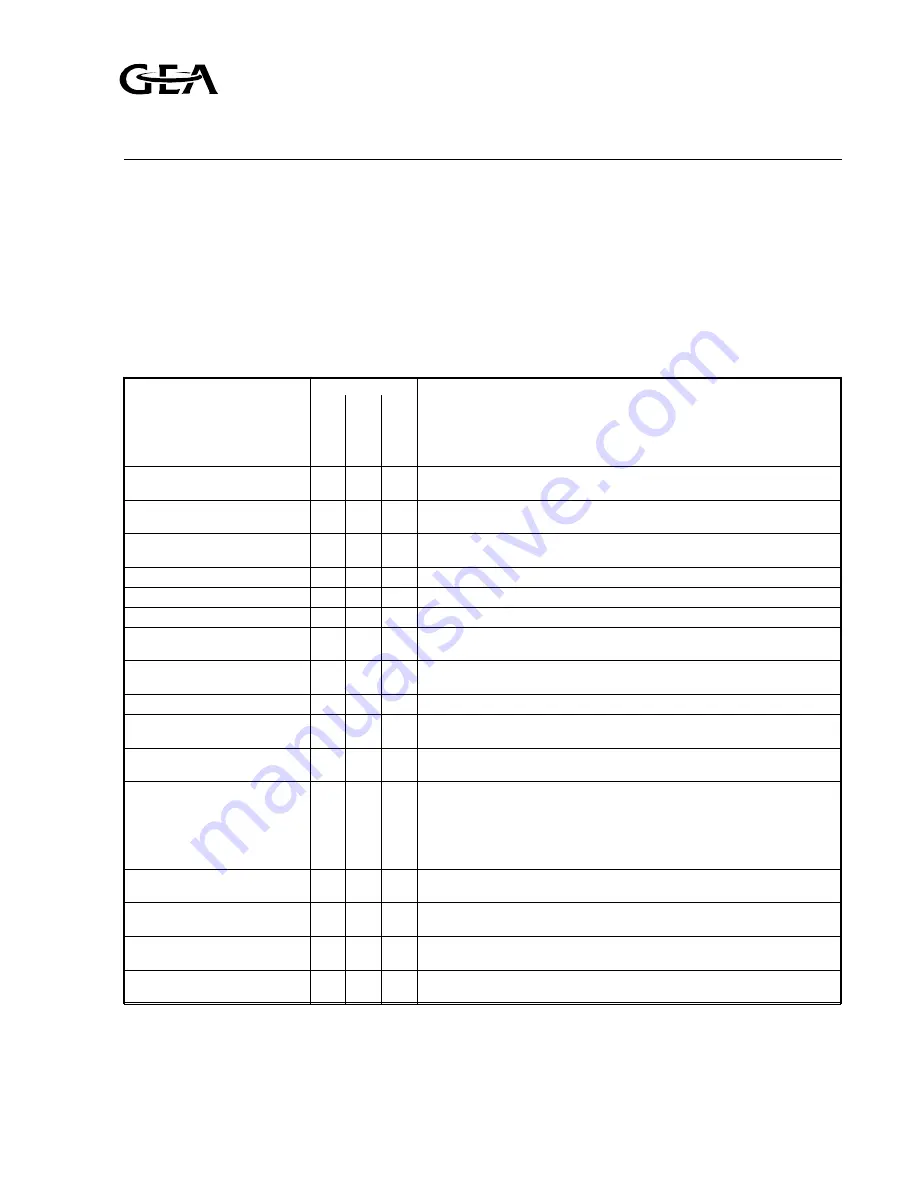
B1 INSPECTION
B1.1 Periodical inspection
These inspections should be made during the normal
shut-down periods as much as possible, so the
compressor is always ready to operate when required. If,
at that time, the number of running hours slightly differs
from the scheduled period below, the inspection should
nevertheless be carried out.
In this way it will not be necessary to stop the
compressor at inconvenient times.
The frequency of inspections is dependent on the type
of installation and operating conditions. In the case of
automatically controlled plants, the periodical inspection
are particularly important. The table below sums up all
the points on the compressor that have to be inspected
or maintained along with inspection and maintenance
frequencies.
B1.2 Survey of periodical inspections ("check list")
CHECK POINTS 1)
FREQUENCY
REMARKS
d
a
ily
we
ek
ly
month
ly
Oil level in crankcase
•
Between 25% and 75% height of the sight glass. For topping up oil, refer to
§B4.1.
Colour of the oil
•
The oil should be transparently clear. A disappearing white colour points to
dissolved refrigerant. Refer to § B2.2 for oil analysis frequency.
Lubricating oil pressure differ-
ence [dOil]
•
The indication of the oil pressure gauge should be 1.5 - 2.5 bar higher than
the value shown by the suction pressure gauge.
Oil temperature max. [Toil]
•
Refer to the "Engineering Data".
Oil leakage of shaft seal max.
•
In case of more than 1 cc/hr contact supplier.
Suction pressure [Psuc]
•
Check against design conditions. Refer to plant manual.
Discharge pressure [Pdis]
•
Refer to plant manual. For the max. allowable discharge pressure refer to the
technical data of compressor.
Suction superheat [dTo]
Intermediate superheat [dTm]
•
³
5 K
Discharge temperature max.
•
155 °C (311 °F)
Cooling water temperature (if
present) min.
•
Actual condensing tempe 10 K.
Oil temperature min. [Toil]
•
During compressor standstill the lower part of the crankcase must remain
warmer than the surroundings:
³
20 °C (NH
3
) and
³
30 °C (halocarbons).
Condition of V-belts
•
Check belts for:
1) Wear (fraying, cuts etc.) and ensure that they do not touch the groove
bottom.
2) Tension. Too low a tension gives rise to excessive flapping or oscillation in
operation. For correct tension consult the instructions given by the V-belt
supplier.
Adjustment and operation of
pressure safety switches
•
Refer to §A2.5 and to instructions of switch manufacturer.
Capacity control
•
The time lag between the unloading and loading of one cylinder or cylinder
group should generally be at least 3 - 5 minutes.
Switching frequency of the com-
pressor
•
The time interval between stopping and starting should be at least 2 minutes
and between starting and restarting 10 minutes (see §A2.10.2).
Number of operating hours
•
Check the number of operating hours in view of any maintenance operations
to be carried out.
Apart from the above check points, the sound produced by the compressor provides an indication or its mechanical condition. If
abnormal sounds are audible, their cause should be traced and removed immediately in order to prevent serious breakdowns.
1
) During the first 50 operating hours the compressor should be checked regularly for all the points mentioned above, at least
twice every 24 hours and more frequently in cases where irregularities are found.
Refrigeration Division
Grasso
B: INSPECTION, MAINTENANCE
AND TROUBLE SHOOTING
v001.99.01.en
Installation and Maintenance Manual RC(U)6
B1.1
Содержание RC6
Страница 1: ...RC U 6 Installation and Maintenance Manual 00 89 238 v004 00 02 en ...
Страница 10: ...Refrigeration Division Grasso TABLE OF CONTENTS IV Installation and Maintenance Manual RC U 6 v001 99 01 en ...
Страница 24: ...Refrigeration Division Grasso TABLE OF CONTENTS B II Installation and Maintenance Manual RC U 6 v001 99 01 en ...
Страница 36: ...Refrigeration Division Grasso TABLE OF CONTENTS C II Installation and Maintenance Manual RC U 6 v001 99 01 en ...
Страница 60: ...Refrigeration Division Grasso TABLE OF CONTENTS D II Installation and Maintenance Manual RC U 6 v001 99 01 en ...
Страница 64: ...RC6 3 RC6 4 Refrigeration Division Grasso STANDARD ILLUSTRATED PARTS LIST RC6 C4 RC6 0089238 v004 00 02 en ...
Страница 67: ...RC6 5H RC6 5L Refrigeration Division Grasso STANDARD ILLUSTRATED PARTS LIST RC6 0089238 v004 00 02 en RC6 C7 ...
Страница 68: ...RC6 6 RC6 7 Refrigeration Division Grasso STANDARD ILLUSTRATED PARTS LIST RC6 C8 RC6 0089238 v004 00 02 en ...
Страница 71: ...RC6 8 RC6 9 Refrigeration Division Grasso STANDARD ILLUSTRATED PARTS LIST RC6 0089238 v004 00 02 en RC6 C11 ...
Страница 79: ...RC6 1A PARTS LIST RC6 ACCESSORIES Refrigeration Division Grasso v002 99 05 en RC6 Accessories 3 ...
Страница 83: ...RC6 3A PARTS LIST RC6 ACCESSORIES Refrigeration Division Grasso v002 99 05 en RC6 Accessories 7 ...
Страница 84: ...Refrigeration Division Grasso PARTS LIST RC6 ACCESSORIES Accessories 8 RC6 v002 99 05 en ...
Страница 85: ...Refrigeration Division Grasso ...