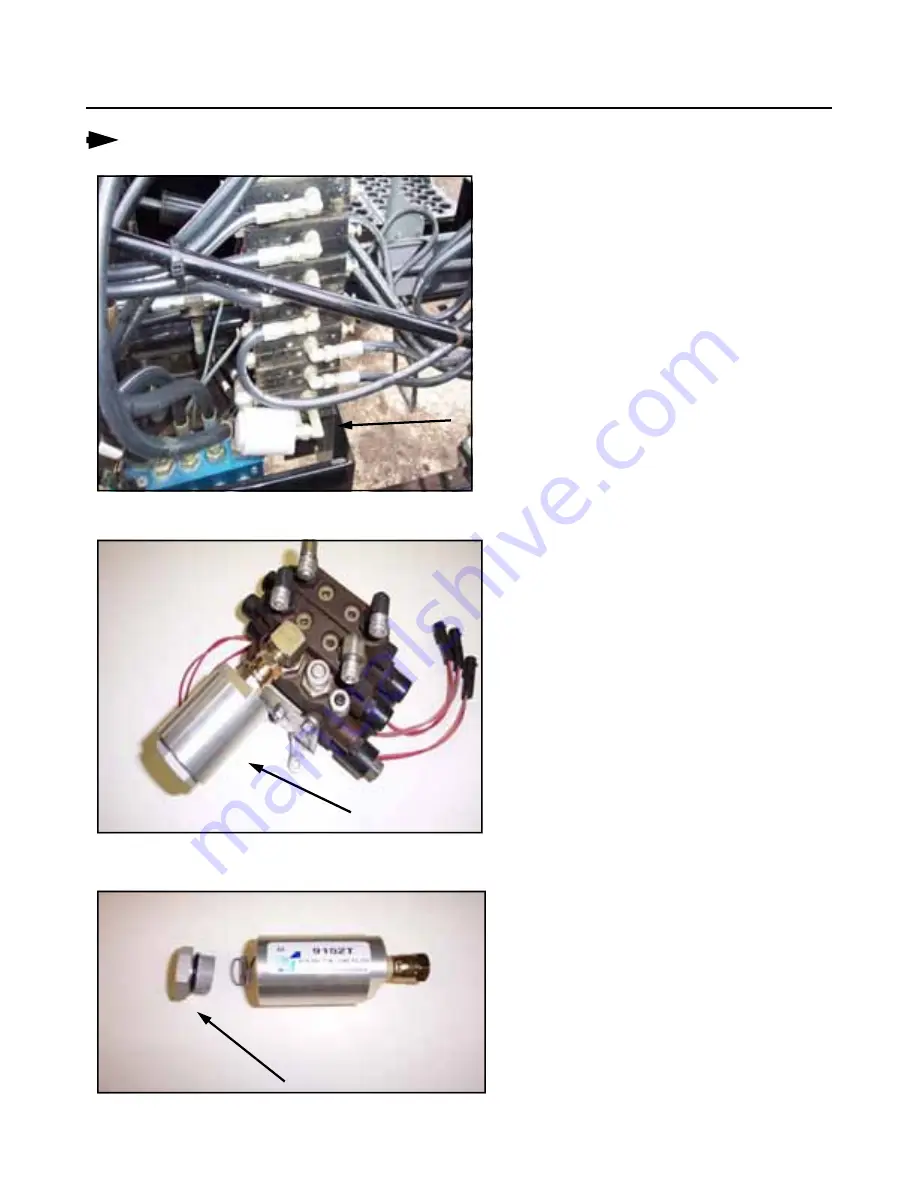
V.
SERVICE AND MAINTENANCE
High Pressure In-line Filters
LIFT ARM STACK VALVE -
The valves
on the lift control stack valve are protected
by a 90 Micron in-line sintered bronze filter
(fig. 5.3). When the filter element is removed
for cleaning, caution should be taken so the
gasket is in the proper place when re-
installing (fig. 5.5). Also, re-install filter
paying attention to direction of flow so the
end marked “OUT” is oriented correctly.
OUTRIGGER FOLD STACK VALVE -
The valves on the outrigger fold stack valve
are protected by a 90 Micron in-line sintered
bronze filter (fig. 5.4). When the filter
element is removed for cleaning, caution
should be taken so the gasket is in the
proper place when re-installing (fig. 5.5).
Also, re-install filter paying attention to
direction of flow so the end marked “OUT” is
oriented correctly.
42
FIG 5.5
FILTERS CONTINUED
FIG 5.4
FIG 5.3
Содержание 2101
Страница 57: ...54 VI TROUBLE SHOOTING TASSELTROL LS SYSTEM ELECTRICAL CONTINUED FIG 6 1 1 2...
Страница 59: ...56 VII LIMITED WARRANTY NOTES...
Страница 61: ...58 NOTES...