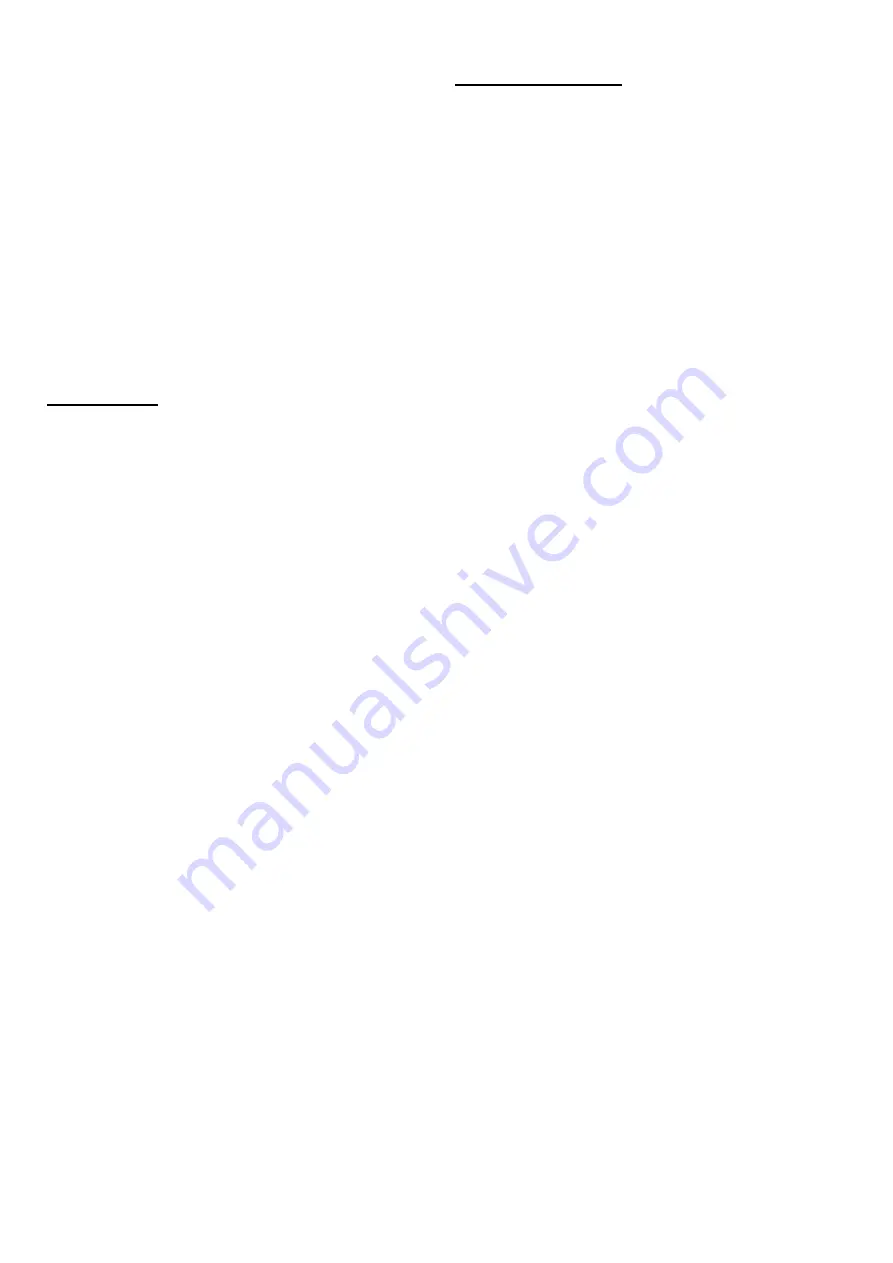
HAMWORTHY HEATING LTD
4
SHAFTESBURY HE
500001049/N
3.5 Minimum System Water Pressure
To comply with guidance note
PM5 (Health and Safety
Executive)
, the minimum pressure requirements at the
boiler are given below as examples :-
1)
Single installed boiler running at 82°C flow
temperature. Minimum head required is not less than 2
metres or 0.2 bar.
2)
Single installed boiler running at 95°C flow
temperature. Minimum head required = 5.1 metres or
0.5 bar.
See Section 8.9.1
3)
Modular boiler installation running at 82°C flow
temperature and 11°C rise across system. Minimum
head required = 4.3 metres or 0.42 bar.
4)
Modular boiler installation running at 82°C flow
temperature and 15°C rise across system. Minimum
head required = 9.4 metres or 0.92 bar. See
Section
8.10
for Pressurised Water Systems.
4.0 LOCATION
4.1
The boiler location must permit the provision of
a satisfactory flue system, and provide adequate
space around the boiler for servicing and air
circulation.
Sufficient space must be provided at the front of the
boiler to allow the removal of the burner assembly
for servicing/replacement, and at the rear for
installation of pipes, valves and flue.
Sufficient clearance around the boiler must also be
provided to allow access for servicing. Refer to
Figure 16.2
for recommended clearances.
The boiler room, or compartment, housing the boiler
(s) - whether specifically constructed for the
purpose, or a modification of an existing space -
should be in accordance with the requirements of
either BS.6644, or BS.5410 Part 2, as appropriate.
Where a separate purpose built boiler room is not
available, measures should be taken to protect the
boiler or boilers from damage, and the boiler should
be sited such that extraneous material cannot be
stored next to, or against it.
The boiler stands on a steel cradle and therefore it
requires installing on a suitable level non-
combustible surface, capable of withstanding
temperatures of 65
°
C and able to support the weight
of the boiler (including pipework and ancillary
equipment) when filled with water. A steel sheet
can be placed beneath the boiler cradle to facilitate
movement of the boiler during assembly. If a plinth
is required, it should be level, non-combustible,
50mm nominal height, and must be equal in width to
the boiler casing dimensions.
The compartment housing the boiler must have
permanent air vents communicating directly with the
outside air at both high and low level. Refer to
Section 7
for details.
5.0 GAS / OIL SUPPLY
5.1 Gas Service Pipes
The local gas region should be consulted at the
installation planning stage to either determine the
feasibility of providing a gas supply or, where there
is an existing supply, to ensure that the meter
capacity is adequate for the rated input of the
proposed new boiler. An existing gas service pipe
must not be used without prior consultation with the
local gas region.
5.2 Gas Meters
A new gas meter will be connected to the service pipe
by the local gas region, or a local gas region contractor.
An existing meter should be checked, preferably by the
gas region, to ensure that it is adequate to deal with the
rate of gas supply required.
5.3 Gas Supply Pipes
Supply pipes must be fitted in accordance with
BS 6891
or
IGE/UP/2
. Pipework from the meter to the boiler must
be of adequate size. Do not use pipes of a smaller size
than the boiler gas connection. The complete
installation must be purged and tested for soundness as
described in
BS 6891 or IGE/UP/1
and
IGE/UP/1A
as
appropriate.
A manual shut off valve must be fitted on the incoming
gas supply pipe, adjacent to each boiler, in an easily
accessible position.
5.4
Boosted Gas Supplies
Where it is necessary to employ a gas pressure
booster, the controls must include a low pressure cut-off
switch at the booster inlet. The local gas region must be
consulted before a gas pressure booster is fitted.
5.5 Boiler House Gas Control Valve
A manual valve for boiler house isolation shall be fitted
in the gas supply line. It shall be clearly identified and
readily accessible for operation, preferably by an exit.
5.6 Oil Supply
The oil storage and supply system should be
designed and installed in accordance with BS.5410
Part 2, as appropriate. The following notes are
given as guidance:-