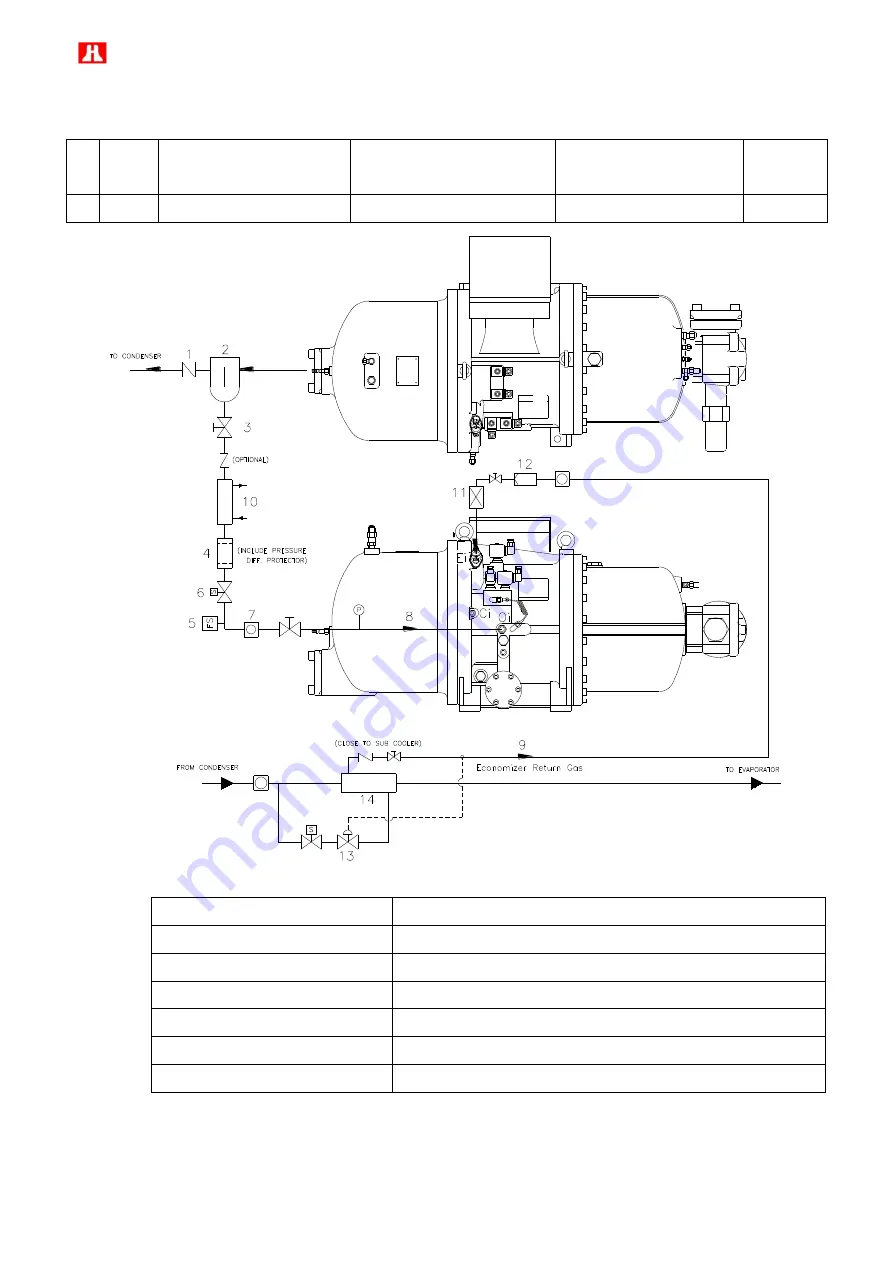
50
(2) Lubricant circuit, Liquid injection system and economizer connection diagram
Item
Oil
cooler
Oil injection into
compression chamber
Liquid injection into
compression chamber
Liquid injection for cooling
motor winding
Economizer
A
-
-
-
-
O
1.
Check valve
8.
To principal return oil port Oi
2.
External oil separator
9.
To medium pressure (Economizer return port) Ei
3.
Stop valve
10. Oil cooler
4.
Oil filter
11. Muffler
5.
Lubricant flow switch
12. Suction strainer
6.
Oil solenoid valve
13. Expansion valve
7.
Sight glass
14. Sub-cooler
Содержание RC2-F Series
Страница 6: ...5 2 2 Compressor outline...
Страница 7: ...6...
Страница 8: ...7...
Страница 9: ...8...
Страница 10: ...9...
Страница 11: ...10...
Страница 12: ...11...
Страница 13: ...12...
Страница 14: ...13...
Страница 15: ...14...
Страница 16: ...15...
Страница 17: ...16...
Страница 18: ...17...
Страница 19: ...18...
Страница 20: ...19...
Страница 21: ...20...
Страница 22: ...21...
Страница 23: ...22...
Страница 24: ...23...
Страница 25: ...24...
Страница 26: ...25...
Страница 27: ...26...
Страница 85: ...84 Horizontal External Oil Separator OS80 Horizontal External Oil Separator OS100 OS125 OS150...