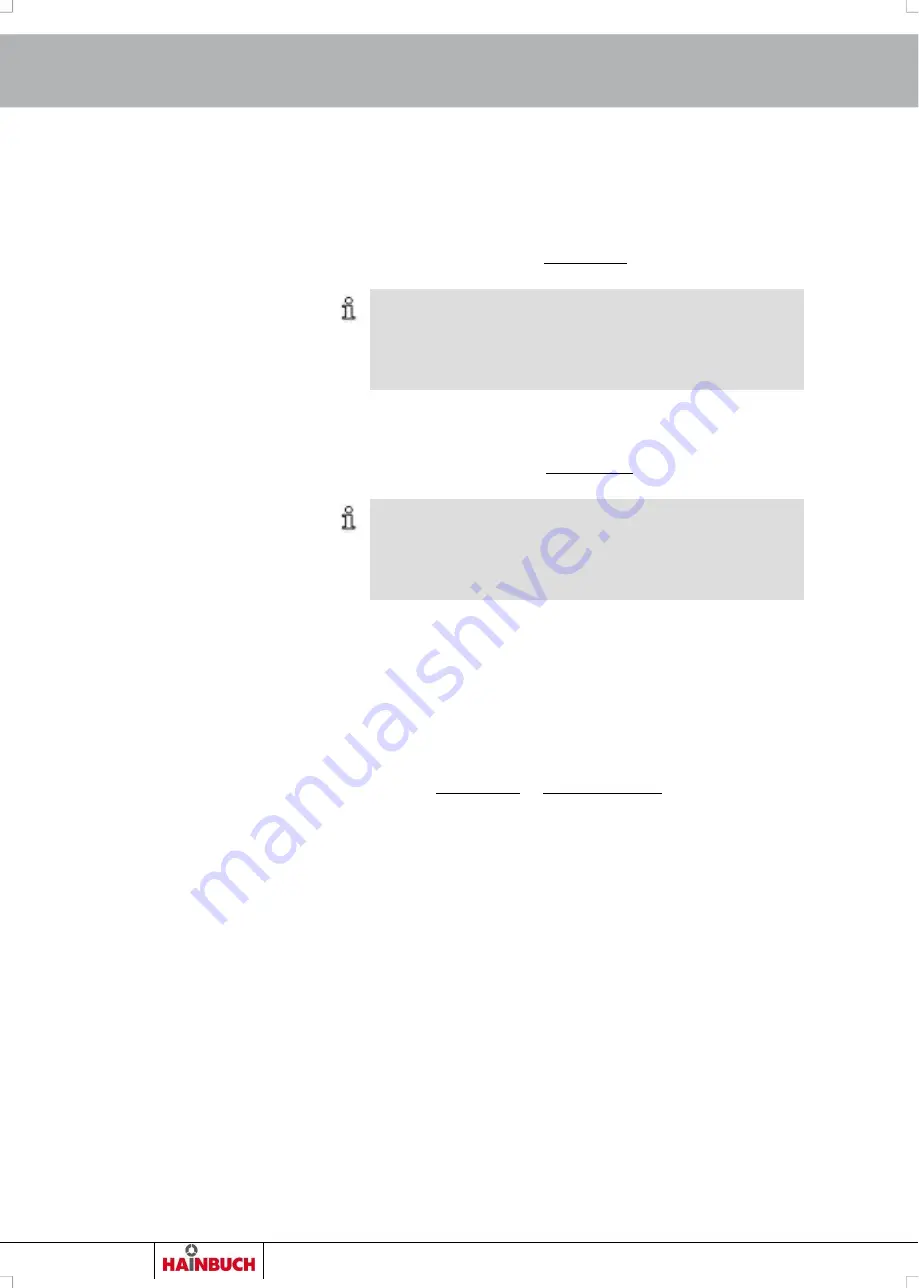
MANOK plus
Technical data
24
Order h49 7144.907-333
3.6.2 Calculation
The following formula should be used to determine the actu-
ating torque that needs to be set to achieve a defined level
of actuating force:
𝑀 =
𝑀
𝑚𝑎𝑥
∗ 𝐹
𝑎𝑥
𝐹
𝑎𝑥 𝑚𝑎𝑥
INFORMATION
The maximum actuating torque
𝑀
𝑚𝑎𝑥
and the maxi-
mum actuating force
𝐹
𝑎𝑥 𝑚𝑎𝑥
can be taken from the
»General information« chapter.
The following formula should be used to determine the actu-
ating force present at a given actuating torque setting:
𝐹
𝑎𝑥
=
𝐹
𝑎𝑥 𝑚𝑎𝑥
∗ 𝑀
𝑀
𝑚𝑎𝑥
INFORMATION
The maximum actuating torque
𝑀
𝑚𝑎𝑥
and the maxi-
mum actuating force
𝐹
𝑎𝑥 𝑚𝑎𝑥
can be taken from the
»General information« chapter.
3.6.3 Sample calculation
Clamping head chuck
MANOK plus size 65
Actuating force
Actuating force to be set
𝐹
𝑎𝑥
= 27𝑘𝑁
Calculation
𝑀 =
𝑀
𝑚𝑎𝑥
∗ 𝐹
𝑎𝑥
𝐹
𝑎𝑥 𝑚𝑎𝑥
=
100𝑁𝑚 ∗ 27𝑘𝑁
45𝑘𝑁
= 60𝑁𝑚
Содержание MANOK
Страница 1: ...Operating instructions incl installation manual MANOK plus EN ...
Страница 91: ...MANOK plus Removal Order hotline 49 7144 907 333 91 6 Remove the product from the machine table ...
Страница 104: ...MANOK plus Annex 104 Order hotline 49 7144 907 333 ...
Страница 105: ...MANOK plus Annex Order hotline 49 7144 907 333 105 ...