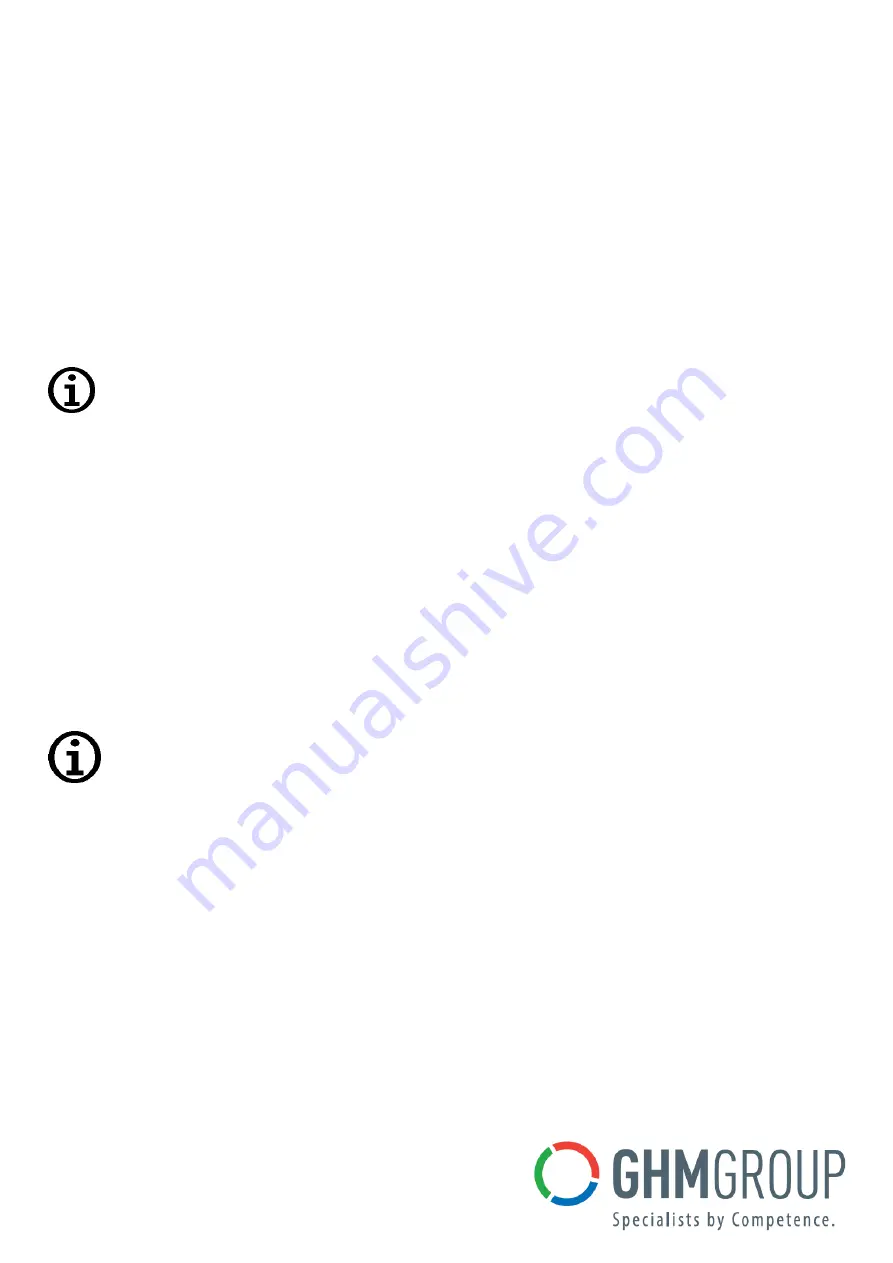
GHM GROUP - Greisinger
GHM Messtechnik GmbH
Hans-Sachs-Str. 26
93128 Regenstauf | GERMANY
Measurement accuracy and calibration
Measurement accuracy of the overall system with careful calibration and measurement:
1-point calibration: ± 0.2% O2 ± 1 digit for concentrations <10% O2
2-point calibration: ± 0.1% O2 ± 1 digit for concentrations <10% O2
This must be selected in the menu in advance, depending on the type of calibration that should be used.
Two-point calibration can be conducted with GMH 5695 for the most accurate measurements. A second reference
medium is required in addition to air. Pure nitrogen (in cylinders, minimum recommended purity 3.5: 99.95%) is
recommended for checking protective atmospheres with little oxygen (<1% O
2
vol.). This corresponds to 0.0% O
2
vol.
Please refer to the GMH 5695 operating manual for detailed information about 2-point calibration.
Checking the calibration
In order to assure measurement accuracy, we recommend checking the calibration at the beginning of the work day. A
simple check can take place with normal environmental air.
The sensor must assume the environmental temperature before the check and/or calibration. Therefore, we recommend
storing the device in the installation location so that it is ready for use quickly. To check the calibration, remove the
protective cover of the needle and draw in environmental air with the help of the gas pump (‘flushing’).
The sensor housing may contain residual gas. Incorrect calibrations can occur if the sensor housing
cannot be flushed!
The device should display an oxygen level of 20.7 to 21.2 % vol. O
2
after approximately 10 seconds. If the value
deviates by more than 0.3 % vol. O
2
, we recommend calibrating the devices as specified in the GMH 5695 operating
manual (chapter: Calibration of the oxygen sensor).
Measurement
Preparation
Prior to taking measurements, ensure that the device has been calibrated correctly (see above) and is ready for use
–
e.g. sensor needle not clogged / filter not contaminated, etc.
Prior to conducting the measurement, apply a GOG *) seal sticker on the package (refer to the figure on page 1).
This assures that the package is not torn when punctured with the needle and it prevents external air from being drawn
in between the needle and package, which would falsify the measurement.
This is essential for measurement accuracy for stiff packages with low gas volumes, in particular.
Procedure:
1. Puncturing: Puncture the seal sticker with the needle of the oxygen sensor until it reaches a hollow space in the
package.
When puncturing the package, ensure that no particles or fluids are drawn in. The filter prevents
contamination of the sensor. However, the puncturing needle / filter can become clogged if
particles/fluids are drawn in.
2. Suctioning: Switch on the gas pump with at the right side. Now the gas mixture in the package is suctioned for
measurement of the residual oxygen.
3. Measuring: The T
90
response time is < 10 s. It becomes recognisable that the device is approaching the minimum
value as the value begins to drop increasingly slowly (or increases for O2 > 21%) and stabilises. The minimum value
(or maximum value for O2 > 21 % vol. O
2
) reflects the residual oxygen content.
Recommendation:
Use the min/max function with the appropriate buttons for the recording. Press and hold the
appropriate button for 2 seconds to reset the sensor prior to each new measurement.
4. Storing: If you would like to store measurements, activate the individual value logger. Now you can store any arbitrary
measurements by pressing the Store button (insert figure).
If a suitable data transmission cable is present, the stored values can be conveniently transmitted to a PC via the
data logger.
5. Cleaning: After the measurement, the sensor and puncturing needle should be flushed using a gas pump for
approximately 30 seconds. This will clear the gas mixture out of the sensor.
*) GOG-A for predominantly soft package material
GOG-B for stiff and compact package trays