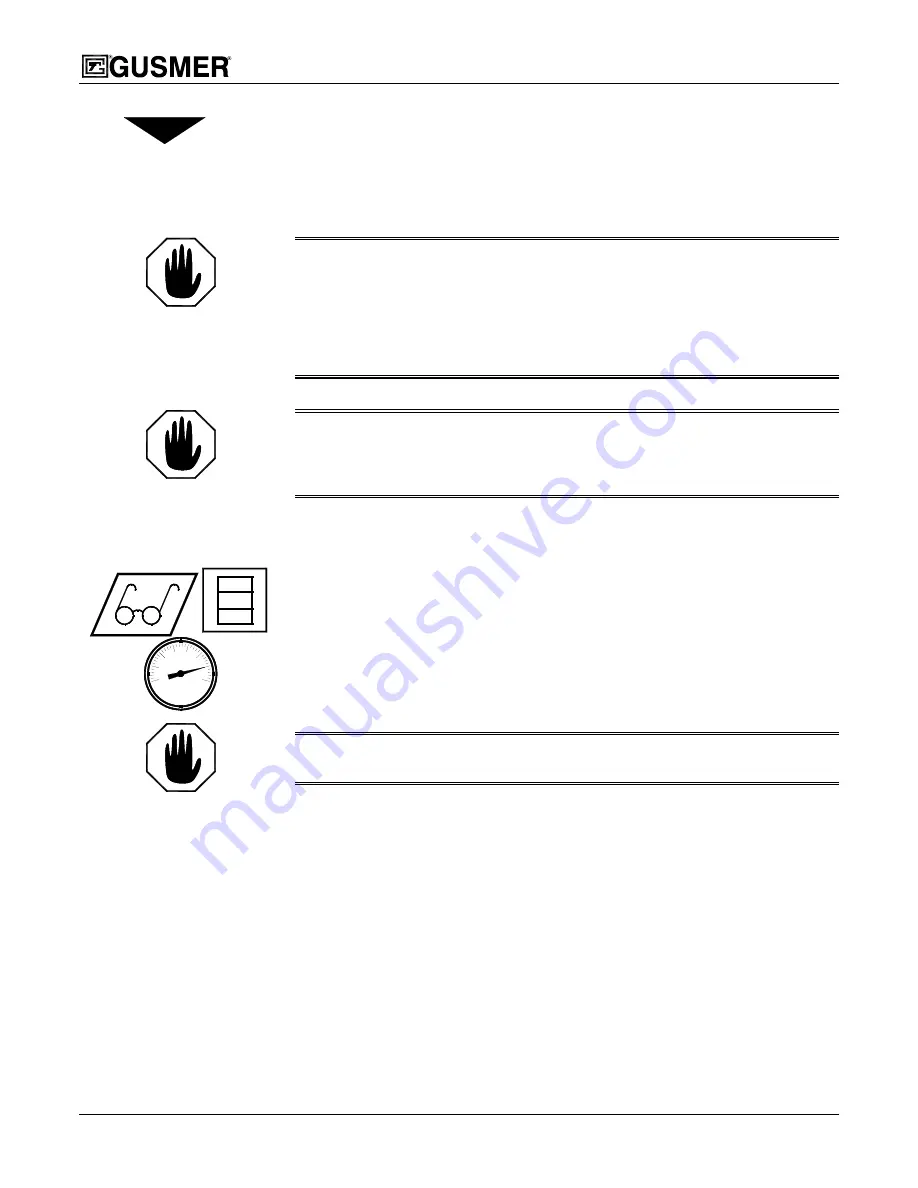
Model FF-2500 Proportioning Unit
34
25942-1, Issue 4
MAINTENANCE
To realize full productivity and maximum service life from the FF-2500, it is necessary
to perform certain maintenance procedures daily or periodically.
WARNING:
T
HE MAINTENANCE SECTION OF THIS MANUAL ASSUMES THAT THE INDIVIDUAL
PERFORMING THE WORK ON THE EQUIPMENT IS QUALIFIED TO DO SO
. T
HIS INDIVIDUAL MUST
HAVE A WORKING KNOWLEDGE OF BASIC ELECTRICITY
,
HYDRAULICS AND PNEUMATICS
;
MUST
FOLLOW ALL GENERALLY ACCEPTED SAFETY PRECAUTIONS USED WHEN WORKING WITH
HYDRAULICS
,
PNEUMATIC AND ELECTRO
-
MECHANICAL EQUIPMENT
;
MUST HAVE READ AND
UNDERSTOOD THE APPLICABLE SECTIONS OF THIS MANUAL
;
AND MUST WEAR PERSONAL
PROTECTION APPROPRIATE TO THE TASK BEING UNDERTAKEN
.
WARNING:
U
NLESS OTHERWISE NOTED
,
ALL MAINTENANCE DESCRIBED IN THIS MANUAL
MUST BE DONE WITH THE INCOMING POWER SWITCHED OFF AND LOCKED OUT AT THE SOURCE
.
A
NY ELECTRICAL TROUBLESHOOTING REQUIRED BEYOND THE SCOPE OF THIS MANUAL MUST BE
DONE BY A QUALIFIED ELECTRICIAN
.
Proportioning Pumps
When the proportioning pumps are functioning properly, it is not unusual for a trace
amount of resin or isocyanate chemical to seep past the pump packing onto the pump
shaft. Maintain proper packing adjustment to minimize seepage. Routinely inspect the
shaft and wipe away any residue when the proportioner is turned off. Disassemble and
clean both proportioning pumps annually. Inspect the pistons and cylinders for mars or
scratches, which may cause leakage or damage to packings. As a preventive
maintenance precaution, Gusmer recommends replacement of the piston and cylinder
packings during the annual cleaning.
(Refer to the Proportioning Pump Assembly section
of the Parts I.D. for reference.)
WARNING:
A
FTER REASSEMBLING OR SERVICING THE PROPORTIONING PUMPS
,
TORQUE THE
CYLINDER TOP HEX NUTS TO
10
FT
/
LBS
.
Pump Bases
Disassemble and clean both pump bases annually as follows:
(Refer to the Pump Base Assembly section of the Parts I.D. for reference.)
1. Perform the Daily Shut-down procedure and bleed all chemical pressures to zero.
2. Remove the valve cover using an adjustable wrench.
Inspect the valve cover o-ring and replace as required. Liberally coat the o-ring with
Lubriplate grease before installing the valve cover back into the pump base. Also,
check the chamfer around the cavity to ensure that there are no sharp edges, which
could damage the o-ring and prevent proper seal.
3. Remove the valve ball and inspect it for nicks and scratches. Replace as required.