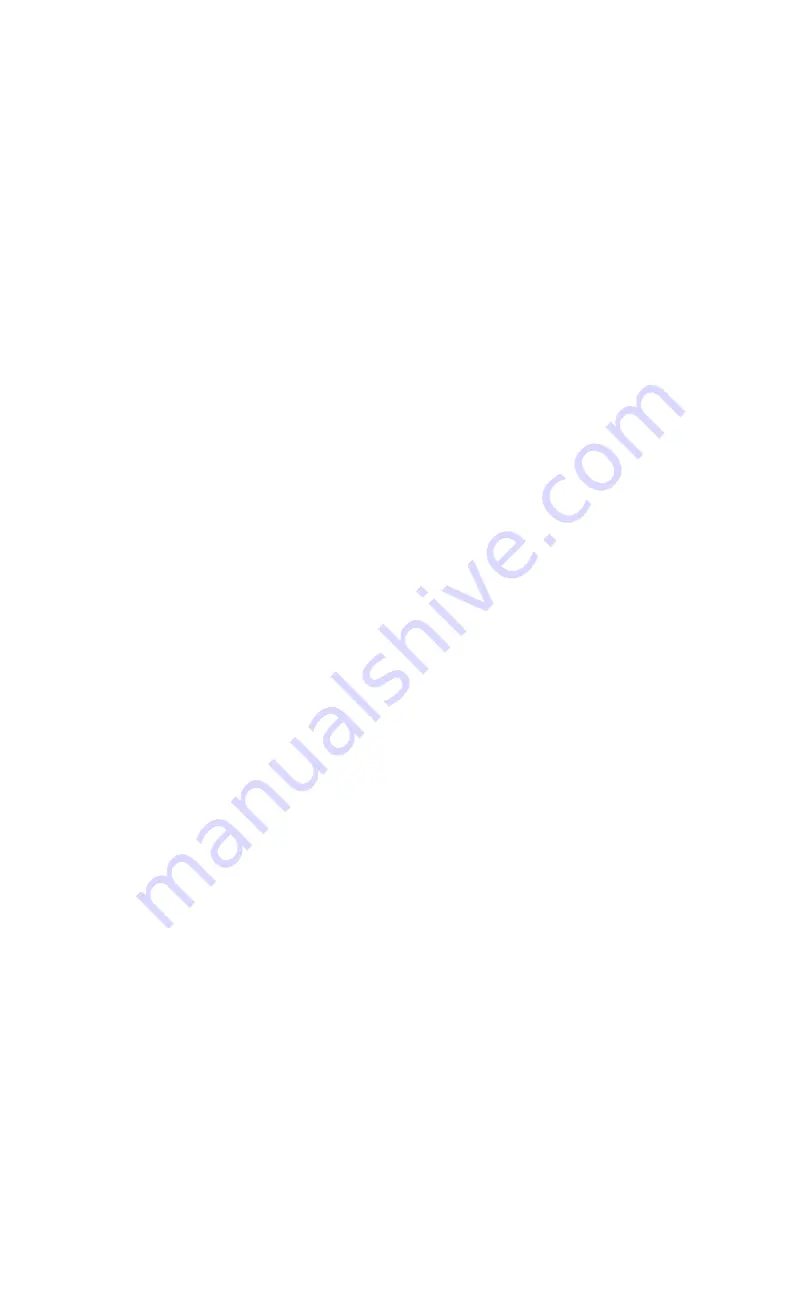
Page 5
MODBUS TROUBLE-SHOOTING
The CO2/RH/T device operates as a slave. It will not communicate unless a master is connected
to the network and sends a request for information, then the slave will answer. If the device does
not communicate properly, first check that the communication wires are not reversed. Then check
the communication parameters in the menu in the following sequence: Slave address, baud rate,
transmission mode, parity bit, stop bit, RTU mode CRC polynomial and slave response delay.
The factory default Modbus address is 01 and each device must have its unique address to communicate
properly on the bus. Use the menu as described above to change the Slave address to a unique number
for each unit.
The default Modbus baud rate is 9600. Use the menu to change the baud rate to the correct setting.
The default transmission mode is RTU. If this is incorrect, use the menu to change the transmission mode
to ASCII.
The default Modbus parity is N for None. If this is not correct, use the menu to change the parity from
None to Odd or Even.
The default stop bits is 1. Use the menu to change the stop bit setting to 2. For some configurations the
value is fixed.
The default Modbus CRC value is A001. The menu can be used to change this setting. This only applies
to RTU mode and has no effect in ASCII mode. It is the CRC polynomial setting and can be changed
between A001, 1021, 8005 or 8408.
The default Modbus delay is minimum (0). This can be changed as described above. It is the slave
response delay and can be set from minimum to 350ms. For example, the minimum delay means 3.5
character time delays or 4ms for 9600 baud rate.
CALIBRATION
Calibration with gas requires a field calibration kit consisting of an LCD, a bottle of 1000 ppm CO2 gas, a
tank pressure regulator with flow restrictor and the necessary tubing to connect to the device.
Note that because of the Automatic Calibration Mode and other technology incorporated into the CDD
series, only a single point 1000 ppm calibration is required to meet specified accuracy.
Turn the regulator on/off knob fully off and attach it to the 1000 ppm CO2 gas bottle and firmly
tighten it by hand. Remove the cover of the unit to be calibrated to expose the gas sensor chamber.
The tubing from the gas bottle can be connected to either port on the chamber after the plastic cap is
removed. Gently remove one cap and connect the tubing, note that strong shock or vibration can affect
calibration.
Ensure the device has been operating normally for at least five minutes before applying gas. Slowly turn
the valve knob on the regulator to let the gas begin flowing.
The regulator will restrict the flow rate to the specified 100 ml/min. After a brief period the gas will flow
into the chamber and the CO2 reading on the LCD will begin to approach 1000 ppm. Wait 1 to 2 minutes
until the CO2 reading stabilizes.
Enter the Setup menu and use the <MENU> key to advance to Calibrat 1000 PPM. Press and hold the
<SAVE> key for 2 seconds and the display will change to Waiting Calibrat then to Waiting 5 minute to
indicate that the process of reprogramming the internal calibration setting is taking place.
This calibration process takes about 5 minutes and the LCD will count down the minutes. Do not disturb
the unit or the gas flow during this period. When calibration is complete the unit will display Calibrat
Done. Press the <SAVE> key to return to normal operation and then the gas can be shut off.
Disconnect the tubing and replace the cap on the sensor chamber as calibration is complete.
IN-GE-CDD3B1XXXMOD-01-03 11/19 Copyright © Greystone Energy Systems, Inc. All Rights Reserved Phone: +1 506 853 3057 Web: www.greystoneenergy.com