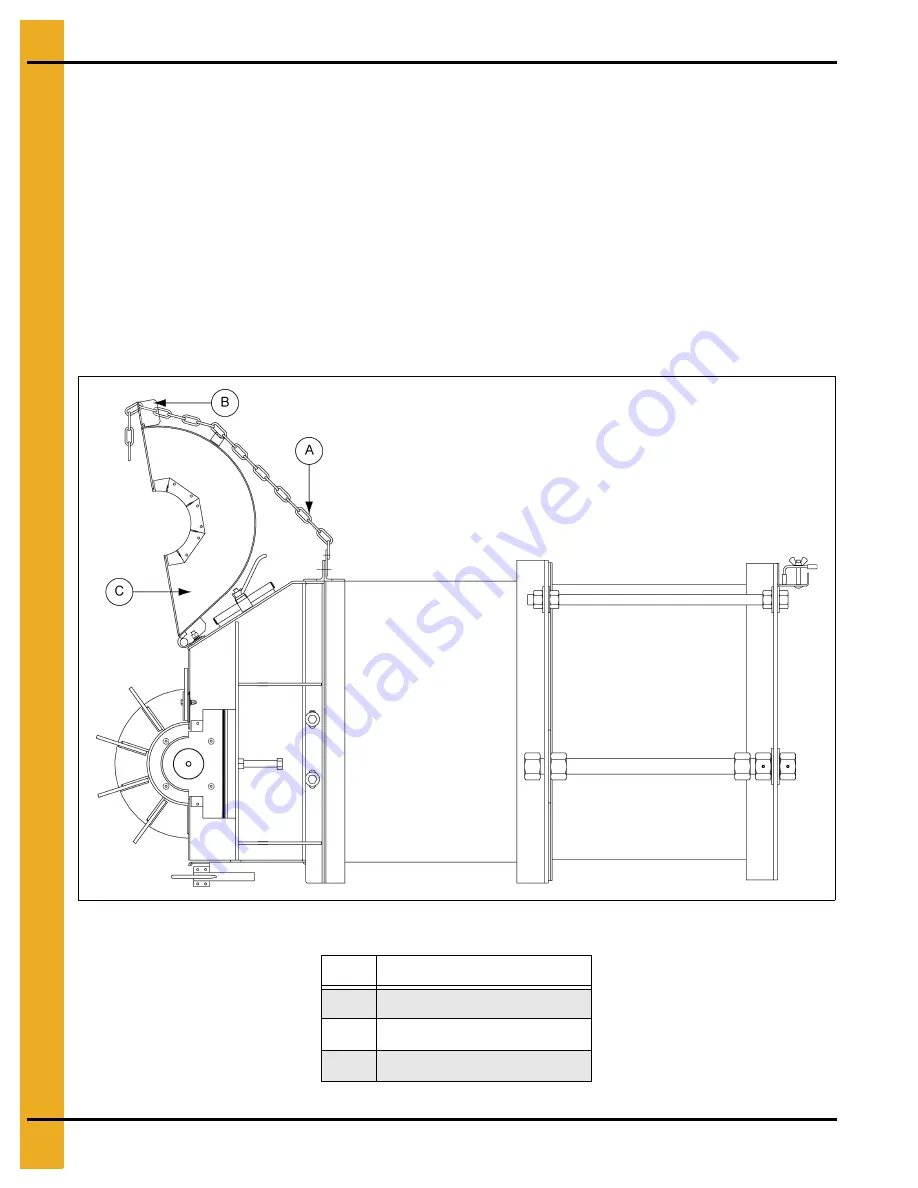
46
PNEG-1204
Enclosed Belt Conveyor
9. Start-Up
Starting Conveyor
1. Check for and remove any tools or debris that may have been left in the conveyor during installation.
2. Tighten the take-up rods on the tail section equally. The belt should be tightened sufficiently to
prevent slippage between the drive pulley and belt and to conform to the crown on the crowned
head pulley.
3. Install covers after belt has been trained.
Secure Shroud During Maintenance
NOTE:
While accessing the tail pulley, the tail shroud may either be removed or pivoted in an upright
position. If pivoted upright, then secure the shroud by placing the chain in the slot as shown
Figure 9A
Ref #
Description
A
Chain
B
Slot
C
Shroud