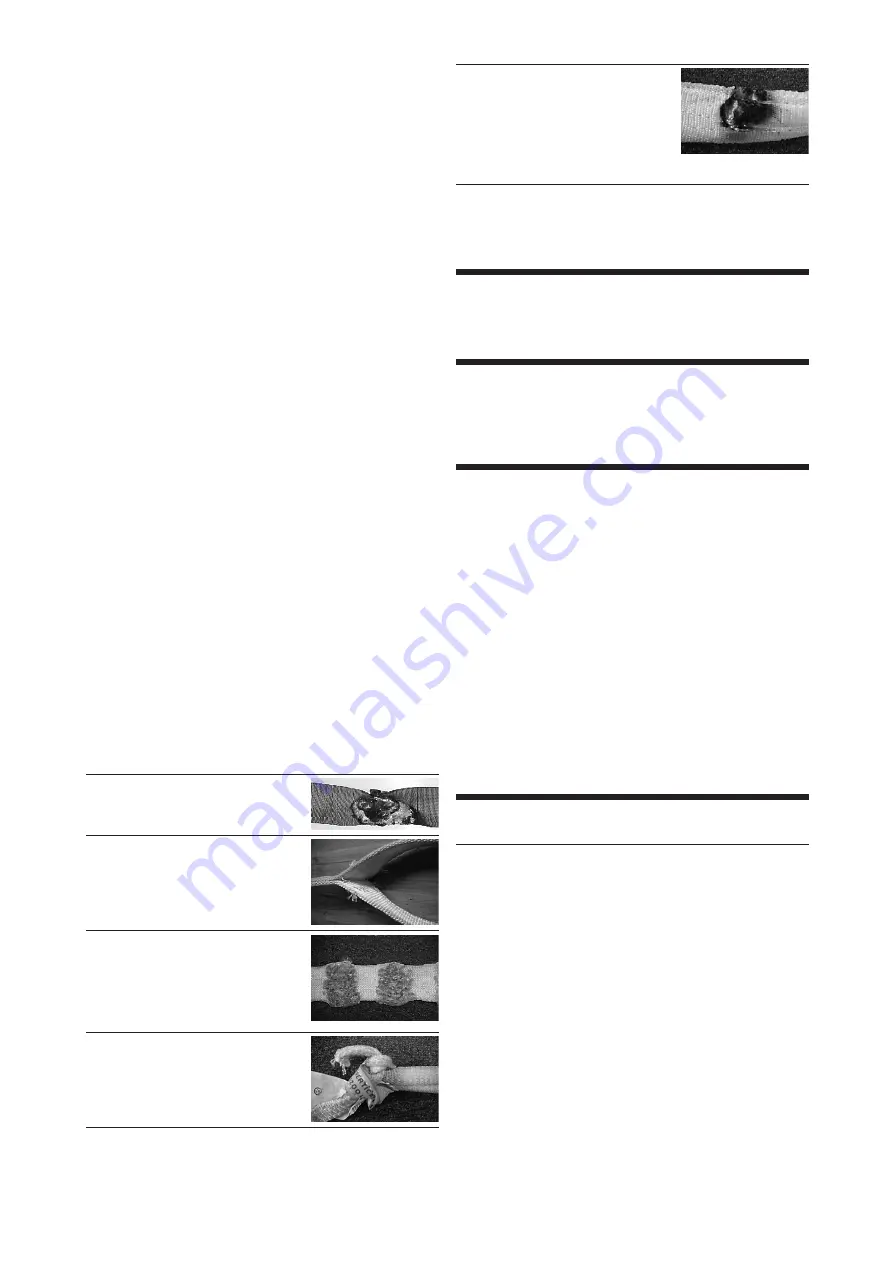
© Guldmann 01/2020 # 900640_1
© Guldmann 01/2020 # 900640_1
7
2) Frequent
The frequent level of inspection should be done by the sling user
before each use. The sling should be examined and removed
from service if damage is detected. The sling user should also
determine that the sling is proper for the user conditions, care task
required and the required weight capacity.
3) Periodic
Your facility might want to consider implementing a program for a
periodic level of inspection at regular intervals. The interval should
be based upon the frequency of use, severity of the service cycle
and information derived through the inspection process. Recom-
mendations to prevent damage and enhance service life could
be made by staff that perform the periodic inspections. If written
inspection records are maintained, they should always reference
the unique sling identification number, and be updated to record
the condition of the sling. Not intended to represent all potential
inspection steps or all potential aspects of product management
program. Judgment of inspector/site prevails.
Sling inspection technique
The sling inspection procedure should be thorough, systematic
and consistent; both visual and “hands on” inspection techniques
are recommended. Certain forms of damage are far more discern-
able through hands-on inspection, than by visual inspection. For
example, fabric stiffness, crushed webbing, as well as, thinning
fabric can be identified through tactile inspection. Visual inspec
-
tion alone may not reveal all forms of sling damage. Once signs
of damage have been identified, do not downgrade the work
load limit of the sling, with the intent of continuing to use it, but at
limited capacity or frequency. This is sometimes done to get more
service life out of a damaged sling. The operating rule and stand-
ard should be: intact = use; damage = do not use.
Consider the practice of documenting sling inspections through
written inspection records. The documentation should include
information such as: the name of manufacturer, the sling stock
number, width and length, the unique sling identification number
(important in differentiating similar slings), as well as the condition
of the sling. Other important information might also include the
date it was received or put into use at your facility and any special
features (if applicable). A beneficial outcome of an inspection pro
-
gram would be the realization of repetitive forms of damage and
the analysis that would lead to specific recommendations.
Sample visual examples of synthetic sling damage
x
)
Chemical/caustic burns
Broken stitching
Crushed / Frayed webbing
Knots
Melting / Charring
x
) sample visual images not intended to
represent all types of potential damage
3 .02 Lifetime
The sling is designed for short-term use by one particular user and
is to be discarded when soiled or no longer needed.
4.00 Technical specifications
Lifting capacity, SWL . . . . . . . . . . . . . . . . . . . . . . .205 kg (450 lbs)
Material . . . . . . . . . . . . . . . . . . . . . . . . . . . . . . . . . . . . . . Polyester
5 .00 EC-Declaration of conformity
The product is manufactured in compliance with the Council
Directive 93/42/EEC of June 14th 1993, including amendments,
as medical device class 1.
6 .00 Environmental policy statement – V . Guldmann A/S
Guldmann is continuously working towards ensuring that the com-
pany’s impact on the environment, locally and globally, is reduced
to a minimum.
It is Guldmann’s goal to:
• Comply with the current environmental legislation (e.g. WEEE
and REACH directives)
• Ensure that we, at the widest possible range, use RoHS com-
pliant materials and components
• Ensure that our products do not have an unnecessary nega-
tive impact on the environment regarding use, recirculation or
disposal
• Ensure that our products contribute to a positive working
environment in the places they are utilised
Inspections are made annually by the Department for Nature and
Environment from the Municipality of Aarhus using the Danish
Environmental Protection Act, section 42 as a reference.
7 .00 Warranty and service conditions
A .
Warranty
Guldmann warrants its equipment is free from material defects
under normal use, and will perform substantially in accordance
with the specifications set forth in documentation provided with the
equipment.
This express warranty shall be in effect for one year from the date
of original purchase and installation (the “Warranty Period”). If a
valid claim is made during the Warranty Period for malfunction or
equipment defect, Guldmann will repair or replace the equipment
at no additional cost to you. Guldmann retains sole discretion as
to whether the equipment will be repaired or replaced.
The warranty does not cover any part of the equipment that has
been subject to damage or abuse by the user or others. The
warranty does not cover any part of the equipment that has been
altered or changed in any way by the user or others. Guldmann
does not warrant that the lifting device functions will meet your
requirements, be uninterrupted or error free.