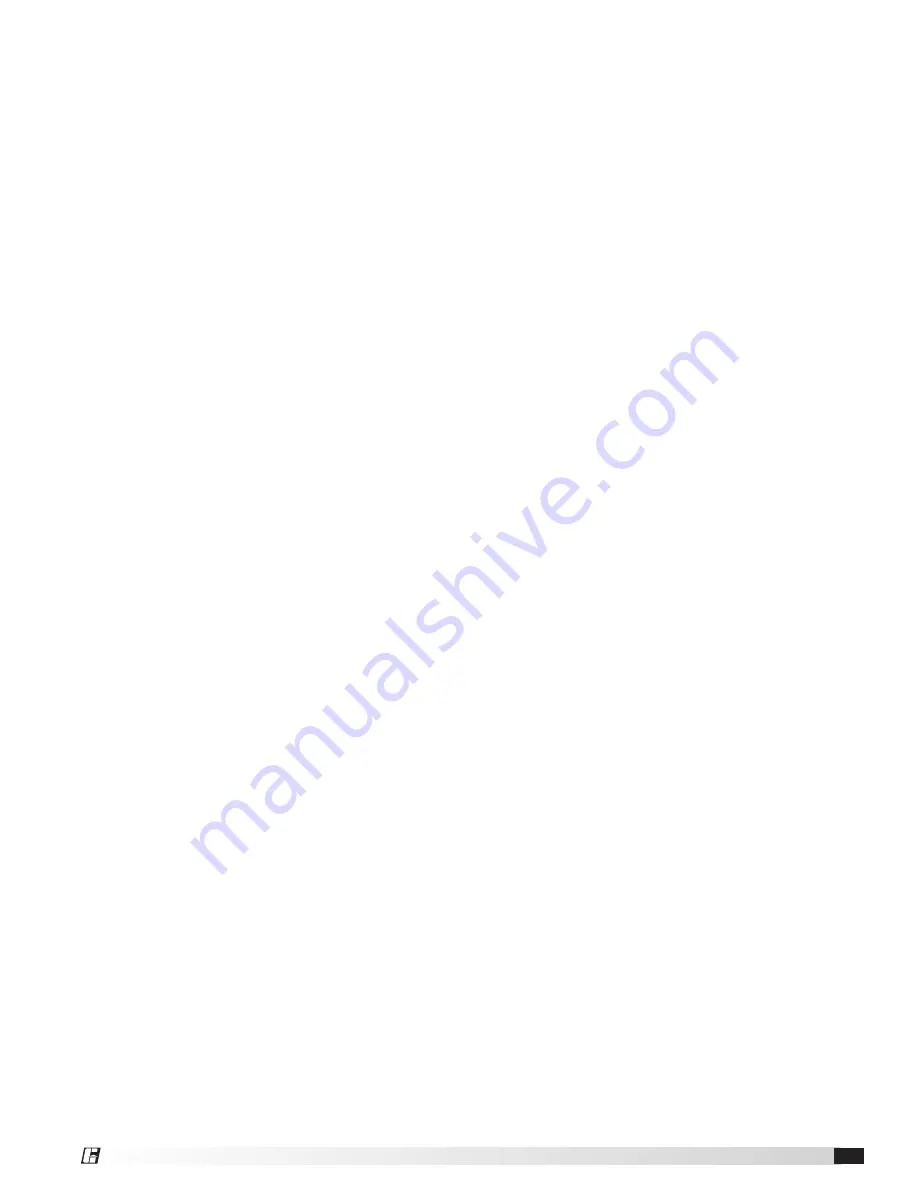
Controller Display
The controller has a two line backlit LCD display. By using the up and down arrows on the controller’s cover the
display can be toggled to show one of three sets of data:
• Top Screen: Real-Time CFM and CFM Setpoint
• Middle Screen: Real-Time Velocity (fpm) and Velocity Setpoint
• Bottom Screen: Real-Time Differential Pressure Measurement and Actuator Position
Wiring the Controller
The basic wiring of the controller is shown below in
Figure 2
. The controller’s three terminal blocks can be accessed
by opening the cover of the enclosure.
Powering the Controller
The controller is powered by applying electrical power to the “Power In” terminal block. The controller can run off of
24 VAC +/- 20% 50/60 Hz ; 24 VDC +/- 10%.
Connecting the Pressure Transducer
The second terminal block is labeled “Remote Sensor” and is used to connect the pressure transducer. The three
terminals from the Remote Sensor block connect directly to the pressure transducer as shown in
Figure 2
. The
controller supplies the transducer with its power and reads the pressure signal.
Connecting the Damper Actuator
The actuator can be powered either by the same power supply as the controller (as shown in
Figure 2
) or by running
a separate power supply to terminals 4 and 5 of the factory supplied terminal block on the AMD/AMS. In addition,
the “Control Out” from the controller (terminal 7) must be run to terminal 6 on AMD/AMS terminal block.
Connecting the Flow (or position) Setpoint Signal
Connect the 0-10 VDC or 2-10 VDC flow (or position) setpoint to the controller’s terminals 1 and 3. The controller’s
terminal 1, labeled Remote Setpoint, is the positive terminal and the controller’s terminal 3 is the negative terminal.
Connecting to the Flow Output Signal
Connecting to controller terminals 6 and 3 allows the user to read the 0-10 VDC or 2-10 VDC flow output that is
proportional to the cfm measured by the AMD/AMS. To convert the voltage signal to cfm see the section above on
Controller’s Analog Output Proportional to Real-Time Airflow.
Override Mode
See the full Vari-Green constant volume controller installation and operation manual for a description of the override
feature. The override feature can be activated by closing the contacts of an external relay across terminals 2 and 3
(or by simply putting a jumper wire across them).
AMD & AMS Series
7
®