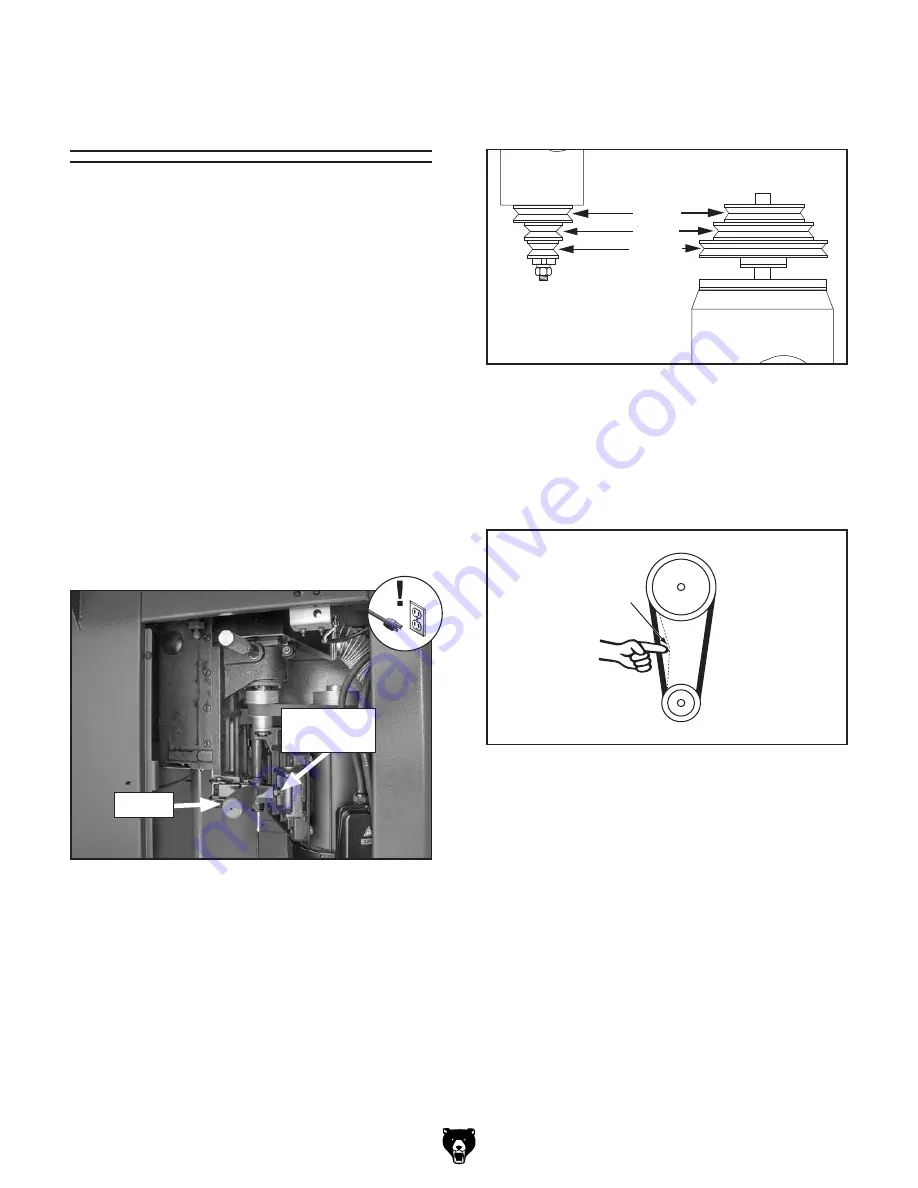
Model G0900 (Mfd. Since 03/20)
-45-
4. Tighten belt by replacing motor bracket han-
dle. When belt is properly tensioned, there
should be approximately
1
⁄
4
" of deflection in
the center of the belt when you press it with
your thumb, as shown in
Figure 67.
V-Belt Tension &
Replacement
The V-belt transfers power from the motor to the
spindle. If the V-belt does not have the proper
tension or is damaged in any way, the shaper will
not operate optimally, and unnecessary wear on
the moving parts will occur. Regularly check the
V-belt tension and replace it when necessary.
Tools Needed
Qty
Open-End Wrench or Socket 19mm ................. 1
To tension V-belt:
1. DISCONNECT MACHINE FROM POWER!
2. Open cabinet access door, then release belt
tension by pulling motor bracket handle (see
Figure 65).
— If V-belt is cracked, excessively worn, or
damaged, replace V-belt.
3. Move V-belt to sheave on motor and spindle
pulleys to select desired speed (see
Figure
66.)
Pulley
Deflection
Pulley
Figure 67. Checking V-belt tension.
Figure 66. Different speed options.
5,000
7,000
10,000
5. If there is not
1
⁄
4
" of deflection, adjust belt ten-
sion by loosening/tightening adjustment hard-
ware on motor bracket handle until proper
tension achieved, see
Figure 65.
6. Spin pulley by hand to ensure proper tracking.
7. Close access door.
Figure 65. Handle for motor tension.
Handle
1
⁄
4
"
Adjustment
Hardware
Содержание G0900
Страница 68: ......