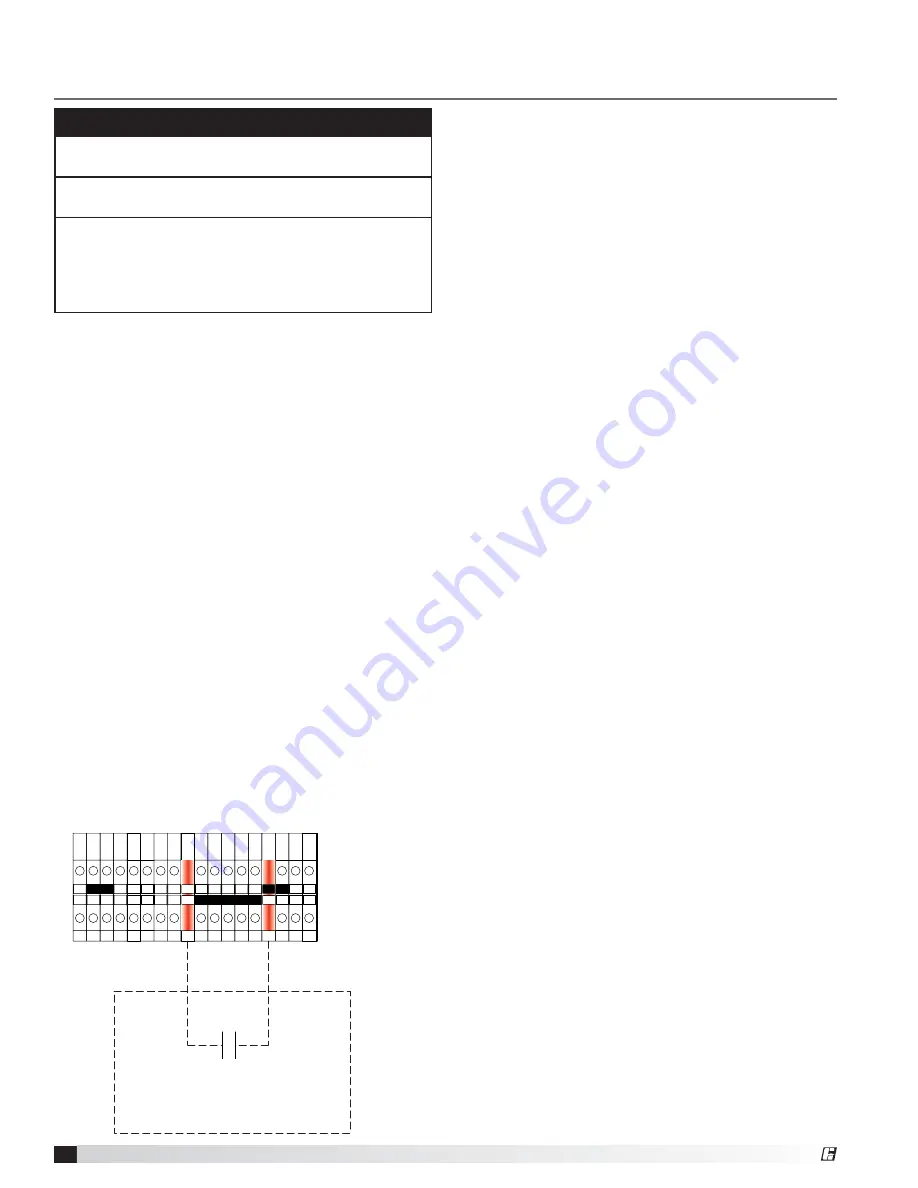
6
VGN Technology
®
BMS Communication
(hard wire connections)
Nozzle Feedback
will report the position of the nozzle
during operation. It is necessary to maintain minimum
required nozzle outlet velocity. Each nozzle has two
feedback outputs, one for each blade of the nozzle.
Connect BMS to 1NZFB1 and COM. Connect BMS to
1NZFB2 and COM.
Wire Landing Points
• Fan 1: 1NZFB1 and COM and 1NZFB2 and COM on
the terminal strip
• Fan 2: 2NZFB1 and COM and 2NZFB2 and COM on
the terminal strip,
if applicable
• Fan 3: 3NZFB1 and COM and 3NZFB2 and COM on
the terminal strip,
if applicable
• Fan 4: 4NZFB1 and COM and 4NZFB2 and COM on
the terminal strip,
if applicable
Fan Flow
This feature is not required for system
operation. This feature allows the BMS to record and
display the CFM of the fan during operation. Connect
BMS to 1SURAR and COM.
Wire Landing Points
• Fan 1: 1SURAR and COM on the terminal strip
• Fan 2: 2SURAR and COM on the terminal strip,
if applicable
• Fan 3: 3SURAR and COM on the terminal strip,
if applicable
• Fan 4: 4SURAR and COM on the terminal strip,
if applicable
Alarm
will notify the BMS of issues with the VGN
control system by closing a dry relay contact within
the VGN Carel controller. Connect BMS to ALM1 and
ALMCOM.
Wire Landing Points
• Entire System: ALM1 and ALMCOM on the
terminal strip
NOTE:
There is only one alarm contact for the entire
VGN control system regardless of the number of fans.
Variable Geometry Nozzle (VGN) Controller to VFD and BMS Hardwiring
Instructions
Make sure the numbering of the fans is consistent
during the entire wiring installation; fan 1 will require
wiring specific to fan 1, fan 2 will require specific wiring,
along with fans 3 and 4 if applicable.
Fan Run Signal
(hard wire connections)
The VGN controller requires a 24 VAC fan run input
signal to communicate to the VGN controller that the fan
is running. The VGN controller will supply the 24 VAC
voltage required, but it will need to be switched on
and off by the Building Management System (BMS) or
Variable Frequency Drive (VFD) based on the fan run
status. Use a relay contact controlled by the VFD or
BMS to control the fan run signal; the contact should
be closed when the fan is running. Connect the +24V
terminal in the VGN controller to the input of the relay
contact. Connect the normally closed (NC) switched
side of the relay contact to the 1FNRUN terminal in the
VGN controller. The VGN controller will not function
without the 24 VAC fan run signal.
Wire Landing Points
• Fan 1: +24 V and 1FNRUN on the terminal strip
• Fan 2: +24 V and 2FNRUN on the terminal strip,
if applicable
• Fan 3: +24 V and 3FNRUN on the terminal strip,
if applicable
• Fan 4: +24 V and 4FNRUN on the terminal strip,
if applicable
NOTE
All field installation and wiring of electrical equipment
must be done to meet NEC, CEC and local codes.
Be sure to use appropriately sized wire for the full load
amp draw.
Once the following hardwiring is complete, please
refer to the BMS Communication Programming
section for details on programing the BMS to
communicate with the VGN controller via the hard
wire connections.
COM
COM
1FNRUN
COM
COM
COM
1SURAR
GND
GND
1SURAR
1NZVDC
1NZFB1
1NZFB2
+24V
+24V
ALM1
ALMCOM
TEST
VFD BY OTHERS:
Relay output on VFD to close when
fan is running.