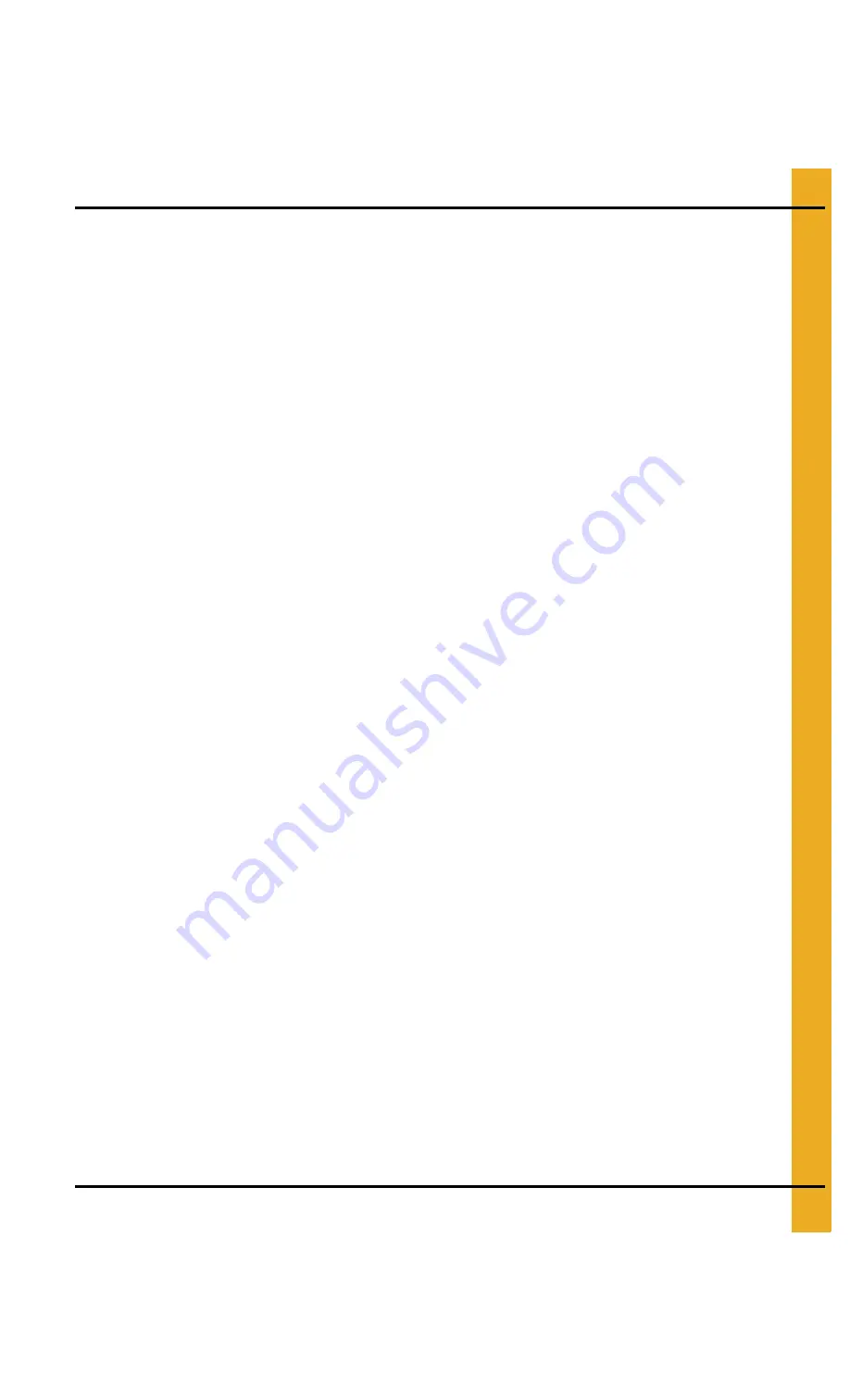
4. Installation
PNEG-2116
Bucket Elevator
19
b.
UP Side Infeed Devices:
The device which feeds the elevator, (auger, belt conveyor, spout,
hopper, etc.), must feed the material into the boot ABOVE the centerline of the pulley. The
buckets must complete the turn around the pulley and be moving vertically upward, not at a
tangent, before encountering material to be elevated. If the buckets ARE NOT moving vertically
upward when they encounter the incoming material, material will be forced back into the infeed
device or chute. Grinding and churning in the boot area will damage the product and excessive
power will be required to operate the system.
c.
DOWN Side Infeed Devices:
Several factors, most importantly the nature of the material being
elevated, are important in determining the location of down side or down-leg infeed devices. If a
change in infeed arrangement from that shown on the certified drawings is contemplated, consult
InterSystems before proceeding with modifications.
d.
FLOW of material to the infeed Devices:
Every effort should be made when designing the
feeding equipment or spouting such that the direction of the flowing material will be perpendicular
to the buckets. Reduce or eliminate any side loading of the buckets. Achieving the bucket
elevators rated capacity is determined by even and consistant bucket fill.
Elevator Discharge
1. Spouting to carry off the material must be sized so that its capacity equals or exceeds the maximum
capacity of the elevator to prevent material plugging in the head or down-legging.
2. The elevator IS NOT designed to support the weight of any accessory equipment. Spouting,
cleaners, distributors, etc. must have their own supporting structures.
Positioning Trunk Sections for Ladder
Study the drawings to determine where each trunk section fits into the overall layout of the elevator leg.
This is important so that platforms and ladders can be attached to the elevator without having to
re-assemble ladder brackets. The final ladder at the head section (at the top of the elevator) must be
near the trunk closest to the discharge (the down-leg trunk).
for ladder and cage
assembly details.
Elevator Belt Selection
If InterSystems has supplied the belt, no further action is required at this time. However, if the belt is being
obtained independent of the elevator, those ordering the belt must be aware of a number of requirements.
1. Belt length must take into consideration the method of belt splicing to be employed in this installation.
Refer to belt splicing
for an overview of the three (3) splicing
methods commonly employed in elevator installations. A mechanical splice requires the least extra
belt while a butt splice requires the greatest length of extra belt.
2. The pattern, spacing, and size of prepunched holes must be correct for the number, type, and size
of the buckets to be attached to the belt. If the belt is purchased with the wrong hole pattern, it will
be extremely difficult and expensive to correct the problem in the field. If the hole sizes are too small,
they may have to be re-drilled in the field. If the holes are too large, the buckets may have to be
re-drilled to accept larger bolts or be replaced. Elevator bolts must fit snugly in the belt.
3. The installer should fabricate spreader bars in advance to avoid delay once belt installation begins.
4. A belt manufacturer or a local belt supplier sales representative can assist in the correct selection
and specification of belting and advise in proper installation procedures.