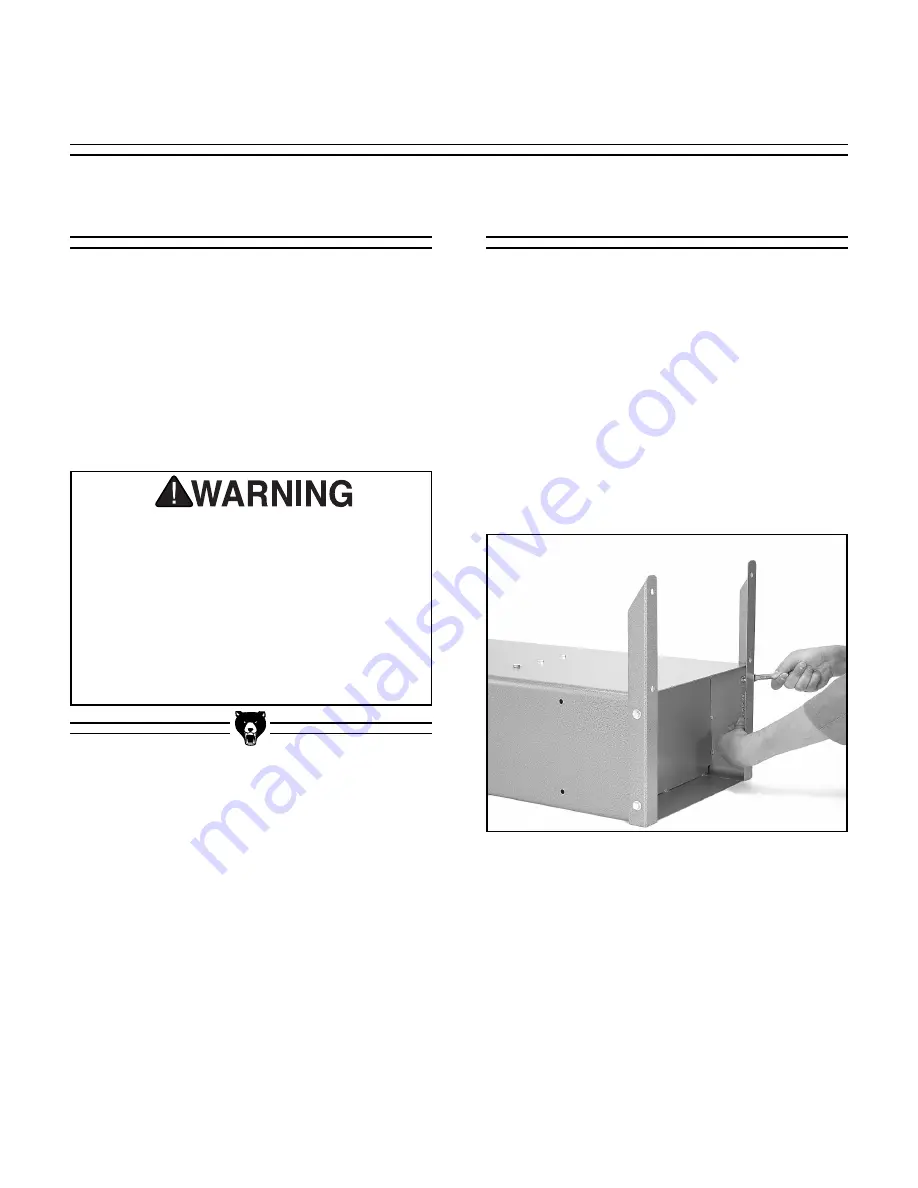
G1495 Heavy-Duty Wood Lathe
-11-
Pre-assembly
Assembly of the G1495 is straightforward. We
have organized the assembly process into steps.
Please follow them in sequence.
Tools Required: Only a few common tools are
needed to assemble this machine. Specifically,
two 12mm open end wrenches, a 6mm Allen
®
wrench (supplied), a Phillips
®
screwdriver and a
plumb bob.
SECTION 4: ASSEMBLY
Stand
Figure 4. Attaching base brackets to stand.
(Stand is lying down on its front)
The stand components are most easily assem-
bled on their sides, then stood up and joined
together:
1. Attach the two base brackets to the base of
the cabinet using four (4)
5
⁄
16
'' - 18 x
3
⁄
4
'' bolts
and nuts. Use two (2) washers for each bolt,
one under the head of the bolt, one next to
the nut. These brackets are used when the
lathe is going to be bolted to the floor or
other type of support structure. See Figure
4.
All die-cut metal parts have a sharp edge
(called “flashing”) on them after they are
formed. This is generally removed at the fac-
tory. Sometimes a bit of flashing might
escape inspection, and the sharp edge may
cause cuts or lacerations when handled.
Please examine the edges of all die-cut
metal parts and file or sand the edge to
remove the flashing before handling.
2. Attach the third base bracket to the right
hand stand using two (2)
5
⁄
16
'' - 18 x
3
⁄
4
''
bolts, washers and nuts.