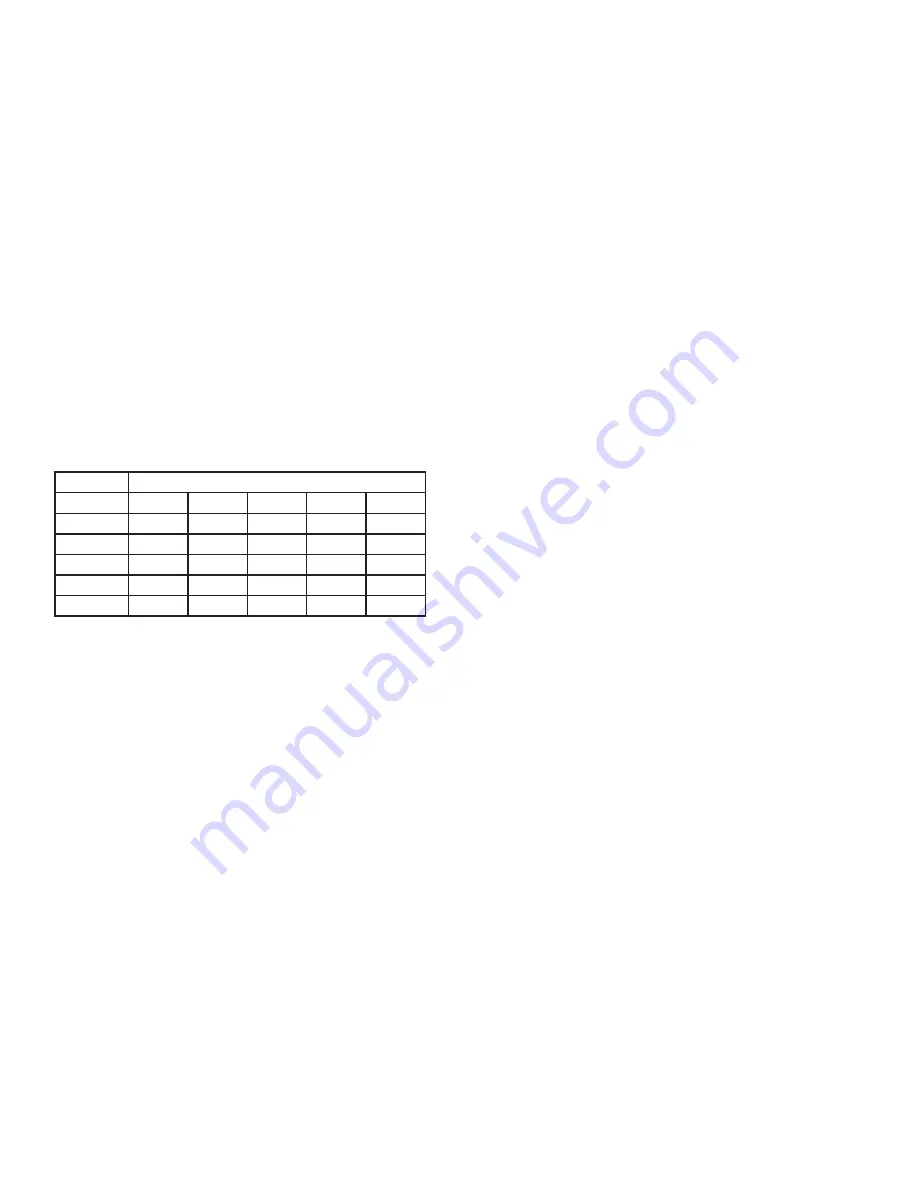
8
A100b
JAN 2009
SETTING ADJUSTMENTS OF SENSORS
There are several selectable features included in the
Hansen Gas Sensor. Refer to pages 6 and 7 for the
adjustable features. Note the adjustment screws on
the circuit board for the electrochemical sensor have
a different layout then the semiconductor sensor. The
jumpers may be moved without shutting off the power.
With the use of a 12-24V AC/DC power source, these
sensors can be set to the customers specifications
prior to mounting the gas sensor in the engine room or
refrigerated area.
Relay and Horn Set Point
The adjustment screw A sets the trip point for the relay
and the alarm horn. A 0-5V scale measures the full sensing
range of the Gas Sensor. The trip point voltage can be
measured at points ØV and REF1 located on the board.
Refer to pages 6 and 7 for location of the reference pin
REF1. A 100 PPM range gas sensor reading 2.5 volts at
the reference pin would be equivalent to half the range
or 50 PPM.
Default factor y setting is 50% of range.
Note that the set point of the relay is independent
of the set points to the Gas Detection Monitor.
To
assist in selecting the correct voltage for the desired
PPM set point, refer to
Table 1
below.
VOLTAGE
PPM R ANGE
5
100
250
500
3000
10,000
4
80
200
400
2400
8000
3
60
150
300
1800
6000
2
40
100
200
1200
4000
1
20
50
100
600
2000
.5
10
25
50
300
1000
TABLE 1
Setting Minimum or Maximum Relay Set Point
There is a practical limit for setting the minimum or
maximum relay set point. There is the tolerance of the
electronic board and the test meter. It is recommended
to keep the relay set point between 10% and 95% of
the range.
Time Delay
A time delay for the operation of the relay and alarm horn
can be selected using jumpers JP5 and JP6.
Default
factor y setting is zero.
Alarm Horn
Alarm horn is 40dB at 2 feet for Basic Sensor; all other
models not audible with cover closed. The alarm horn
can be disabled using jumper JP2.
Default factor y
setting is enabled.
Adjustment of the Detection Range
Adjustment Screw Z sets the zero (0 PPM) and Adjustment
Screw S sets the span. (full range = 1000PPM, for
instance). The output of the sensor circuit can be
monitored via test points ØV and VS. The full range
equals 5 volts DC. See
Calibration Procedures
for
fur ther details.
GAS SENSOR OPERATION
On power up the internal relay will energize switching
from the normally closed position to the normally open
position. In addition, the sensor will go through an
initial warm-up delay for five minutes. At this time, the
I and V outputs are 0. This is indicated by the green
LED flashing approximately ever y second. After five
minutes, the green LED stays on continuously, indicating
power to the gas sensor and ready for service. The gas
sensor also sends a milliamp output signal to the gas
detection monitor, PLC, or computer. This output signal
is propor tional to the amount of the specific gas being
monitored in the air around the gas sensor. If signal
reads 0.5mA, it is an indication the sensing element has
failed or disconnected. Verify proper installation and
refer to testing and calibration procedures.
Fail Safe Operation
Hansen Gas Sensors feature a one amp SPDT alarm
relay for fail safe operation. In the event of a sensor
element failure, power loss or gas leak detection, the
internal relay will be de-energized. This relay can be
used to trigger an external alarm.
Start Up Test
Once the installation of the gas sensors and monitors
is complete, the entire gas sensor system should be
tested. Normally, two people are required—one person
using a small amount of the target gas to “bump” each
sensor in turn, a second person at the monitor location
to verify the sensor is connected to the correct input,
responds to the target gas and causes the lights and
alarms to respond.
Gas Sensor Testing
Field testing of the gas sensor is normally done for three
reasons. The first is to determine if the gas sensor is
responding to the specific gas. This test is sometimes
called a “bump” test. The frequency of the test is usually
stated in the facilities Process Safety Management (PSM)
document, but not less than ever y six months.
The second reason for gas sensor testing is to be sure
the gas sensor is properly calibrated. Depending on the
sensing element type, the sensor sensitivity will change
with time. In par ticular, electrochemical sensors use a
material that is depleted with time. The length of time
varies depending on the amount of exposure to the target
gas, the ambient temperature and humidity, and changes
to temperature and humidity range. Atmospheres that
are ver y dr y or ver y humid will shor ten the life of a
sensing element.
The third reason is to be sure the gas sensor output
triggers the alarms on the monitor, PLC, Gas Alert System,
horn or lights. Gas sensors should be recalibrated at
least once a year or sooner where the gas sensor is
frequently exposed to low concentrations of the target
gas. Semiconductor and infrared sensors should be
checked annually. All sensor types should be recalibrated
immediately after exposure to a large concentration of
the target gas.
Note: Insurance companies, local and state agencies
may require more frequent testing and calibration;
refer to insurance carrier mandates as well as local
and state codes.
Calibration of Electrochemical Sensors
Read the calibration instructions completely before
proceeding. If in doubt about a procedure, please
contact Hansen Technologies for fur ther assistance.