified in the previous Controls
Identification section.
□
Replace damaged or missing safety
decals.
Perform the Daily Maintenance Checklist.
□
Check engine oil level
□
Check hydraulic oil level
□
Check fuel level
□
Check engine coolant level
□
Visually inspect machine for fluid
leaks, loose hardware, damaged parts,
etc.
□
Check radiator/oil cooler and screen
for debris.
□
Check engine air cleaner intake
□
Grease as needed – see maintenance
section for grease locations and
intervals
□
Visually inspect tires to ensure proper
inflation
Setting the Sweeping Height
•
Park on level ground.
•
Start the machine and raise the deck
using the LH lever located on the
console.
•
Secure the deck using the deck lift
safety locks.
•
Adjust gauge wheel to desired height.
The deck height is set from the factory
in the middle hole of both the tube
and the rod. At this setting, a new
brush will contact the surface. To
adjust the brush to be more aggres-
sive, raise the gauge wheel to the next
set of holes that line up. To be less
aggressive, lower the gauge wheel to
the next set of holes that line up. The
adjustments are approximately ¼”
(.64 cm) increments. Set the gauge
wheel height the same on both sides.
•
Check the sweeping height. Repeat
the steps in this section until desired
sweeping height is determined.
Adjusting the Anti-Scalp Rollers
•
The anti-scalp rollers are set from
the factory so that the surface of the
roller is approximately 1” (2.5 cm)
below the front edge of the deck. To
adjust, remove the bolts and nuts
identified below and adjust up or down
accordingly. The rollers can be
adjusted in 3/8” (.95 cm) increments.
These are intended as anti-scalp
rollers only and not intended to roll on
the ground continuously.
14
Содержание 301012
Страница 1: ...HK4400 HK 4400 7 2020 OPERATOR S MANUAL SWEEPER Serial Number 20A01 Part 301012...
Страница 2: ...HK4400...