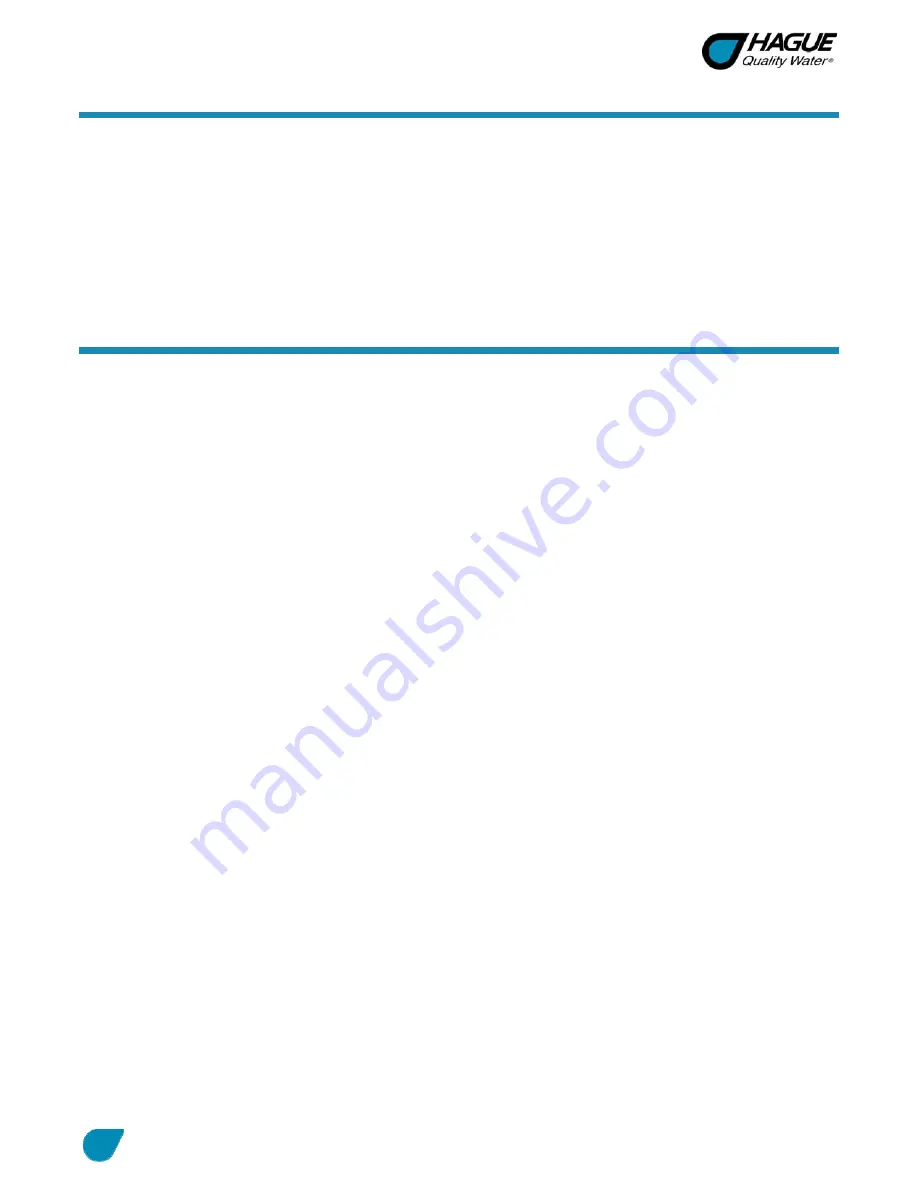
Checklist Before Installation, Cont.
Drain
—Drain the appliance to an appropriate drain, such as a floor drain or washer drain that will comply with
all local and state plumbing codes. To prevent back-siphoning, provide an adequate air gap or a siphon break.
See
Installation Steps and Start-Up Procedures
. For installations under the kitchen sink, be sure to install the
drain line using a dishwash air gap. Call the factory for recommended installation.
Electricity
—The transformer supplied is for a standard 115 volt, 60-cycle AC outlet for locations in North
America or 220 volt, 50-cycle AC outlet for locations outside North America. The transformer supplied for Japan
is 100 volt, 50/60 cycle AC.
If you have any questions, contact your water treatment specialist.
Precautions
Do
1.
Comply with all state and local, building, plumbing, and electrical codes.
2.
Install the appliance before the water heater.
3.
Install the appliance after the pressure tank on well-water installations.
4.
Install a pressure-reducing valve if the inlet pressure exceeds 70 psi (4.8 bar).
5.
Examine the inlet line from the pressure tank to appliance on well water with iron (recommended minimum
inlet pipe size 3/4-inch I.D.). On municipal water, recommended minimum inlet pipe size is 1/2-inch I.D.
6.
Install a gravity drain on the cabinet.
7.
Secure the drain line on the appliance and at the drain outlet. See
Installation Steps and Start-Up
Procedures
.
8.
Allow a minimum of 8 to 10 feet (2.4 to 3.1 meters) of 3/4-inch pipe from the outlet of the appliance to the
inlet of the water heater.
Do Not
1.
Do not install if checklist items are not satisfactory. See
Checklist Before Installation
.
2.
Do not install if the incoming or outlet piping water temperature exceeds 120°F (49°C). See
Water
Conditioner Specifications
.
3.
Do not allow soldering torch heat to be transferred to valve components or plastic parts when using the
optional copper adapters.
4.
Do not overtighten the plastic fittings.
5.
Do not plumb the appliance against a wall that would prohibit access to plumbing. See
Installation Steps
and Start-Up Procedures
.
6.
Do not install the appliance backward. Follow the arrows on the inlet and outlet.
7.
Do not plug the transformer into an outlet that is activated by an On/Off switch.
8.
Do not connect the drain and the overflow (gravity drain) lines together.
9.
Do not use to treat water that is microbiologically unsafe or of unknown quality without adequate
disinfection before or after the appliance.
10.
Do not allow your appliance or drain line to freeze.
HomeGuard
®
Owner’s Manual
9/29/2009
10