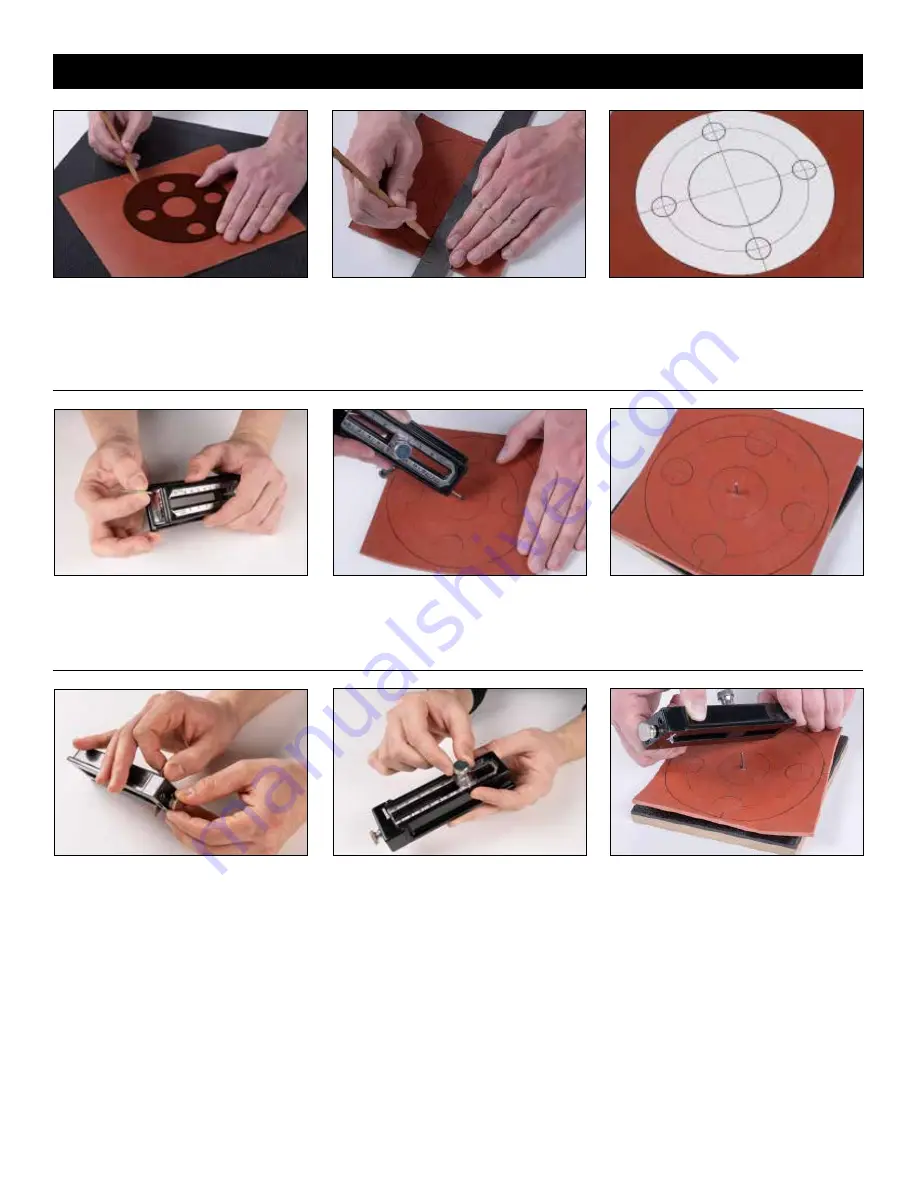
www.allpaxcorp.com
CUT GASKETS UP TO 6” (152 mm) DIAMETER
8.
8.
Loosen top thumb screw. Slide pivot post ind-
cator to desired OD on cutter block scale. Tighten
top thumb screw.
5.
5.
Using cutter block as a handle, pierce center of
gasket material with center pin. Disengage cutter
block leaving center pin protruding through gasket
material.
6.
6.
Insert protruding center pin into recessed
ferrule located in the center of cutting board.
Lay gasket material flat on cutting board.
7.
7.
Loosen cutting blade thumb screw on cutter
block. Position cutting blade to protrude slightly
beyond thickness of gasket material. Tighten
thumb screw.
(continued on next page)
1.
1.
If existing gasket is available, use a pencil to
trace outline onto gasket material.
3.
3.
Another way to determine bolt hole locations
is using a paper template with OD, ID and PCD.
Transfer the bolt hole location center pins with
piercing tool or pencil tip.
4.
4.
Choose center pin approximately ½” (12 mm)
longer than thickness of gasket material. Insert
center pin into silver hole at end of cutting block.
2.
2.
Otherwise, lay out outer diameter (OD), inner
diameter (ID) and pitch circle diameter (PCD)
directly onto gasket material. To determine bolt
hole locations see
LAYING OUT GASKETS WITH
BOLT HOLES.
9.
9.
Position pivot post hole over center pin.
Ensure cutter block is lying flat on gasket material.