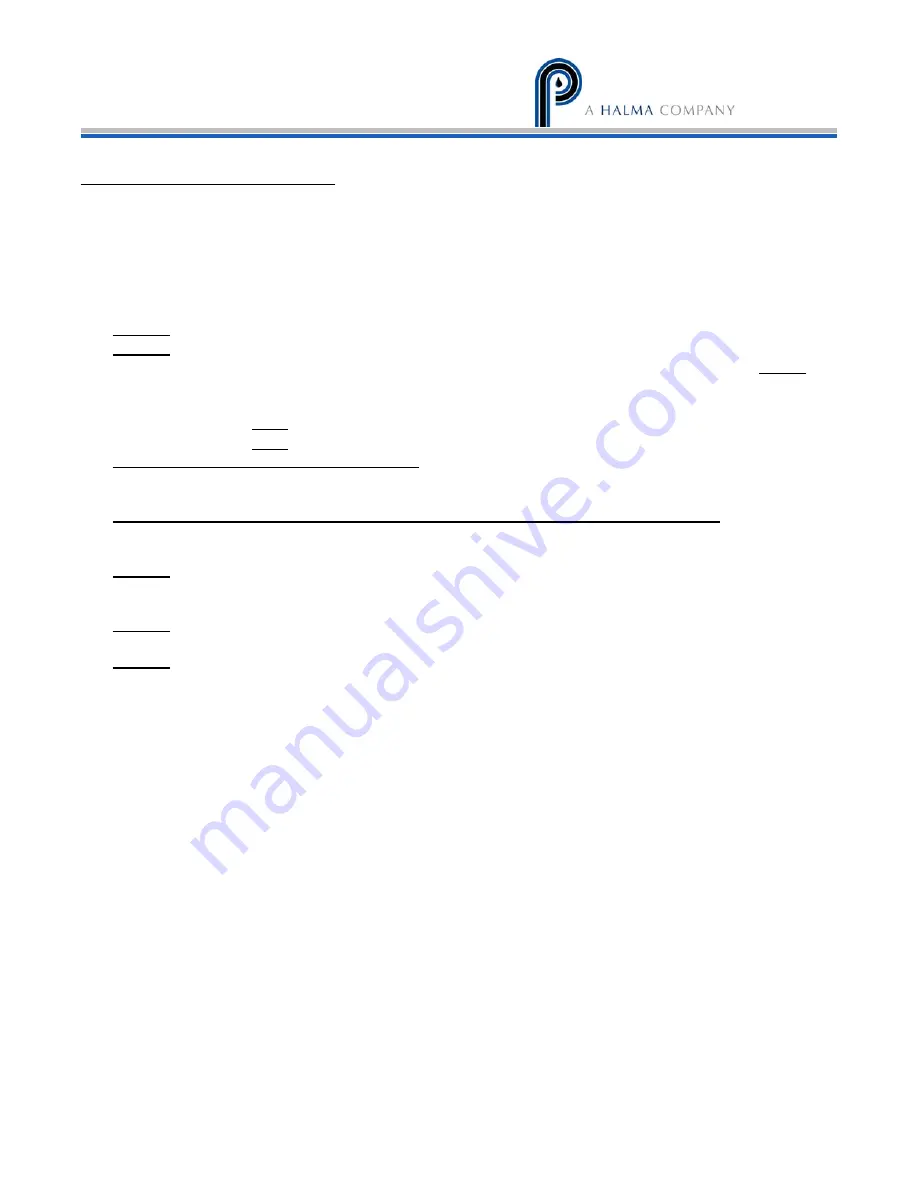
PERMA PURE LLC
Model 3300 User’s Manual
Doc. #532: Revision: 000
Page 6 of 14
Important Safety Warnings
Please be sure to review the following basic safety procedures. These procedures
represent the MINIMUM requirements to operate the equipment safely. It is the ultimate
responsibility of the operator to ensure proper safety practices are utilized at the point
of operation.
•
NEVER
attempt to operate this equipment in an explosive or otherwise hazardous area.
•
NEVER
exceed any specified rating for the equipment. Voltage, temperature and pressure
ratings must be closely observed and not exceeded. Voltage rating of the equipment
MUST
match the rating on the data label. Please make sure that it matches before powering up the
equipment.
•
This equipment is
NOT
designed to be used in an explosive environment.
•
This equipment is
NOT
designed to operate in a wet environment.
•
Sample gas is potentially dangerous
. A leak test is recommended at initial startup and as
often as necessary to maintain a safe working environment around the equipment. The gas
stream exhaust must exit away from all personnel to prevent dangerous exposure.
•
NEVER operate the equipment with any part of the enclosure unsecured
. All operated
doors and covers must be in place and secured prior to operation. Electrical current may be
present behind covers or doors, even if tools are not necessary to access these components.
•
NEVER
attempt service on this equipment without first disconnecting all energy sources.
Repair of this equipment should only be done by properly trained personnel that are familiar
with the potential risks involved with servicing of the equipment.
•
NEVER
replace fuses with types other then the sample specification of type and current. Do
not bypass this or any other safety device.
•
NEVER
operate this equipment if it is visibly damaged or the possibility exists that it may have
been damaged.
•
The use of components that have not been purchased through an authorized Perma Pure
dealer or directly from Perma Pure may compromise the safety of the operator. Additionally,
use of non-authorized components may change the operating characteristics of this equipment.
Any changes to the equipment, that modify its operation in any way, are dangerous, and are
strictly prohibited.
•
Read the entire operating manual before attempting to set up or operate the equipment.
•
Please heed all warning labels that are on the equipment. They are there to remind you of
possible hazardous conditions.
•
Verify the integrity of any mechanical and/or electrical connections that are made to the unit.
Verify that the unit is connected to the proper rated power for the system
Verify that the unit is plumbed properly to operate effectively