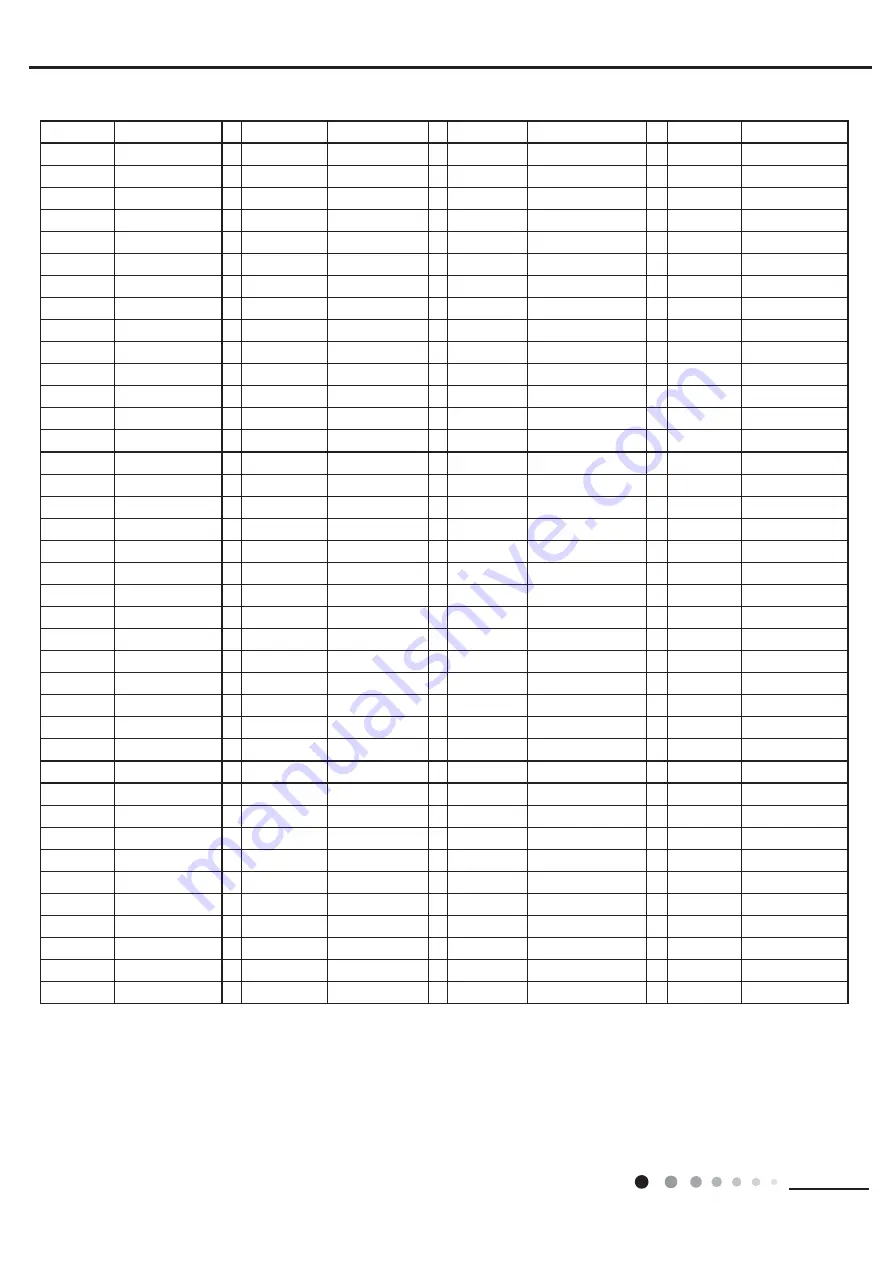
74
Maintenance
Service Manual
Resistance table of temperature sensor (20K)
Temp(
o
C)
\X¼^
Temp(
o
C)
\X¼^
Temp(
o
C)
\X¼^
Temp(
o
C)
\X¼^
-19
181.4
20
25.01
59
5.13
98
1.427
-18
171.4
21
23.9
60
4.948
99
1.386
-17
162.1
22
22.85
61
4.773
100
1.346
-16
153.3
23
21.85
62
4.605
101
1.307
-15
145
24
20.9
63
4.443
102
1.269
-14
137.2
25
20
64
4.289
103
1.233
-13
129.9
26
19.14
65
4.14
104
1.198
-12
123
27
18.13
66
3.998
105
1.164
-11
116.5
28
17.55
67
3.861
106
1.131
-10
110.3
29
16.8
68
3.729
107
1.099
-9
104.6
30
16.1
69
3.603
108
1.069
-8
99.13
31
15.43
70
3.481
109
1.039
-7
94
32
14.79
71
3.364
110
1.01
-6
89.17
33
14.18
72
3.252
111
0.983
-5
84.61
34
13.59
73
3.144
112
0.956
-4
80.31
35
13.04
74
3.04
113
0.93
-3
76.24
36
12.51
75
2.94
114
0.904
-2
72.41
37
12
76
2.844
115
0.88
-1
68.79
38
11.52
77
2.752
116
0.856
0
65.37
39
11.06
78
2.663
117
0.833
1
62.13
40
10.62
79
2.577
118
0.811
2
59.08
41
10.2
80
2.495
119
0.77
3
56.19
42
9.803
81
2.415
120
0.769
4
53.46
43
9.42
82
2.339
121
0.746
5
50.87
44
9.054
83
2.265
122
0.729
6
48.42
45
8.705
84
2.194
123
0.71
7
46.11
46
8.37
85
2.125
124
0.692
8
43.92
47
8.051
86
2.059
125
0.674
9
41.84
48
7.745
87
1.996
126
0.658
10
39.87
49
7.453
88
1.934
127
0.64
11
38.01
50
7.173
89
1.875
128
0.623
12
36.24
51
6.905
90
1.818
129
0.607
13
34.57
52
6.648
91
1.736
130
0.592
14
32.98
53
6.403
92
1.71
131
0.577
15
31.47
54
6.167
93
1.658
132
0.563
16
30.04
55
5.942
94
1.609
133
0.549
17
28.68
56
5.726
95
1.561
134
0.535
18
27.39
57
5.519
96
1.515
135
0.521
19
26.17
58
5.32
97
1.47
136
0.509