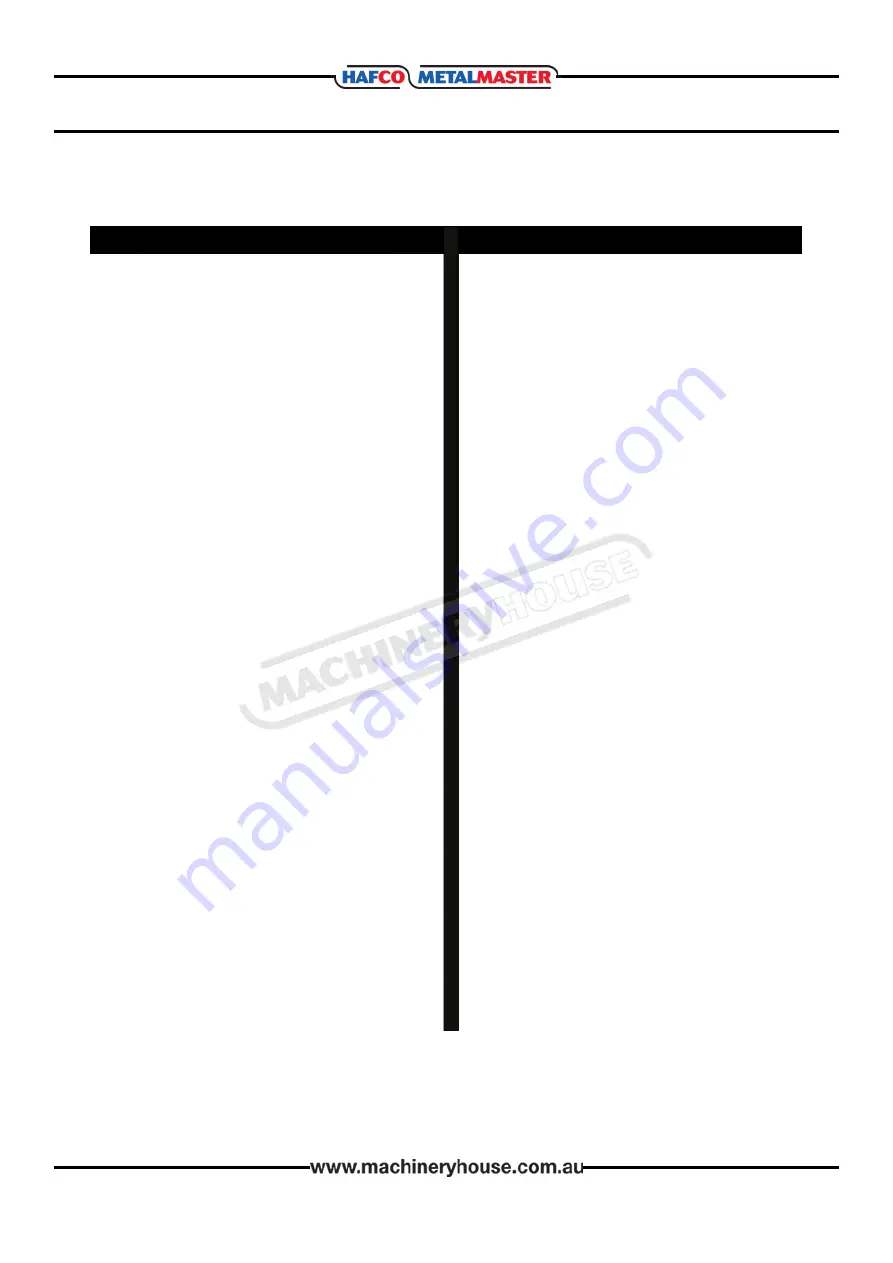
24
OPERATION MANUAL
BS-152 PARTS LIST
ITEM
DESCRIPTION
QTY.
ITEM
DESCRIPTION
QTY.
1
2
3
4
5
6
7
8
9
10
11
12
13
14
15
16
17
18
19
20
21
22
23
24
25
26
27
28
29
30
31
32
33
34
35
36
37
CUP HEAD SCREW M4X6
LEFT COVER
WORK TABLE
FIXATION BOARD OF WORK TABLE
FLAT ASHER Φ8
HEX COUNTERSUNK SCREW M8X10
HEX COUNTERSUNK SCREW M8X16
U-SUPPORT
BODY
DUST RECEIVER
DRIVEN WHEEL
STAR GRIP SCREW
SPRING
FLAT WASHERΦ8
FLAT FASTNER WASHER Φ8
SELF-LOCKING NUT M8
NUT M8
DRIVEN WHEEL GUIDE
COLUMNAR PINΦ6X50
BOLT M8X25
SHAFT BLOCK
HAND WHEEL
HEX SOCKET HD SCREW M6X30
SPRING
RETAINING RING Φ47
BEARING 204
DRIVEN WHEEL SHAFT
FLAT WASHER Φ8
BOLT M8X25
CUP HEAD SCREW M4X10
FLAT WASHER Φ4
PERSPEX PLATE
COLLECTING BOARD
CUP HEAD SCREW M6X50
FLAT WASHER Φ6
BOLT M8X12
FENCE EXTENSIONS
8
1
1
1
1
2
4
1
1
1
1
3
2
2
6
2
2
1
1
4
1
1
1
1
2
2
1
5
2
2
2
1
2
1
2
2
1
38
39
40
41
42
43
44
45
46
47
48
49
50
51
52
53
54
55
56
57
58
59
60
61
62
63
64
65
66
67
68
69
70
71
72
73
SELF-LOCKINGNUTM6
NUT M4
MOTOR
BOLT M8X25
HAND BALL
SAFETY COVER
TOP TABLE
RIGHT COVER
SIDE FENCE
PROPECT TUBE
PIN 3X20
SPRING
HAND BAR
BASE
WASHER
LOCK KNOB
LOCK SHAFT
SCREW 6X16
HEX HEAD SCREW M5X20
SAND BELT
BIG WASHER Φ32
DRIVE WHEEL
CUP HEAD SCREW M8X20
ELASTIC WASHER Φ8
BOLT M8X12
HAND BAR CONNECTING BLOCK
HANDLE
BLACK COVER PLATE
HINGE
CUP HEAD SCREW M4X6
SPRING PLATE
SWITCH
NUT M4
WASHERΦ4
ELASTIC WASHER Φ4
SCREW
2
2
1
4
1
1
1
1
1
1
1
1
1
1
1
1
1
1
1
1
1
2
2
2
1
1
1
4
16
1
1
4
4
4
4
Содержание BS-152
Страница 20: ...20 OPERATION MANUAL WIRING DIAGAM FOR BS 76 BS 152 ...
Страница 21: ...21 OPERATION MANUAL BS 76 PARTS DIAGRAM ...
Страница 23: ...23 OPERATION MANUAL BS 152 PARTS DIAGRAM ...