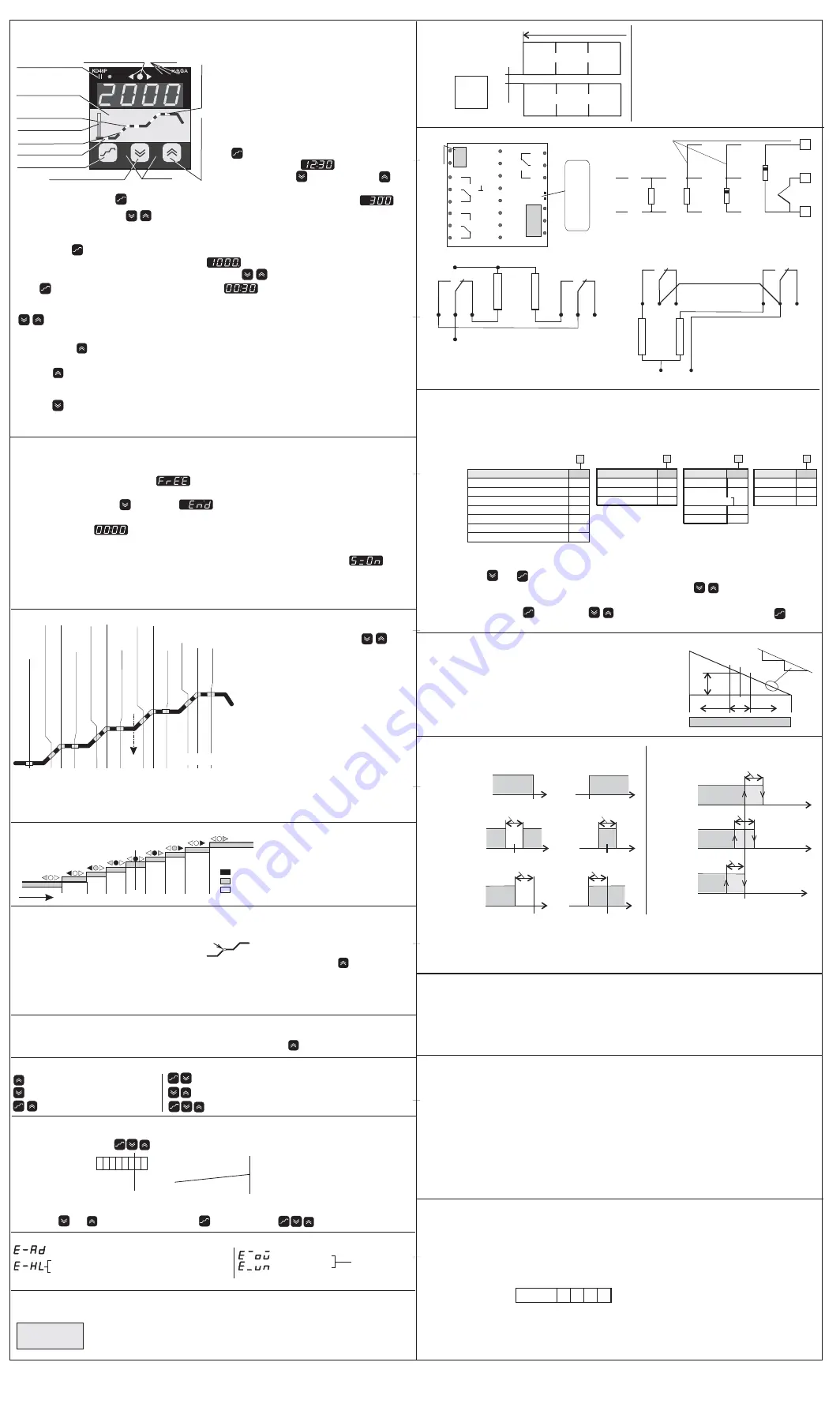
2. page
ME160-5
Warranty
Model:
KD48P
Serial number: Date of purchase:
Validation by the supplier:
The cost of transport (out and home) is borne by the customer.
.
The HAGA Automation LTD’s KD48 series warranted to be free of defects in material, and fabrication. The warranty is valid
for 3 years after delivery to the first purchaser for use. The second period of the warranty is 2 years long in which the
manufacturer repairs the defective controller without fee, except the cost of materials.
.
Since the HAGA Automation LTD can not influence the usage of the controllers, so the warranty is not valid for the
damages cased by them in the connected devices.
.
.
.
.
The HAGA Automation LTD examines in its electrical laboratory the defective controller and detects the cause of breakdown.
The warranty does not apply to damage resulting from transportation, alteration, misuse or abuse.
.
EMC installation guidelines
The KD48P controller generally is not sensible for electrical noise. The controller does not disturb the other instruments in
its environment as well. The extreme circumstances such as long leads, inductances without filters, etc. may reduce the
control qualities. In such cases you ought to prevent the spreading of the electric noise. The noises must be eliminated the
closest to its source. The filters and snubbers at the controller's inputs and outputs generally have not enough effects.
There are some thumb rules for improving the control properties.
.
Connect to the every inductive coil a special filter as close as possible.
Give power from the operating circuit in a cabinet. If there is not, use separating transformer.
In very noisy environment install the controller in metal case which is properly connected to protective earth. If you have
more protective net use the best by trial.
.
In very extreme environment (inductive heating, radio transmitter, X-ray appliances etc.) call an expert.
CAUTION
: In any critical application where failure could cause expensive product loss or endanger personal safety, a
redundant limit controller or monitor is required. We recommend the KD48Bx controller.
.
Never run the signal and control cables together the AC power lines. Use shielded cables and connect the shields (pigtails)
to the PE.
.
All these sensible cables run as far the noise sources as possible.
and
For automatic lead compensation
Cascade control
KD48P PID Profile Controller. User’s Manual.
The KD48P type profile controller can solve all of your
heating tasks, where the temperature must be
controlled precisely by the time.
.
Due to the robust PID algorithm the KD48P controls
the temperature along the programmed profile with
minimal oscillation.
.
Please configure the controller before starting up. It is
necessary to read up this manual. Some skill in
knowledge of control may be useful.
.
Danger warnings
Programming
It is very easy programming a profile by the graph.
Press
the delayed START green lamp blinks and
the time appears in form
on the display.
You can decrease with
or inrease with
the delay.
Save the value pressing the
again. The lamp of the 1. RAMP (heating velocity) will blink in form
.
After pressing
the controller saves the previous value and steps to the SOAK temperature setting.
The green lamp blinks and value displayed in form
.
Set the SOAK temperature with
.
Caution!
The point at the and is the
signal of SOAK temperature.
Press
and repeat the setting process for the SOAK time
.
The time units of START delay, RAMP and SOAK are in hour or in minute according to configuration 1.p/dPrG[6].
Continue the programming to the and of the profile in the same way. The graph shows you what to do.
keys decrease or increase the displayed value with one unit at a press, but will run down or up
accelerated for holding them down. After the last program step the controller exits from programming.
.
Press and hold
for 5 seconds to start the control. The display changes from OFF to On. The controller
runs the programmed profile to the
command or to the profile end. You can stop the program pressing
End
and hold
for 5 seconds. The lamps light red and the actual blinks. So the graph demonstrates the state
of process.
.
The
Difference display
shows the control deviation. You can inquire about the actual time or temperature
pressing
.
The lamp from among which is set blinks green. The actual running program step lamp is red and blinks.
The lamps of executed steps are continuously red. The lamp which is set in
state blinks red-green.
On
.
For making the handling clear we name the profile construction
and the set of the properties
of controller
. To program a profile go through the graph and write the values in display and save.
Some useful facilities can you find below:
programming
configuring
When you enter a RAMP in the graph
appears. At his command the program jumps across the
velocity segment and heat without any restrictions to the next
temperature.
SOAK
The
temperature limits are configured in 1.p/3.level/
and
.
SOAK
SPlo
SPHi
Step one before
with
there is the
which finishes the profile, turns out the controller.
FrEE
At SOAK time value
the controller jumps to the next RAMP, so it is possible to use two RAMPS
continuously. SOAK time is guaranteed so there is an automatic FrEE before SOAK temperature. This may
disabled by
1.p/3.level/con[6]=1.
The SOAK time may be timeless if 1.p/3.level/dLin[4]=1. The display shows in such a case
.
The programming may be enabled or disabled by the 1.p/3.level/out[7] and 1.p/3.level/dPrG[5] in
or
state. In
state the controller acts by the changed value immediately..
On
OFF
On
All of the ALARM (4 pc) can work as event in each program segment. Configure the properties in the places:
the properties first in 1p./3.level/A*d and A23L, the values after it in 1.p/1.level/A* and A*h.
Using the ON-OFF mode the system oscillates, the PV swings around the SP. The PID control mode gives
the efficiency performance. The H-TUNE determines the parameters after starting. Enter the set point
in the place of first soak temperature by this sketch.
Configure 1.p/3.level/out[54]=00. Give a
short circuit on 8 9 terminals for 1-3 seconds. The display shows
holding down
. The controller
makes 3 on-off oscillations around the selected set point and writes the parameters in the 1.p/1.level. After
it returns to the normal mode. The PID parameters can be altered for modifying of control properties.
tunE
.
Operation of H-TUNE function
The auto tune may be started in
or
state. The controller goes
state finishing the tune.
For special tune see foot-note on 1. page.
On
OFF
OFF
.
There is a modulated (intermittent signal on the 2. relay if
)
1.p/A23L[7]=1 and on the 3. relay if A23L[3]=1
when the relay is active. Acknowledge and turn off the signal with pressing
.
There is a buzzer instead of relay by order.
In the controller containing 16 program steps
you may change
by pressing
for 5
seconds. The profil names are:
profiles
and
.
P-- I
P--II
The controller containing 56 program steps you
profile in
may choose a
1.p/1.level/
PrFL.
The Fig.2. shows an annealing program. The
explanations are as follows:
The range of the first part of the program is
effective to the line 7. The next part runs to
the line 13 and the
symbol is lighting. At
the line 11 the controller turns off the process.
+
If two profile is connected 1.p/3.level/dPrG[2]=1
during the running of the second profile the II
symbol is lighting.
.
Take it into account that the profiles may be connected by the 1.p/3.level/dPrG[012]=
configuration. Write
the connected programs by itself in OFF state. The editing of connected programs in On state are disable.
***
Cation!
If there is a START delay before a connected program than it appears before each profile, but it
will be effective after the start only.
.
START
START
START
Set the RAMP value with the
keys. The value for programmed cooling is negative.
The
upper point in the RAMP value is not a decimal point but shows the difference between the RAMP and
SOAK values.
Caution!
START
START
START
START
START
MAINS
All the necessary fasteners and
connectors are in the accessory bag
Fig. 4
1
2
3
4
5
6
7
8
31
32
33
34
35
36
37
38
21
22
23
24
25
26
27
28
MODE
INPUT
+
-
24Vdc
Tx
A
Rx
B
R1
R2
R3
+
-
User
input.
1.p/3.level/out[54]
-2
-6
-10
-15
2
6
10
15
Lights
Blinks
Does not light
Key for
SP difference display
PV-
The deviation display gives fast
information about the state of the
control loop. The control deviation
can be seen by cast a glance at it
.
SP
PV-SP
Programming example
1
2 3
4
5 6
7
8 9 10
12 13
4+
Start
delay:
17:30
RAMP:
4
50
°C/h
RAMP:
5
00
°C/h
RAMP:
6
50
°C/h
RAMP:
End
SOAK
temperaturet:
300
°C
SOAK
temperature:
630
°C
SOAK
temperature:
980
°C
SOAK
time:
00:30
SOAK
time:
00:20
SOAK
time:
00:15
11
Fig. 2.
Fig. 3.
4 +
START
3
2
1
4
5
Relays
Relays
The
program
runs or is set
II
The program runs
on 4+ area (next 4
steps) or is set
SOAK
temperature
Heating velocity
START delay
Steps in graphic
Deacrease value
Increase
value
SOAK
time
Difference display
Fig. 1.
Y
Actuator
Power supply
Voltage: 85-265VAC, 48-400Hz, 120-375VDC
Power: 3 VA
Fuses: for supply: T315mA.
for relays: 3A
Dielectric strength: EN 61010, 2/II
All the inputs and outputs are galvanic isolated
(except Ssd)
n controller: 51xn+6
Installation
Cut out
45+0,3
45+0,3
Placing in a row
30
Placing in a row
(before the controller)
Relais: 3A, 230V, Ac1. Lifetime min.: 100000 cycle
26
27
28
KTY
+
-
PT100
10
W
Thermo
couple
0-20
mA
4-20
mA
0-200
mV
KTY
Wiring of sensors and transmitters which
was set in: 1.p/3.level/ inp [4 210]
*
Wiring
5
6
7
6
7
8
23
3
22 21
5
Closes
Opens
L
N
N
L
KTY
measures the temperature of the cold junction.
Short-circuit on 26-27 turns the cold junction compensation off.
Wiring the valve positioning
motor.
1.p/out:
10.
Closes at mains fall off and OFF state
******
1. type
Opens
Closes
Wiring the valve positioning
motor
1.p/out:
11.
It remains in actual position
at mains fall off,
closes in OFF state
******
2. type
4
Types of ALARMs
ALARM value
ALARM value
ALARM value
ALARM value
ALARM value
ALARM value
SP
SP
SP
SP
DEVIATION
BAND
PROCESS
NORMAL ALARM
REVERSE ALARM
Relay active
Relay inactive
Relay active
Relay inactive
Relay active
Relay inactive
Hysteresis
Relay active
Relay active
Relay active
Relay inactive
Relay inactive
Relay inactive
Hysteresis
Hysteresis
Hysteresis
SP
Lower
asymmetrical
Symmetrical
Upper
asymmetrical
The ALARMs are a logical functions which act the relays. In the 1.p/3.level/A*d defined properties
determine the value of this function in the process. If the result is 0 the relay inactive (default state).
If it is 1 than active (reverse to the default).
The relay is open in the case of reverse
configuration in active state. Some bool functions are in 1.p/3.level/A23L. These functions can connect
ALARMs together e.g.: in case of A23L[210]=100 R3 is active if AL3
AL4 are active.
Caution!
and
.
When the heat source is far from the workpiece, the controller can not regulate it properly. The controlI
is slow and unstable. Such process is the heating in a retort. Because of the big delay time a fair-sized
temperature overshot may occur.
To eliminate the the waste in material and energy, use 2 controllers in one cascade group. The inside
controller will be the MASTER and the outside the SLAVE.
The HAGA controllers are able to control in cascade method. You can configure the MASTER and connect
to the SLAVE thorough the communication port.
.
.
.
.
.
.
Enter into the configuration and how to do it
Configuring
The configuration specifies the properties of the controller. The configuration pages accept the data by
the model identification only. There is a map on the 1. page containing all of the menu items and the
moving
possibilities among them. There are a lot of security items in the menu. The adequate
configuration helps you to select a very good operation. Using the security code to the necessary grade
the handling will be very easy. So the operator can not enter false data into the process.
.
Press and hold
and
after it for about 3 seconds. The blinking
appears. This is the first level of
configuration (see map on 1.page). Browse about the menu items with
. At menu item
you
can go on the second level and at menu item
on the third level.
SP
Pid-
CnF-
.
Enter the menu item with
and set it with
. Each set goes in the memory by pressing
again.
The memory stores the data for an indefinite period.
0%
Y(SP)
SP
dZon
Yt
Yd’
Yd’
Open
Close
100%
Yt
valve update time, the period of one full opening from
closed state with Y=100 % actuation
Y(SP)
Y at the stable range
dZon
dead zone.
Yd’
is the smallest changing of Y, which can turn the motor.
Below this value the controller does not move the motor.
Valve positioning data
START
START
Start and stop program (5 s)
Inquire for output (Y) in %
Changing
and
program (5 s)
P-- I
P--II
Value of program step while
state
On
Special actuations with keys
Enter to security code (30 s)
Enter into configuration (3 s)
The time written in
brackets are periods
of pressing Start
pressing from right.
.
Accept (ENTER)
Setting:
Exit:
Security
The protect function is for preventing unwanted modification of settings. The protected levels are hidden
by a 6 bit code. Press the
keys for 30 seconds. An EDS appears on the display with the
following actions:
Protect code
e.g.: 001011
Security
levels
00 without protection
01 3. level is hidden
10 2.
11
everything
level is hidden
is hidden
Please memorise the protect code. You can not change the security levels without the protect code!
The service can erase it, if you have forgotten the code.
START
Error messages.
A/D converter error. Service can repair it.
.
Setting error SPLo
SPHi
≤
in state out [6]=1, if SPLo-5%
PV
SPHi+5%
≥
≥
Overflow
Underflow
The error message disappears after a reset, if the fault was repaired..
Outside
PV
range
Repairing
When the self test after the start repeats continuously the controller has
got out of order. The controller may be repaired by the manufacturer.
_
_
_
_
ALARM3
code
Relay
0
1
None
2
3
4
5
6
Current output 0/4-20 mA
Voltage output 0/1-5 V
Voltage output 0/2-10 V
Buzzer
OPC
KD48P
Model identification
The controller is made of separate parts.
So you can extend it later.
Code
1
2
0
4 steps
56 steps
16 steps
Program
Communication Code
RS-232
0
1
None
2
RS-485
Other
Code
0
1
None
Voltage
for transmitter
2
3
ALARM 4,5
Both
U
T