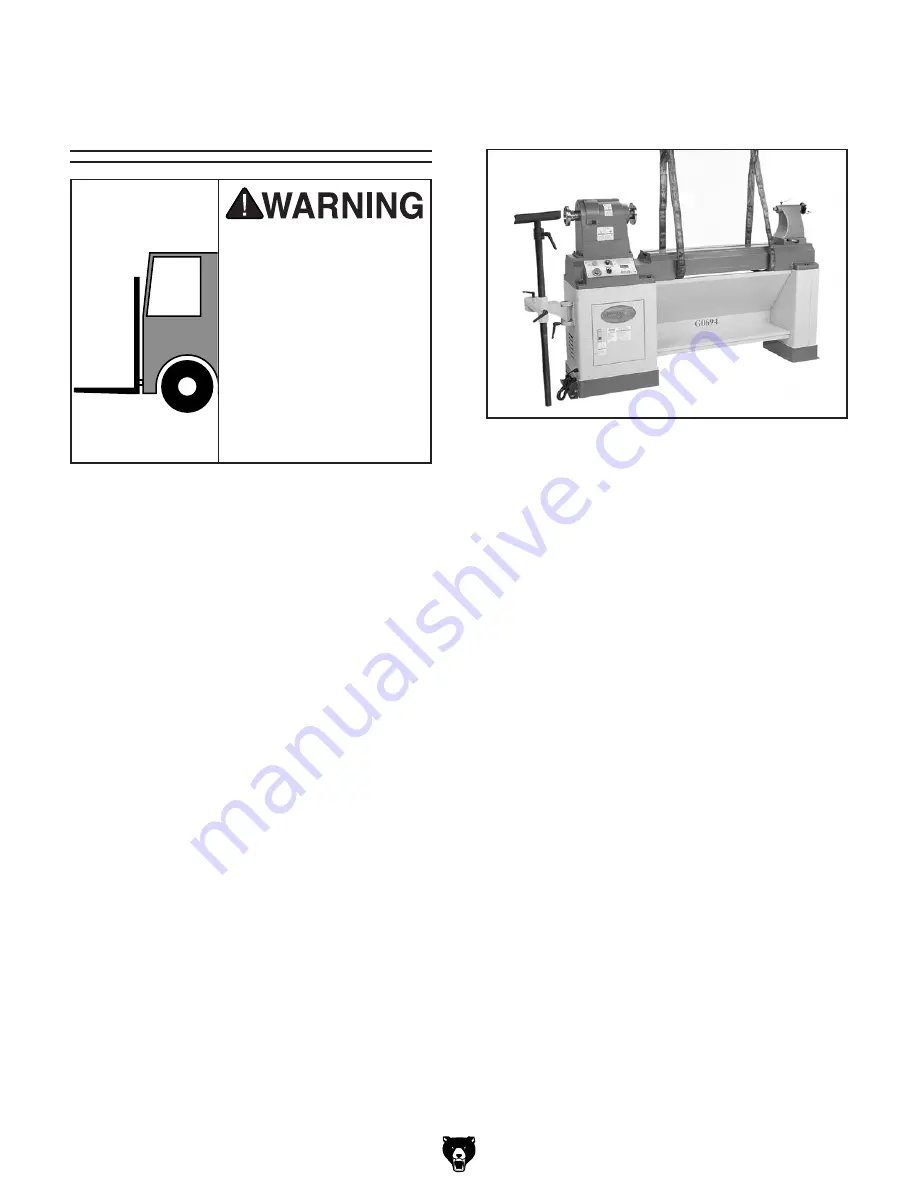
-14-
model g0694 (mfg. since 1/09)
Moving & Placing
Lathe
The Model G0694 is a
heavy machine (approx.
580 lbs.) Serious per-
sonal injury may occur
if safe moving methods
are not used. To be safe,
get assistance and use
power lifting equipment
rated for at least 750 lbs.
to move the shipping
crate and remove the
machine from the crate.
To move and place your lathe:
1. remove the top crate from the shipping pal-
let.
2. to help balance the load, lock the outboard
tool rest assembly as close as possible to the
lathe body, then move the tailstock and cen-
ter tool rest assembly to the extreme right of
the bedway.
3. remove the small items from the shipping
pallet, then remove the lag bolts securing the
lathe to the pallet.
figure 6. Lifting straps positioned to lift the lathe.
4. Feed the lifting straps under the bedway, as
shown in
figure 6, making sure they spread
as wide as possible.
5. With assistance, steady the load and lift the
lathe from the shipping pallet.
— if the load is unbalanced, immediately
lower the lathe and reposition the lifting
straps as necessary. repeat this step until
you are satisfied that the load is safely bal-
anced.
6. have an assistant steady the load to keep it
from swaying as you lift the lathe only enough
to clear the shipping pallet and any floor
obstacles, then move it to its working loca-
tion.