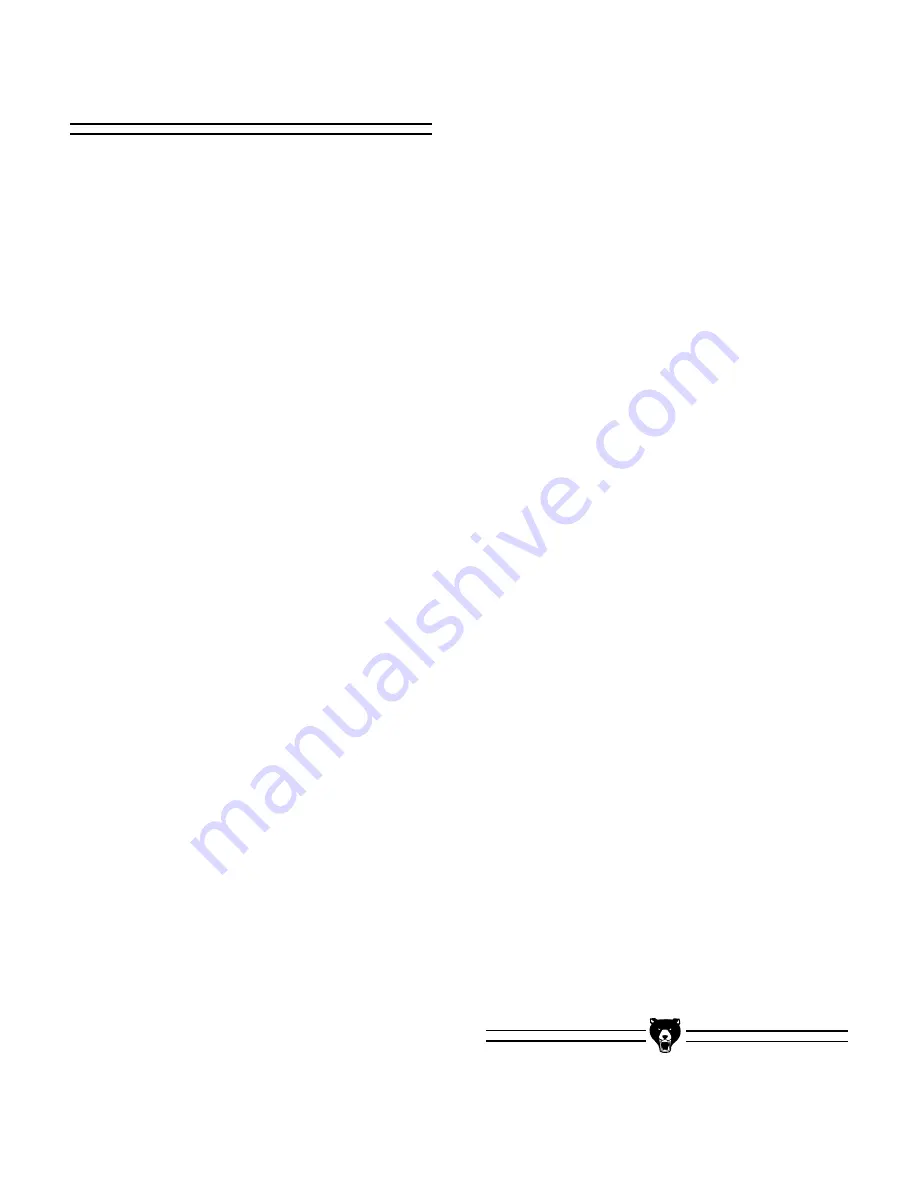
-22-
G1033 20" Planer
Wood Characteristics
The species of wood, as well as condition, will
affect planing ability. The harder the wood, the
more difficult it will be to plane. We’ve included
below, a list of wood characteristics you may
encounter when planing. The following descrip-
tions of defects will give you some possible
answers to problems you may encounter while
planing different materials. Possible solutions fol-
low the descriptions.
Chipped Grain
- usually a result of cutting
against the grain, or planing wood with knots or
excessive amount of cross grain. Chipped grain
can also be caused by dull knives or misaligned
chipbreaker. Often, chipped grain can be avoided
by slowing down the feed rate and by taking shal-
low cuts. If those options do not work, inspect
your lumber and determine if its grain pattern is
causing the problem. If the wood does not show
substantial crossgrain, inspect your knives for
sharpness and inspect the chipbreaker for prop-
er alignment. See the Adjustment Section.
Fuzzy Grain
- Usually caused by surfacing lum-
ber with too high a moisture content. Sometimes
fuzzy grain is a characteristic of some woods,
such as basswood. Fuzzy grain can also be
caused by dull knives or an incorrect grinding
bevel. Check with a moisture meter. If moisture is
greater than 20%, sticker the wood and allow to
dry. Otherwise, inspect knife condition.
Glossy Surface
- Usually caused by dull knives
taking shallow cuts at a slow feed speed. Surface
gloss will usually be accompanied by overheat-
ing. Often, lumber will be scorched and eventual-
ly, damage to knives will occur. If knives are
sharp on inspection, increase feed speed and/or
cutting depth.
Snipe
- Occurs when board ends have more
material removed than the rest of the board.
Usually caused when one or both of the bed
rollers are set too high. Can also be caused by
the chipbreaker or pressure bar being set too
high. However, small amount of snipe is
inevitable.
Snipe can be minimized by proper adjustment of
the planer’s components, but complete removal
of snipe is extremely unlikely. More likely, you will
be able to reduce it to a tolerance of .002". If
snipe under that level is a problem, consider
planing lumber longer than your intended work
length and cut off the excess after planing is com-
pleted.
Uneven Knife Marks
- Uneven knife marks can
occur when the chipbreaker is set too high.
Inspect cutterhead bearings if re-adjustment of
the chipbreaker fails to remedy the situation.
Chatter Marks
- Usually caused by incorrect
chipbreaker and pressure bar setting heights.
Chatter marks can also be caused by running a
narrow wood piece through the planer at either
the right or left end of the cutterhead. Chatter, like
uneven knife marks, will show in the form of a
''washboard'' look. Chatter marks are more likely
to be inconsistent in appearance than uneven
knife marks.
Wavy Surface
- Caused by poor knife height
adjustment, wavy surface appears when one
knife is taking deeper cuts than the rest of the
knives. Remedy by re-setting the knives to a tol-
erance of ± .001".
Pitch & Glue Build-up
- Glue and resin build-up
on the rollers and cutterhead will cause over-
heating by decreasing cutting sharpness while
increasing drag in the feed mechanism. The
result can include scorched lumber as well as
uneven knife marks and chatter.
Chip Marks
- Occur when chips aren’t properly
expelled from the cutterhead. The knives catch
the chips and drag them across the lumber being
planed. Chips tend to be random and non-uni-
form (as compared to chipped grain). Can be
caused by exhaust blockage or too much room
between the cutterhead and chip deflector. Using
a dust collection system in combination with the
planer can help reduce chip marks. Inspect the
chip deflector and readjust (as described earlier
in the text).
Содержание G1033Z
Страница 4: ......
Страница 40: ...36 G1033 20 Planer...