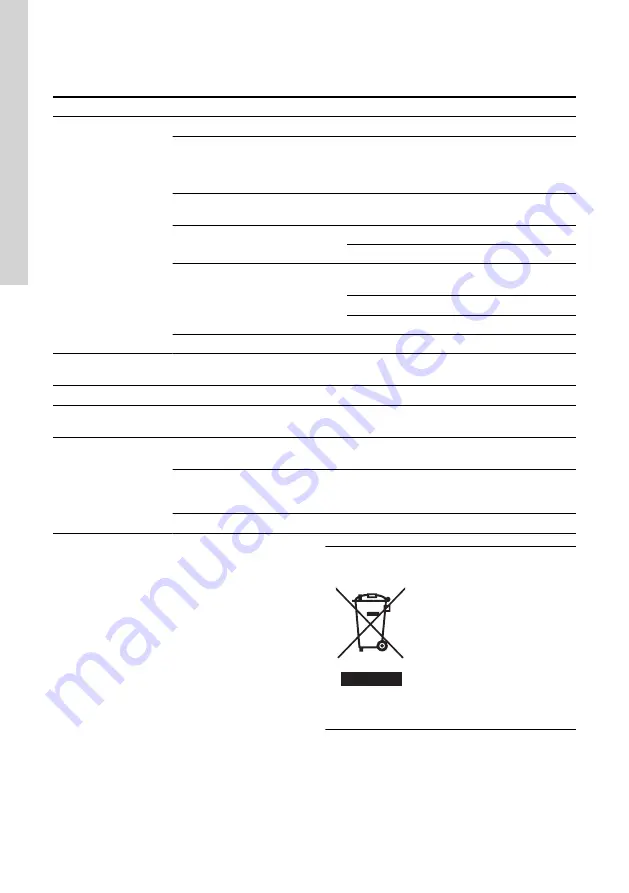
9. Fault finding chart
Fault
Cause
Remedy
The dosing has stopped
or the output is too low.
Valves leaking or blocked.
Check and clean the valves.
Valves incorrectly installed.
Remove and fit valves. Check that the arrow on
the valve casing is pointing in the liquid flow
direction. Check that all O-rings have been
fitted correctly.
Suction valve or suction pipe/hose
leaking or blocked.
Clean and seal the suction pipe/hose.
Suction lift too high.
Install the pump in a lower position.
Install a priming tank.
Viscosity too high.
Select the anti-cavitation function, see section
Anti-cavitation.
Install a pipe/hose with larger cross-section.
Fit spring-loaded valves.
Pump out of calibration.
Calibrate the pump, see section Calibration.
Pump dosing too little or
too much.
Pump out of calibration.
Calibrate the pump, see section Calibration.
Pump dosing irregularly. Valves leaking or blocked.
Check and clean the valves.
Leakage from drain
hole.
Diaphragm defective.
Install a new diaphragm.
Frequent diaphragm
failures.
Diaphragm not fastened properly.
Install a new diaphragm and ensure that the
diaphragm is fastened properly.
Counter-pressure too high
(measured at the pump discharge
port).
Check the system. Check the injection valve.
Sediment in dosing head.
Clean/flush the dosing head.
Related information
5.15 Anti-cavitation
7. Calibration
10. Disposing of the product
This product or parts of it must be disposed of in an
environmentally sound way.
1. Use the public or private waste collection service.
2. If this is not possible, contact the nearest
Grundfos company or service workshop.
The crossed-out wheelie bin
symbol on a product means
that it must be disposed of
separately from household
waste. When a product
marked with this symbol
reaches its end of life, take it
to a collection point
designated by the local waste
disposal authorities. The
separate collection and
recycling of such products will
help protect the environment
and human health.
See also end-of-life information at
www.grundfos.com/product-recycling
40
English (GB)
Содержание DME 150 AP
Страница 2: ......