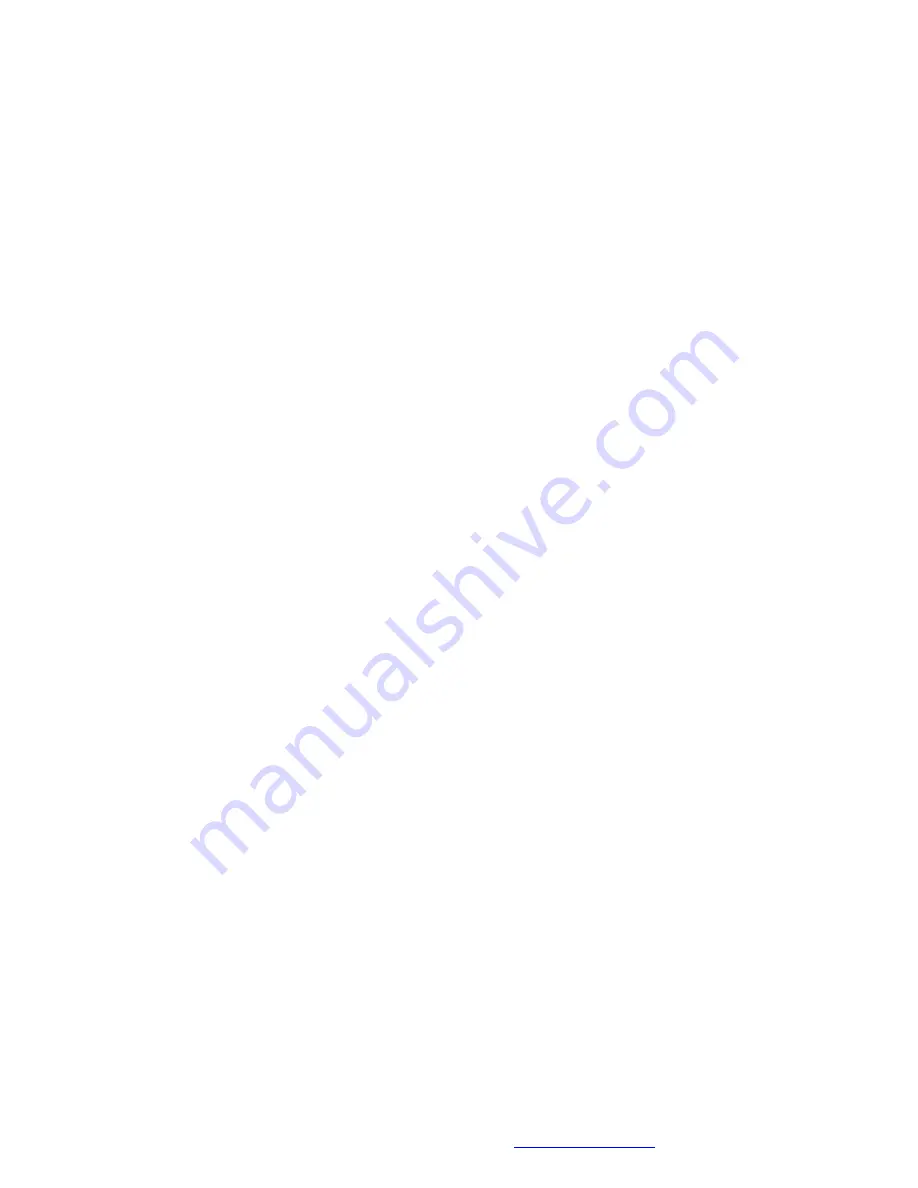
795-94053 - 15
Saponifiers
D. Optional ingredients
Sequestrants
Inhibitors
Buffering agents
Defoamers
T
HE CHEMICAL FORMULATION MUST CONSIDER ALL OF THE ABOVE CHARACTERISTICS
.
Some chemicals that are designed for spray cleaning, or that include rust inhibitors, are
not suitable for ultrasonic cleaning.
PROXIMITY
TO
THE
TRANSDUCER:
The procedure for ultrasonic cleaning is generally as follows: Put parts in basket and
place basket through three or four process steps; ultrasonic wash, spray rinse
(optional), immersion rinse, dry. Some parts loaded in baskets can mask or shadow
from the radiated surface of the ultrasonic transducers. Most ultrasonic cleaning
systems are designed for specific applications. Bottom mounted transducers or side
mounted transducers are decided upon during the process design stage. Automated
systems must specifically address the location of the transducers to insure uniformity of
the cleaning. Some parts require individual placements to separate the part for cleaning
or subsequent processes. Some parts require slow rotating or vertical motion during the
cleaning to insure critical cleanliness.
ULTRASONIC
OUTPUT
FREQUENCY:
Many technical articles claim that high frequencies penetrate more and lower
frequencies are more aggressive. The majority of the ultrasonic cleaning that is done in
industrial applications today uses 40 kHz as the base frequency. Lower frequencies,
such as 20 - 25 kHz, are used for large masses of metal, where ultrasonic erosion is of
little consequence. The large mass dampens or absorbs a great amount of the
ultrasonic cleaning power.