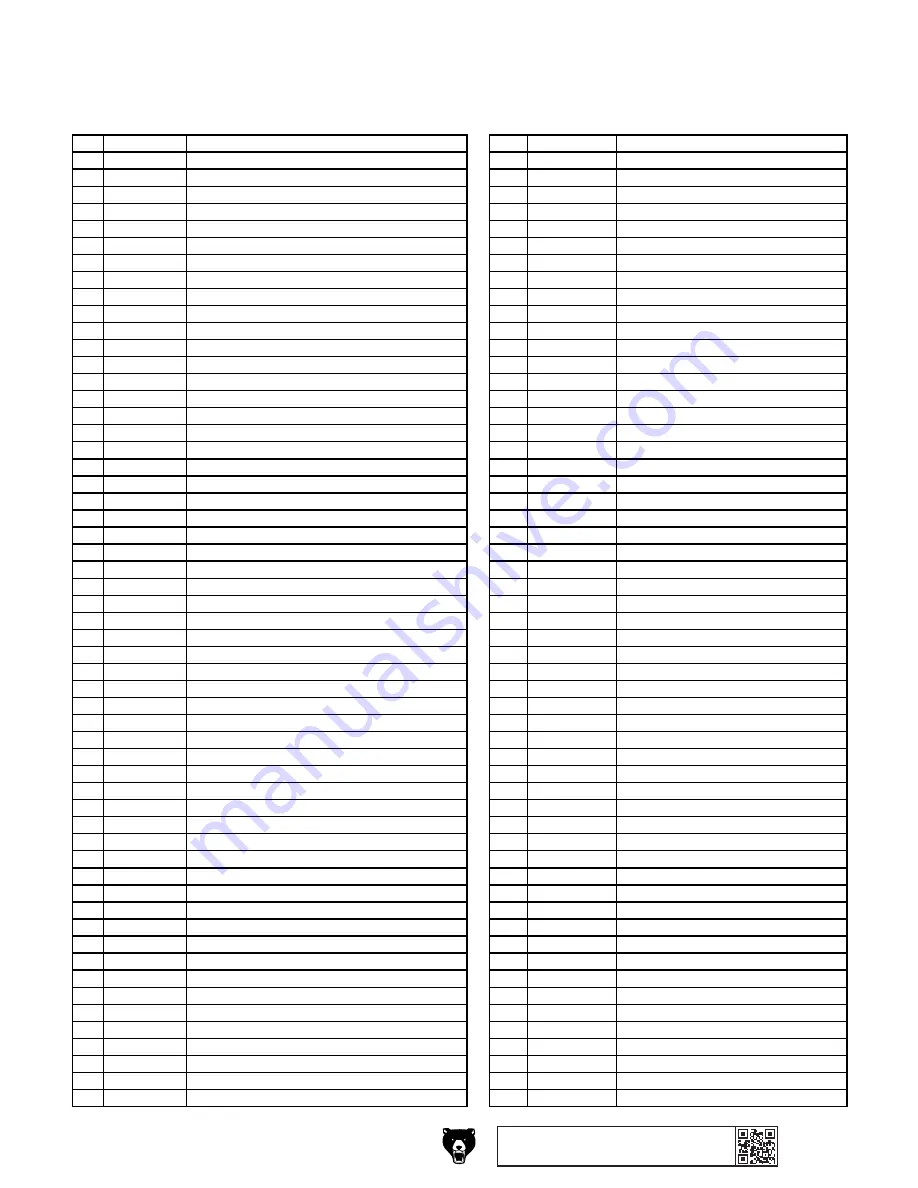
Model T31739 (Mfd. Since 11/19)
-39-
BUY PARTS ONLINE AT GRIZZLY.COM!
Scan QR code to visit our Parts Store.
REF PART #
DESCRIPTION
REF PART #
DESCRIPTION
1
PT31739001
BASE
58
PT31739058
HEX NUT M12-1.75
2
PT31739002
COLUMN SEAT
59
PT31739059
RETURN SPRING COVER
3
PT31739003
HEX BOLT M8-1.25 X 20
60
PT31739060
FLAT COIL SPRING
4
PT31739004
COLUMN
61
PT31739061
HEADSTOCK
5
PT31739005
RACK
62
PT31739062
CAP SCREW M8-1.25 X 12
6
PT31739006
REVOLVING HANDLE 20 X 75, M10-1.5 X 10
63
PT31739063
FLAT WASHER 8MM
7
PT31739007
SET SCREW M6-1 X 10
64
PT31739064
COMPRESSION SPRING 2 X 22 X 80
8
PT31739008
LOCK HANDLE 15 X 78, M10-1.5 X 25
65
PT31739065
SPEED SHAFT
9
PT31739009
WORM SHAFT
66
PT31739066
LED BULB 1W 3.5V
10
PT31739010
WORM GEAR PIN
67
PT31739067
LASER DKLD 1801
11
PT31739011
WORM GEAR
68
PT31739068
LASER COVER
12
PT31739012
WORM GEAR HOUSING
69
PT31739069
PINION GEAR
13
PT31739013
COLUMN RING
70
PT31739070
DOWNFEED LEVER HUB M10-1.5
14
PT31739014
HEX BOLT M12-1.75 X 25
71
PT31739071
KNOB BOLT M10-1.5 X 10, D40, ROUND
15
PT31739015
TABLE MOUNTING ARM
72
PT31739072
LASER SEAT
16
PT31739016
TABLE
73
PT31739073
SET SCREW M6-1 X 10
17
PT31739017
EXTENSION ROD 1/2" X 8-3/4"
74
PT31739074
HEX BOLT M10-1.5 X 40
18
PT31739018
KNOB BOLT M8-1.25 X 18, D36, WING
75
PT31739075
FLAT WASHER 10MM
19
PT31739019
EXTENSION ROLLER BRACKET
76
PT31739076
MOTOR MOUNT PLATE
20
PT31739020
EXTENSION ROLLER
77
PT31739077
HEX BOLT M8-1.25 X 16
21
PT31739021
FLAT HD CAP SCR M6-1 X 12
78
PT31739078
MOTOR 1/3HP 120V 1-PH
22
PT31739022
CAP SCREW M10-1.5 X 20
78-1
PT31739078-1 MOTOR FAN COVER
23
PT31739023
DRILL CHUCK JT3 X 1/32"-5/8" KEYLESS
78-2
PT31739078-2 MOTOR FAN
24
PT31739024
DRILL CHUCK ARBOR 5/8"
78-3
PT31739078-3 CAPACITOR COVER
25
PT31739025
SPINDLE
78-4
PT31739078-4 S CAPACITOR 24M 250V 40 X 90
26
PT31739026
BALL BEARING 6204ZZ
78-5
PT31739078-5 MOTOR JUNCTION BOX
27
PT31739027
QUILL
78-6
PT31739078-6 BALL BEARING 6203ZZ
28
PT31739028
BALL BEARING 6201ZZ
78-7
PT31739078-7 MOTOR CORD 3G 3W 39"
29
PT31739029
CLAMP BOLT M12-1.75 X 2
79
PT31739079
HEX NUT M10-1.5
30
PT31739030
COMPRESSION SPRING 1.2 X 6
80
PT31739080
KEY 4 X 4 X 80 SE
31
PT31739031
LOCK NUT M8-1.25
81
PT31739081
MOTOR SPRING SEAT
32
PT31739032
QUICK-RELEASE DEPTH STOP
82
PT31739082
COMPRESSION SPRING 2 X 33 X 78
33
PT31739033
DEPTH STOP SUPPORT NUT
83
PT31739083
MOTOR PULLEY SET
34
PT31739034
THREADED DEPTH ROD
84
PT31739084
SET SCREW M6-1 X 10
35
PT31739035
HEX NUT M6-1
85
PT31739085
PHLP HD SCR M4-.7 X 16
36
PT31739036
DEPTH STOP BRACKET
86
PT31739086
EXT RETAINING RING 16MM
37
PT31739037
CAP SCREW M6-1 X 20
87
PT31739087
SPEED SENSOR MOUNT
38
PT31739038
PHLP HD SCR M5-.8 X 16
88
PT31739088
FLAT WASHER 5MM
39
PT31739039
ROCKER SWITCH GORBO XCK-017 10(4)A 250V
89
PT31739089
PHLP HD SCR M5-.8 X 20
40
PT31739040
MAG ON/OFF SWITCH DKLD DZ04 10A 120V
90
PT31739090
SPEED SENSOR DKLD CB07-5C
41
PT31739041
E-STOP BUTTON LAY5-BE102 10(6)A 400V
91
PT31739091
TAP SCREW M2.9 X 6
42
PT31739042
DISPLAY SCREEN COVER
92
PT31739092
EXT RETAINING RING 17MM
43
PT31739043
SWITCH BOX
93
PT31739093
BALL BEARING 6203ZZ
44
PT31739044
TAP SCREW M3 X 8
94
PT31739094
BUSHING 39 X 27 X 10
45
PT31739045
DIGITAL DISPLAY DKLD CB07-6A
95
PT31739095
SPINDLE PULLEY SHAFT
46
PT31739046
CHUCK KEY HOLDER
96
PT31739096
KEY 4 X 4 X 65 SE
47
PT31739047
DEPTH STOP BRACKET
97
PT31739097
EXT RETAINING RING 24MM
48
PT31739048
PHLP HD SCR M5-.8 X 12
98
PT31739098
BELT GUARD
49
PT31739049
LOCK NUT M10-1.5
99
PT31739099
SPINDLE PULLEY SET
50
PT31739050
FLAT WASHER 10MM
101
PT31739101
EXT RETAINING RING 35MM
51
PT31739051
SPEED HANDLE HUB
102
PT31739102
INT RETAINING RING 50MM
52
PT31739052
FLAT HD SCR M5-.8 X 16
103
PT31739103
BALL BEARING 61907-ZZ
53
PT31739053
SPEED ADJUST PLATE
104
PT31739104
SPEED SEAT
54
PT31739054
KEY 4 X 4 X 12 SE
105
PT31739105
SET SCREW M10-1.5 X 20
55
PT31739055
SPEED CONTROL GEAR
106
PT31739106
POLY V-BELT AX35
56
PT31739056
SPEED CONTROL KNOB SHAFT
107
PT31739107
POWER CORD 18G 3W 39.5" 5-15P
57
PT31739057
KNOB M8-1.25, D32, BALL
108
PT31739108
LEVER
Main Parts List
Содержание T31739
Страница 44: ......