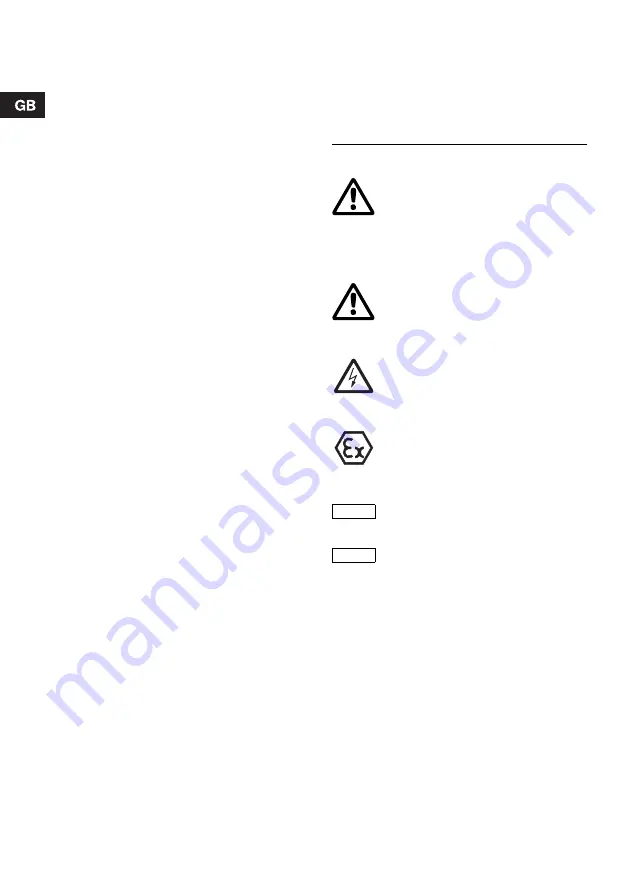
8
Original installation and operating instructions.
CONTENTS
Page
Symbols used in this document
General description
Operating conditions
Installation depth
Operating pressure
Operation
pH value
Liquid temperature
Density of pumped liquid
Approvals
Approval standards
Explanation to Ex approval
Identification
Nameplate
Type key
Safety
Transportation and storage
Installation
Installation on auto coupling
Free-standing submerged installation
Electrical connection
CIU unit (communication interface)
Electrical connection – single-phase
pumps
Electrical connection – three-phase
pumps
Alarm relay/communication connection
Configuration
10.1 Default settings
10.2 Pump alternation
10.3 Start level set
10.4 Thermal switches
Start-up 19
11.1 Before start-up
11.2 Operating modes
11.3 Direction of rotation
11.4 Resetting the pump
Maintenance and service
12.1 Recommended cleaning intervals
for sensors in standard pumps
12.2 Required cleaning intervals for
sensors in explosion-proof pumps
12.3 Inspection intervals
12.4 Adjustment of impeller clearance
12.5 Cleaning the pump housing
12.6 Cleaning the sensors
12.7 Checking/replacing the shaft seal
12.8 Oil change
12.9 Service kits
12.10 Built-in protection
12.11 Contaminated pumps
Fault finding chart
13.1 Megging
Technical data
14.1 Supply voltage
14.2 Enclosure class
14.3 Ex protection
14.4 Insulation class
14.5 Pump curves
14.6 Sound pressure level
Disposal
1. Symbols used in this document
2. General description
The electronic Grundfos DP and EF pumps
incorporate a controller and motor-protective
functions. They only need to be connected to the
mains supply.
The controller offers the following benefits:
•
Built-in level and dry-running sensors.
•
Built-in motor protection.
•
Pump alternation.
If several pumps are installed in the same tank,
the control logic incorporated in the pump will
ensure that the load is distributed evenly among
the pumps over time.
Warning
Prior to installation, read these
installation and operating instructions.
Installation and operation must comply
with local regulations and accepted
codes of good practice.
Warning
If these safety instructions are not
observed, it may result in personal
injury!
Warning
If these instructions are not observed,
it may lead to electric shock with
consequent risk of serious personal
injury or death.
Warning
These instructions must be observed
for explosion-proof pumps. It is
advisable also to follow these
instructions for standard pumps.
Caution
If these safety instructions are not
observed, it may result in malfunction
or damage to the equipment!
Note
Notes or instructions that make the job
easier and ensure safe operation.