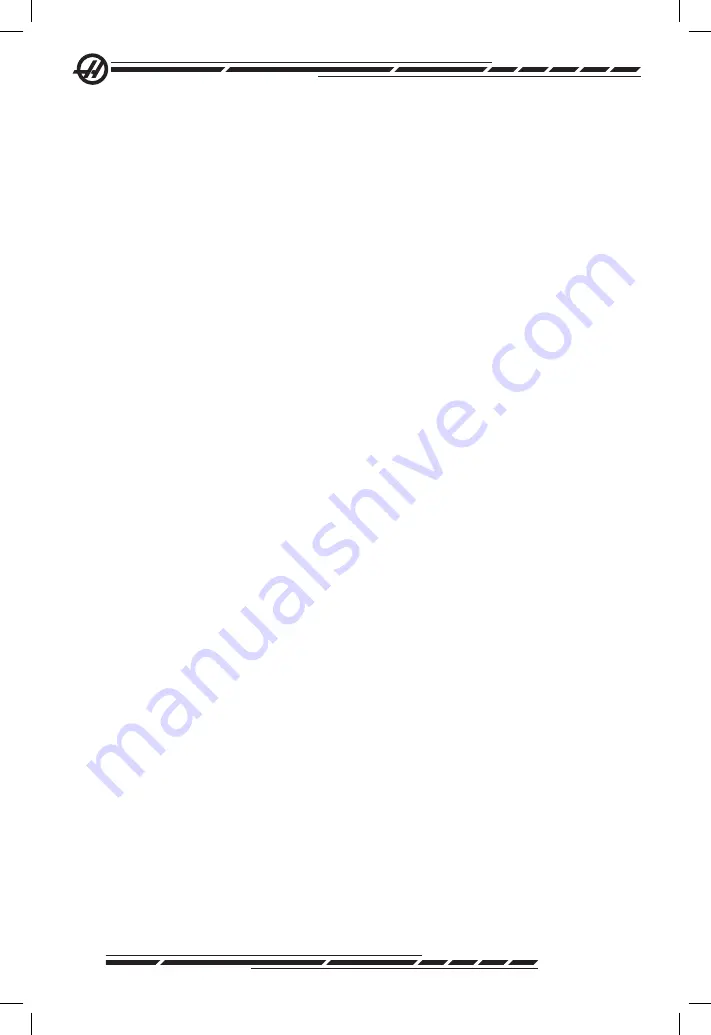
6
96-0041 Rev V
March 2012
Machine Productivity
Use the load meter as an indicator of how the machine is cutting. Speeds and
feeds should be adjusted after the initial cut. The initial cut will give an instant
read-out of the performance of the machine. If adjustment are necessary, they
should be made in 10% increments. Pay close attention to:
• Chip formation and color
• Chip load
• Monitor part and ixture during the cut
• Listen for any unusual noises
Surface Finish
A good inish depends on a number of variables. The following are a number of
items to check to achieve a good inish:
• Good inish results in slower feeds and higher speeds
• Face milling produces the best inish
• Increasing the number of cutters (inserts) allow for a better inish
• Cuts should always be in the same direction
• Lighter depth of cuts will produce a better inish
• Coolants use can also affect part inish
Accuracy
Machine accuracy can be affected by a number of variables, such as:
Is the machine properly warmed up?
Holes should be center drilled irst
Check the condition of the tooling
Cutting Tool Descriptions
Drill
Used to create a cylindrical hole in a work piece. Drilled holes can be
“through holes” or “blind holes”. A “blind hole” is not cut entirely through a work
piece.
Center drill
A small drill with a pilot point. It is used to create a small hole with
tapered walls. When a hole’s location must be held to a close tolerance, use a
center drill irst and then use a regular drill to inish the hole. The tapered walls
of the center-drilled hole will keep the regular drill straight when it begins to drill
into the work piece.
Reamer
Designed to remove a small amount of material from a drilled hole.
The reamer can hold very close tolerance on the diameter of a hole, and give a
superior surface inish. The hole
must be
drilled irst, leaving .005 to .015 of an
inch stock on the walls of the hole for the reamer to remove.
Tap
Used to create screw threads inside of a drilled hole. NOTE: Care must
be taken when using a milling machine to perform a tapping operation. For
example, the spindle speed and feed must be synchronized.
End Mill
Shaped similar to a drill, but with a lat bottom (end). It is used primar
-
ily to cut with the side of the tool, to contour the shape of a work piece.
Содержание Toolroom Mill
Страница 1: ...96 0041 Rev V March 2012 2010 Haas Automation Inc Toolroom mill operaTor s addendum ...
Страница 2: ......