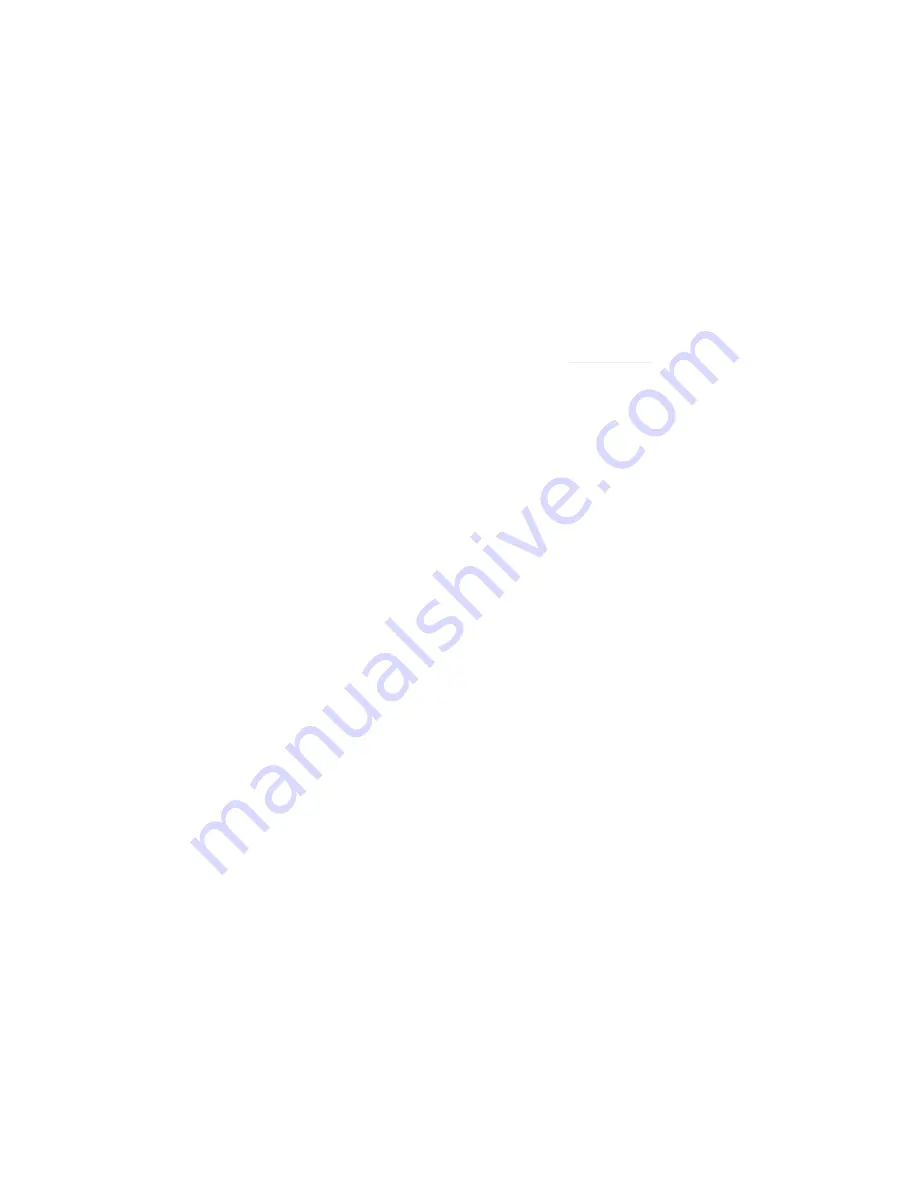
14
Control
Troubleshooting Valve Performance with PID Tuning
The following issues can often be resolved by adjusting the PID gain values for your pressure controller.
Fast oscillation around the setpoint
• PD
: Reduce the
P
gain in decrements of 10%.
• PD²I
: Increase the
P
gain in increments of 10%, and then adjust the
I
gain to fine-tune.
Overshot setpoint
• PD
: Reduce the
P
gain in decrements of 10%.
• PD²I
: If
D
is not 0, increase the
P
gain in increments of 10%.
Delayed or unattained setpoint
• PD
: Increase the
P
gain in increments of 10%, and then decrease the
D
gain by small amounts to fine-tune.
• PD²I
: Increase the
P
gain in increments of 10%, and then increase the
I
gain to fine-tune.
✓
Note:
Valve tuning can be complex. More detailed information is available at
.
Using a Control Deadband for Pressure Control
CONTROL
→
Control Loop
→
Control Deadband
The control deadband is designed to minimize the amount of gas exhausted and improve stability. There is no active
control within the deadband setting.
To turn on the control deadband, enter a non-zero value in
CONTROL
→
Control Deadband
→
Deadband
. In order for the
deadband to activate, the controller must reach the setpoint. If the process variable drifts outside a deadband limit, active
control resumes until the setpoint is reached again.
The controller can be set to either hold the current valve position or close the valve(s) in
CONTROL
→
Control Loop
→
Control Deadband
→
When in Band
. It is recommended to close the valves on PCD-Series controllers.
Example:
With a setpoint of 30 PSIA, a deadband of ±0.25 PSIA allows absolute pressure to vary between 29.75 and
30.25 PSIA. The device will increase pressure until it reaches the setpoint of 30 PSIA. With a setting of
Close valve
, it will
close both valves until the pressure reading varies outside of the preset deadband.
Setpoint Ramping
Setpoint ramping regulates how quickly the controller will reach the pressure setpoint. It is often used to prevent bursts
of flow from damaging delicate instruments when starting a process.
To activate setpoint ramping, set a maximum ramp rate and configure when to enable the ramping function.
Setting the Ramp Rate
•
Ramp
is a quick way to change the maximum rate of change.
•
Units
is a quick way to change the engineering units used.
•
Set By Delta / Time
allows for more detailed control of the ramp rate including changing the value of the time period
Ramping Options
Changing ramping options allows you to have a ramp in only one direction, increasing or decreasing. It also allows you
to ignore the ramp rate when initially powering on or commanding a zero setpoint.
•
Ramp
Up
toggles on and off. When off, the ramp rate will not be honored when increasing pressure to reach a given setpoint.
•
Ramp
Down
toggles on and off. When off, the ramp rate will not be honored when decreasing pressure to reach a given setpoint.
•
Power
Up
toggles between
Allow Ramp
and
No Ramp
. If set to
No Ramp
, the device will ignore the ramp rate just after
powering on, otherwise it will honor the ramp rate from a zero setpoint.
•
0 Setpt
determines whether the controller ramps when a zero setpoint has been given. If this setting is set to
No
Ramp
, when given a zero setpoint, the controller will immediately snap to the zero setpoint; otherwise it will ramp at
the selected rate.