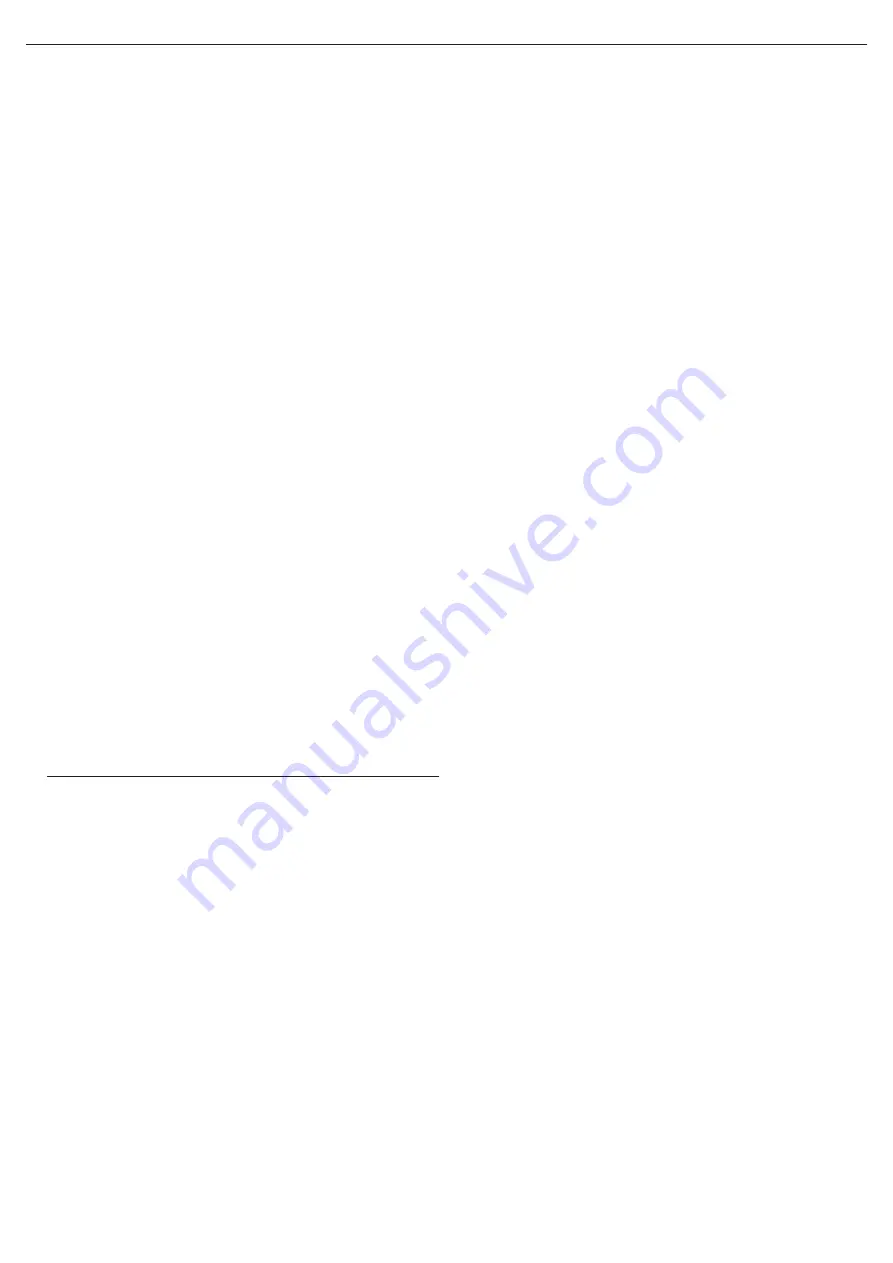
39
In-service tests
Purpose
The purpose of in-service tests is to regularly monitor and record the performance of
the thermostatic mixing valve. Deterioration in performance can indicate the need for
service work on the valve and/ or the water supplies.
Procedure
1.
Carry out the procedure
2.
(a) to (e) on page 39 using the same measuring
equipment, or equipment to the same specifications.
2.
If the mixed water temperature has changed significantly from the previous test
results (e.g. > 1 K), record the change and before re-adjusting the mixed water
temperature check:
a) that any in-line or integral strainers are clean
b) any in-line or integral check valves or other anti-backsiphonage devices are
in good working order
c) any isolating valves are fully open
3.
With an acceptable mixed water temperature, complete the procedure
2.
(a) to
(e) on page 39.
4.
If at step
2.
(e) on page 39 the final mixed water temperature is greater than the
values in Table A and / or the maximum temperature exceeds the corresponding
value from the previous test results by more than about 2 K, the need for service
work is indicated.
NOTE:
In-service tests should be carried out with a frequency which identifies a
need for service work before an unsafe water temperature can result. In the ab-
sence of any other instruction or guidance, the procedure described in „Frequency
of in-service tests“ may be used.
Frequency of in-service tests TMV3*
General
In the absence of any other instruction or guidance on the means of determining the
appropriate frequency of in-service testing, the following procedure may be used:
1.
6 to 8 weeks after commissioning carry out the tests given in 2. on page 39.
2.
12 to 15 weeks after commissioning carry out the tests given in 2. on page 39.
3.
Depending on the results of 1. and 4. several possibilities exist:
a) If no significant changes (e.g. < 1 K) in mixed water temperatures are recorded
between commissioning and 1., or between commissioning and 4. the next
in-service test can be deferred to 24 to 28 weeks after commissioning.
b) If small changes (e.g. 1 to 2 K) in mixed water temperatures are recorded
in only one of these periods, necessitating adjustment of the mixed water
temperature, then the next in-service test can be deferred to 24 to 28 weeks
after commissioning.
c) If small changes (e.g. 1 to 2 K) in mixed water temperatures are recorded in
both of these periods, necessitating adjustment of the mixed water temperature,
then the next in-service test should be carried out at 18 to 21 weeks after
commissioning.
d) If significant changes (e.g. > 2 K) in mixed water temperatures are recorded
in either of these periods, necessitating service work, then the next in-service
test should be carried out at 18 to 21 weeks after commissioning.
4.
The general principle to be observed after the first 2 or 3 in-service tests is that
the intervals of future tests should be set to those which previous tests have shown
can be achieved with no more than a small change in mixed water temperature.
*TMV2: The frequency of performing the in-service tests is 1 year
maximum.
Commissioning and in-service tests
Commissioning
Purpose
Since the installed supply conditions are likely to be different from those applied in the
laboratory tests it is appropriate, at commissioning, to carry out some simple checks
and tests on each mixing valve to provide a performance reference point for future
in-service tests.
Procedure
1.
Check that:
a) the designation of the thermostatic mixing valve matches the intended ap-
plication
b) the supply pressures are within the range of operating pressures for the
designation of the valve
c) the supply temperatures are within the range permitted for the valve and by
guidance information on the prevention of legionella etc.
2.
Adjust the temperature of the mixed water in accordance with the manufacturer’s
instructions (page 32) and the requirement of the application and then carry out
the following sequence:
a) record the temperature of the hot and cold water supplies
b) record the temperature of the mixed water at the largest draw-off flow rate
c) record the temperature of the mixed water at a smaller draw-off flow rate,
which shall be measured
d) isolate the cold water supply to the mixing valve and monitor the mixed water
temperature
e) record the maximum temperature achieved as a result of (d) and the final
stabilised temperature
NOTE:
The final stabilised mixed water temperature should not exceed the values
in Table A.
f) record the equipment, thermometer etc. used for the measurements
Table A: Guide to maximum stabilised temperatures recorded dur-
ing site tests
Application
Mixed water
temperature
Shower
43°C
Washbasin
43°C
Bath (44°C fill)
46°C
Bath (46°C fill)
48°C
The mixed water temperature at terminal fitting should never exceed 46ºC.
If there is a residual flow during the commissioning or the annual verification (cold
water supply isolation test), then this is acceptable providing the temperature of the
water seeping from the valve is no more than 2°C above the designated maximum
mixed water outlet temperature setting of the valve.
Temperature readings should be taken at the normal flow rate after allowing for the
system to stabilise.
The sensing part of the thermometer probe must be fully submerged in the water that
is to be tested.
Any TMV that has been adjusted or serviced must be re-commissioned and re-tested
in accordance with the manufacturers' instructions.