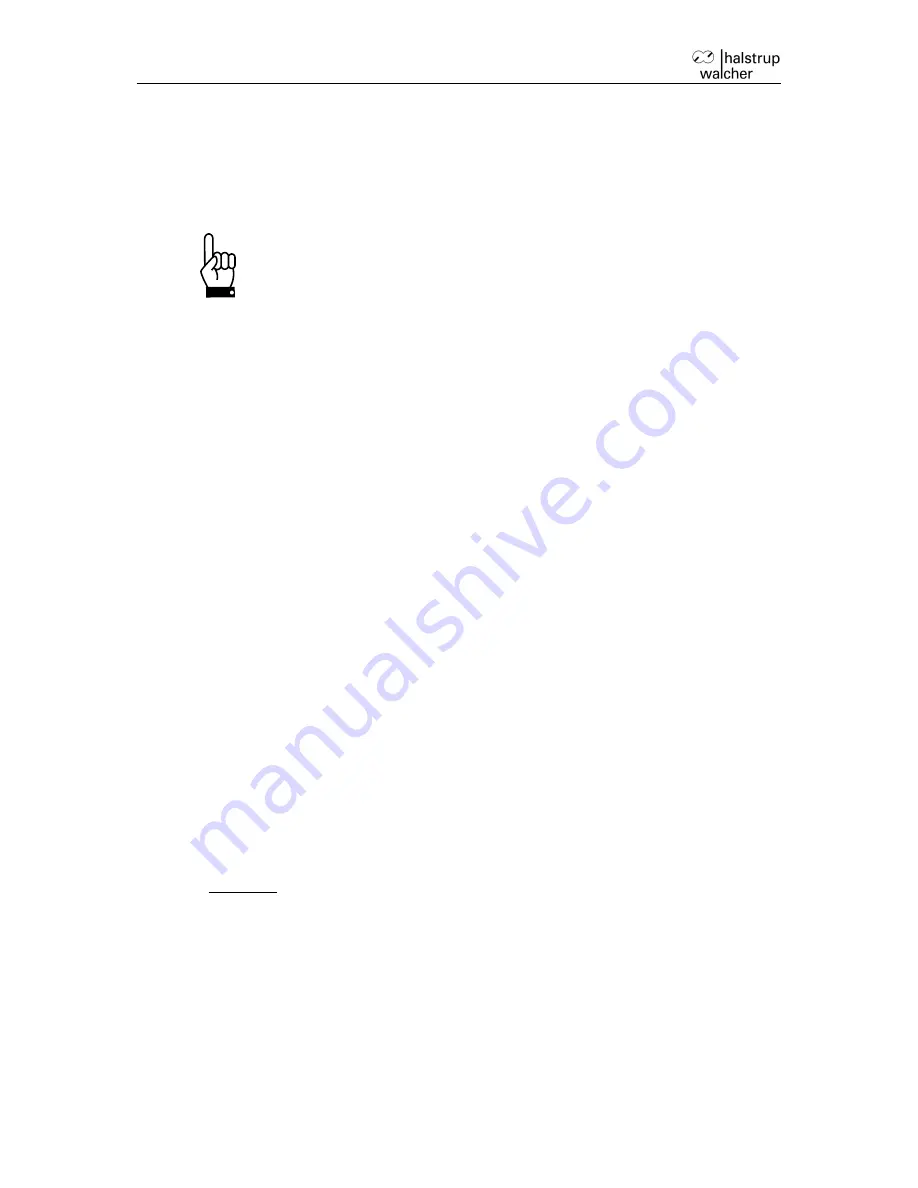
Instruction Manual PSx3xxPN
28
Once the target position has been reached, the device compares it to the internal
absolute encoder status. If a discrepancy is detected, the device then sets the “error”
bit (bit 9 in the status word).
In delivery state the length of loop is < 0, i.e. each target position is approached in
forward direction.
It is not possible to perform a positioning run to the upper limit (Par. 42)
with a length of loop > 0 because the drive would have to run past the
upper limit in order to do so. The same applies to the lower limit (Par. 43)
with a length of loop < 0.
3.5
Positioning sequence without loop
The mode “positioning without loop” mode is used primarily for moving the small
distances involved in fine adjustments. In this case, each position is approached
directly. This does NOT eliminate any play present in the spindle in question. The
PSx3xxPN internal gear backlash does not play a role in this case, as position data
are acquired directly at the output shaft.
3.6
Calculating the absolute physical position
The PSx3xxPN actuator includes an absolute measuring system with measurement
range of 256 rotations. In order to avoid an overflow when the drive is switched off
and moved by an external force, the user can only command positionings in the range
of 250 rotations. Thus the upper as well as the lower 3 rotations of the measurement
range are inaccessible.
The mapping of the desired positioning range to the physical positioning range is
done with the help of the parameter “upper mapping end” (Par. 41).
In the delivery state, the drive is at position 51200, the upper limit switch is set to
101200 and the lower limit switch is set to 1200, yielding a positioning range of ±125
rotations (±50000 increments). So if the desired positioning range doesn’t exceed
±125 rotations, in delivery state none of the following actions to adjust the positioning
range have to be taken.
For the realization of any desired positioning range independent of the possible
positioning range which is defined by the mounting situation (physical positioning
range) there are the following two possibilities:
1) Move the axle (for example a spindle) to the desired position, then move the drive
(with opened collar) to the position value which belongs to the physical position of
the axle, only then close the collar.
Examples:
a) Move the axle in middle position, then move the drive at no-load (with opened
collar) also to middle position (position 51200), then close the collar. The drive
is now capable of moving 125 rotations (±50000 increments by default) in each
direction.
b) Move the axle completely to the left (resp. bottom), then move the drive at no-
load (with opened collar) without loop to the lowest position (position 1200),
then close the collar. The drive is now capable of moving 250 rotations (100000
increments by default) to the right (resp. top).
c) Move the axle completely to the right (resp. top), then move the drive at no-load
(with opened collar) to the highest position (position 101200), then close the
collar. The drive is now capable of moving 250 rotations (100000 increments by
default) to the left (resp. bottom).
Содержание PS*3**EIP series
Страница 35: ...Instruction Manual PSx3xxPN 35 ...