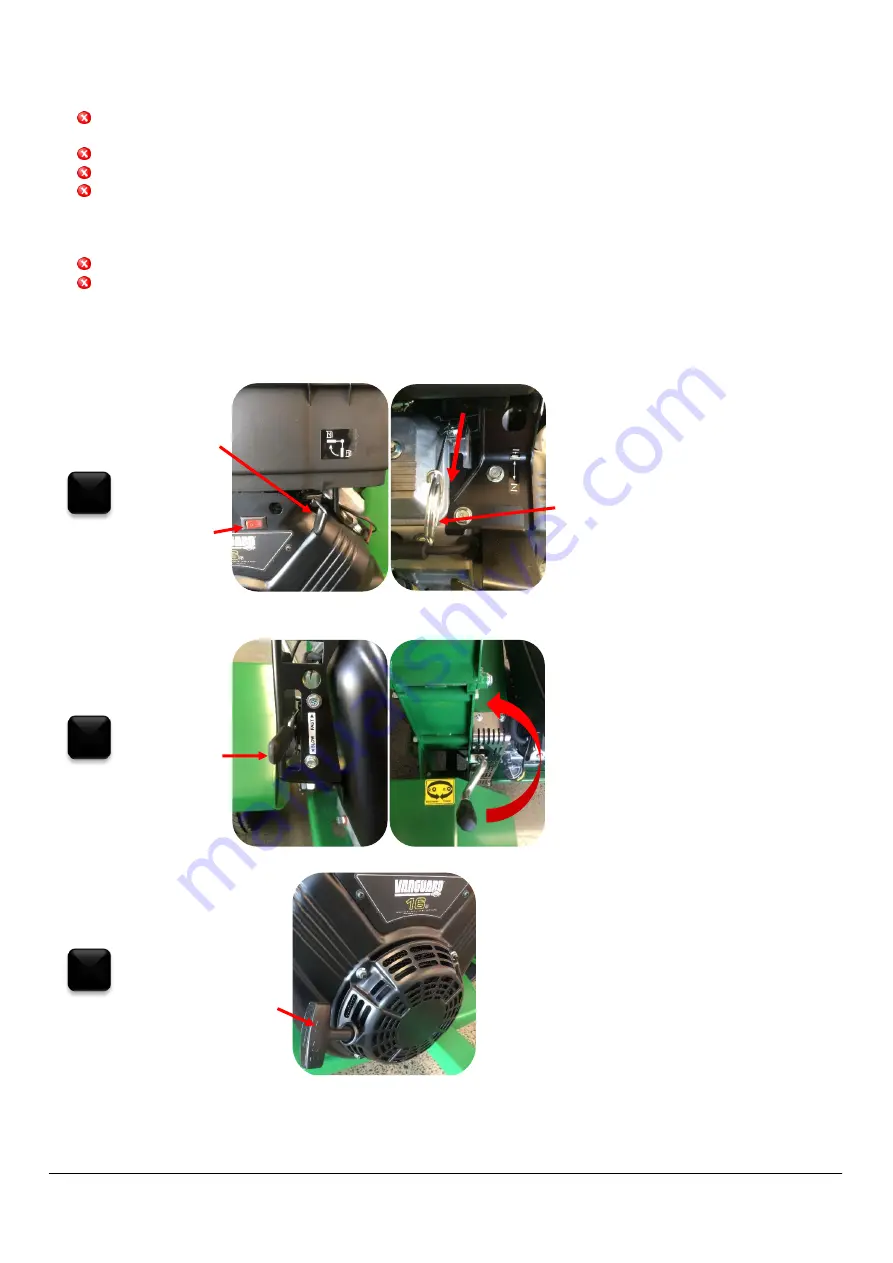
Hansa C16 O&M Manual - OM-009 Revision G 26/09/2019
© Hansa Chippers 2019
9
The governor controls the maximum safe operating speed and protects the engine and all moving parts from
damage caused by overspeed
Operate the chipper with blunt knives
This causes excessive vibration which may result in damage to the chipper
Move or tilt the chipper while it is running
Touch any guards or stick hands between guards while the chipper is running
Put hands or any other part of the body or clothing:
Inside the feed chute past the rubber flap
Inside or near the opening of the discharge chute
Near any moving part
Remove any guards on the chipper unless the engine is turned off and the cutting rotor has come to a complete standstill
Leave the chipper on while it is unattended
Starting procedure
Before proceeding, ensure the ‘safe setup procedure’ has been followed on page
7 of this manual.
Turn the fuel lever and
engine switch to the
“on” position
.
Pull the choke lever to
turn the choke on.
Turn the throttle to the halfway
position and disengage the belt
drive by winding the engagement
handle anti clock-wise until it
comes to a stop.
Pull the pull cord in one smooth
motion to start the engine.
1
1
2
3
Throttle
lever
(halfway
position)
Pull cord
Choke lever
(“on” position)
Fuel lever (“on”
position)
Engine
switch (“on”
position)