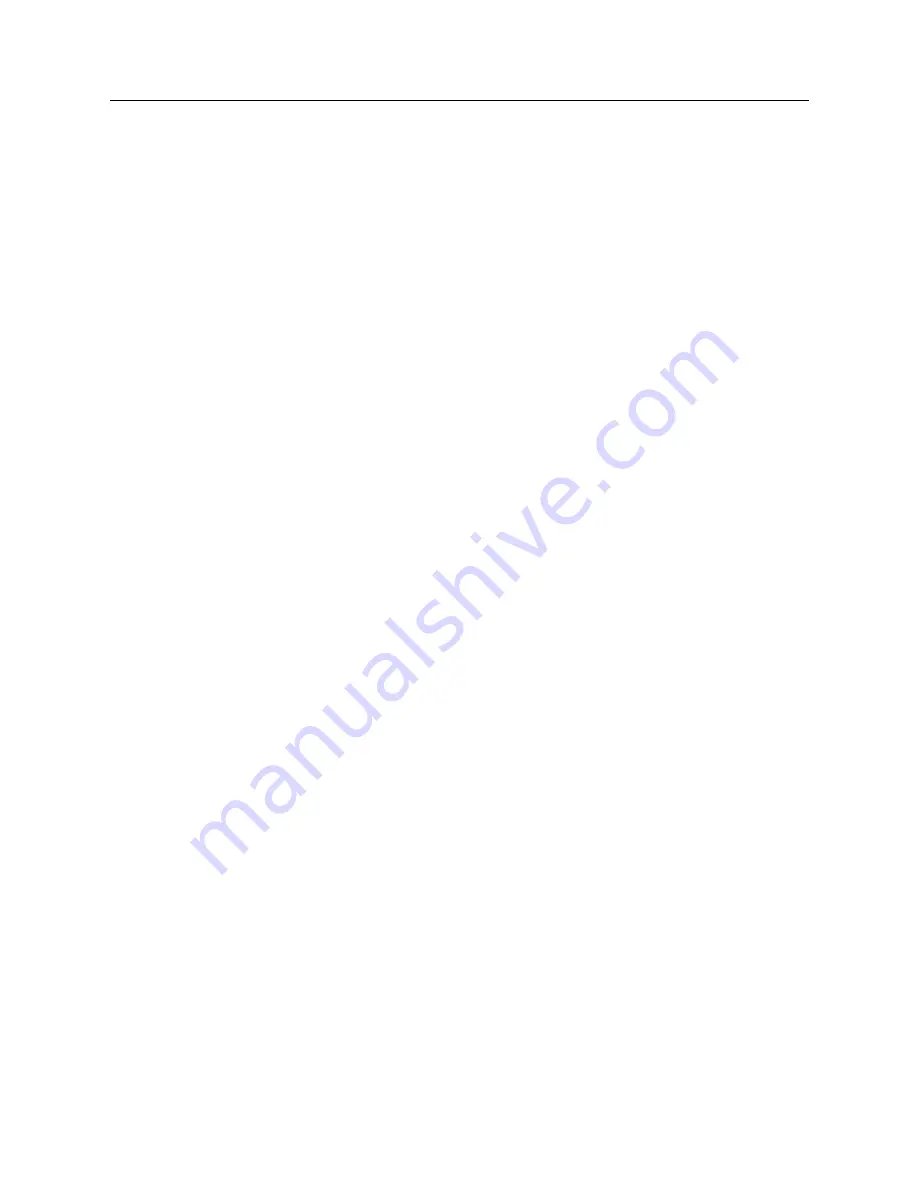
55
Range Testing Your Radio
Step 1.
Before each flying session be sure to range check your
radio. This is accomplished by turning on your transmitter with
the antenna collapsed. Turn on the radio in your airplane. With
your airplane on the ground, you should be able to walk 30
paces away from your airplane and still have complete control of
all functions. If not, do
not
attempt to fly! Have your radio
equipment checked out by the manufacturer.
Step 2.
Double check that all controls (aileron, elevator, throt-
tle, and rudder) move
in the correct direction.
Step 3.
Be sure that your batteries are fully charged per the
instructions included with your radio.
Adjusting the Engine
Step 1.
Completely read the instructions included with your
engine and follow the recommended break-in procedure. At the
field, adjust the engine to a slightly rich setting at full throttle
and adjust the idle and low speed needle so that a consistent
idle is achieved. Before you fly be sure that your engine reliably
idles , transitions, and runs at all throttle settings. Only when
this is achieved should any plane be considered ready for flight.
Pre-Flight at the Field