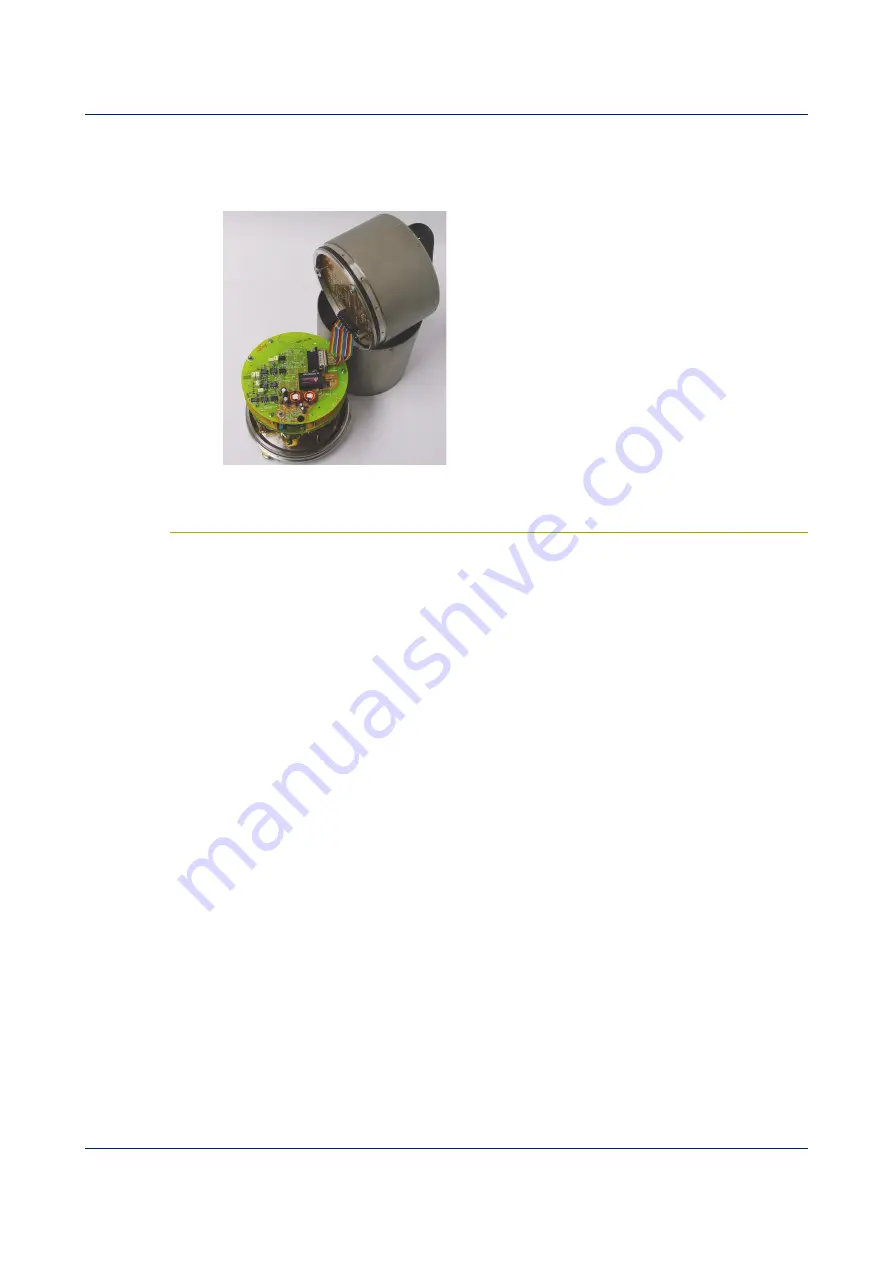
First encounters
2. Carefully lift off the digitiser module, and support it nearby, leaving the ribbon
cable connected. Extension cables can be obtained from Güralp Systems;
otherwise, you can use the casing of the sensor itself as a support.
3. Whilst monitoring the mass position outputs (channels
M8
,
M9
and
MA
), adjust
the potentiometers as above.
3.4.4
Digital nulling operation
The Güralp 40T sensor can be ordered with an option for automated “Digital nulling”.
This removes the need to manually adjust the internal potentiometers to achieve a
near zero mass position output for each component. It comprises a micro-controller
and three digital potentiometers that replace the standard electromechanical pots.
When installing the instrument, ensure that it is levelled accurately by checking that
the bubble in the level lies within the central circle.
On power-up, the micro-controller will automatically zero the mass positions of all
three axes simultaneously. Zeroing can be further triggered via the “centre” control
line on pin U. (On instruments without the digital nulling option, grounding pin U
(to pin Y) puts the instrument into "one-second mode".)
Automatic zeroing takes approximately forty-five seconds to complete, after which
the sensor reverts to long period operation and the nulling module enters a low
power “sleep” mode. During nulling, the sensor's outputs will fluctuate as the pots
are adjusted in a binary search before settling with a mass position of ±0.5V. If the
sensor is poorly levelled, the micro-controller will make three attempts to zero the
mass before giving up and using the closest match.
A test mode is available to check the operation of the digital centring pots. This
mode is entered by holding the centre line low during power up. The unit will then
set the pots to maximum for thirty seconds; then minimum for thirty seconds; then
to the centre position for six minutes. The centre line must be held low
continuously, otherwise the unit will abort the test mode and null the sensors as
normal.
16
Issue F - June 2019