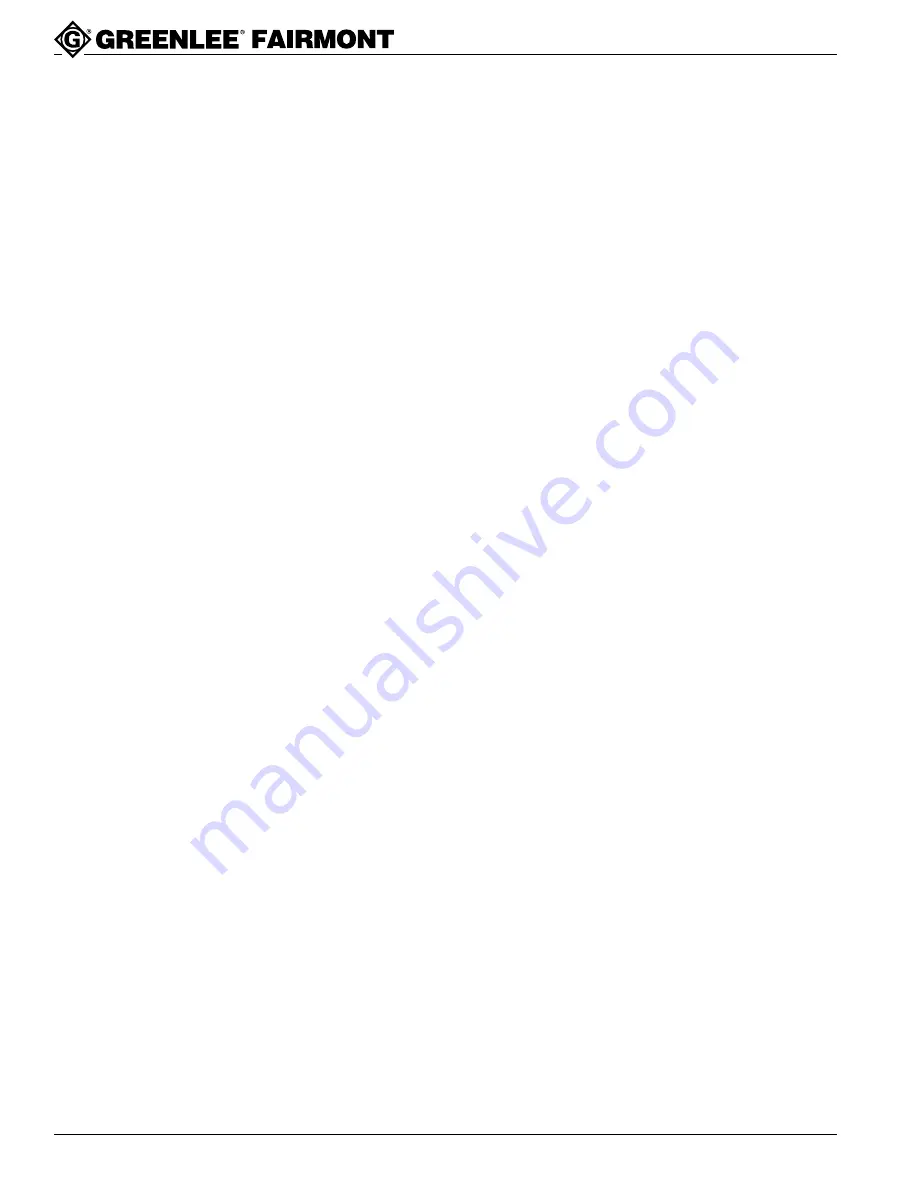
Greenlee Textron / Subsidiary of Textron Inc.
20
H8508 Hydraulic Impact Wrench
4455 Boeing Dr., Rockford, IL 61109-2988 815/397-7070
Disassembly (cont’d)
Trigger and Control Spool - 48696
(See Figures 5 and 7)
1.
Remove spring pin (42) from trigger spool (29) by
pressing or tapping with a hammer and punch.
Note:
Support trigger (41) so pressing or tapping
does not bend trigger spool (29).
2.
Remove washer (39), spring (38), snap ring (37),
and washer (36). Trigger spool (29) may now be
pushed out of handle (1). Push spool toward trigger
side of tool.
3.
Remove snap ring (33). Open-Center/Closed-
Center spool (31) may now be removed to service
O-ring (34).
4.
Ball (32) is loose in this assembly. Take caution to
catch ball when it falls free.
Reversing Spool
1.
Remove reversing spool (19) by loosening and
removing cap (24) on left side of tool and pulling
spool (19) out right side of tool.
Note:
For tool orientation (left and right) grip tool
as you would use it and view tool looking at
motor cap (6). See Figure 12.
Note:
Attempting to push the reversing spool (19)
the opposite way through the bore will
cause damage to O-rings (25 & 26) and
could allow particles of O-ring to get into
motor.
2.
Remove plug (22), spring (21) and poppet (20).
3.
Repeat procedure for right side of reversing
spool (19).
Note:
If set screws (23 & 60) have not been
disturbed and internal components are
returned to the same side of spool (19),
the relief valve setting may not have been
affected and tool will perform properly
when assembled.
Note:
Relief valve setting may require checking
when tool is reassembled.
Assembly
Inspection
1.
Motor Cap (6) and Handle (1). Mating surfaces,
gear cavities, oil passageways, etc.; must be
smooth and free of grooves or nicks. If either
component has grooves or nicks, replace the
component as an assembly with the bearings
already pressed in.
2.
Drive Shaft (8), Idler Shaft (13) and Gears (10). All
surfaces, including gear teeth, must be smooth and
free of grooves or nicks. If any component is
damaged, replace the component.
3.
Bearing (3 & 7). Hold motor cap or handle assembly
in one hand or place on a flat surface. Insert drive
shaft (8) or idler shaft (13) into bearing. Spin the
shaft. The shaft should turn smoothly. If any rough-
ness is noted, Greenlee Fairmont recommends
replacing the component as an assembly with the
bearings already pressed in.
4.
Bearing (56) in hammer case cap (55). Slide anvil
(49) into bearing (56). Turn anvil (49). The anvil
should turn smoothly. If any roughness is noted,
check anvil surface. If problem is the bearing
surface, replace hammer case cap assembly as an
assembly with the bearing already pressed in.
5.
Thrust bearing (43) and thrust washers (44). Turn
bearing on washer surfaces. Bearing should roll
smoothly. If any roughness is felt, replace the
components.
6.
Trigger Spool (29). All surfaces must be free of
grooves or nicks. If the component has grooves or
nicks, replace the component.
7.
Reversing Spool (19). All surfaces must be free of
grooves or nicks. If the component has grooves or
nicks, replace the component.
8.
Hammer Frame (46), Anvil (49), Hammers (47) and
Pins (48). All surfaces must be free of grooves,
nicks, or cracks. If any component has grooves,
nicks, or cracks, replace the component.
9.
O-rings. Always replace O-rings in components that
have been disassembled with new O-rings during
assembly. A packing kit is available that includes all
O-rings and gaskets.
10. Gasket (15). Always replace gaskets when motor
cap or hammer case is removed from handle
assembly.