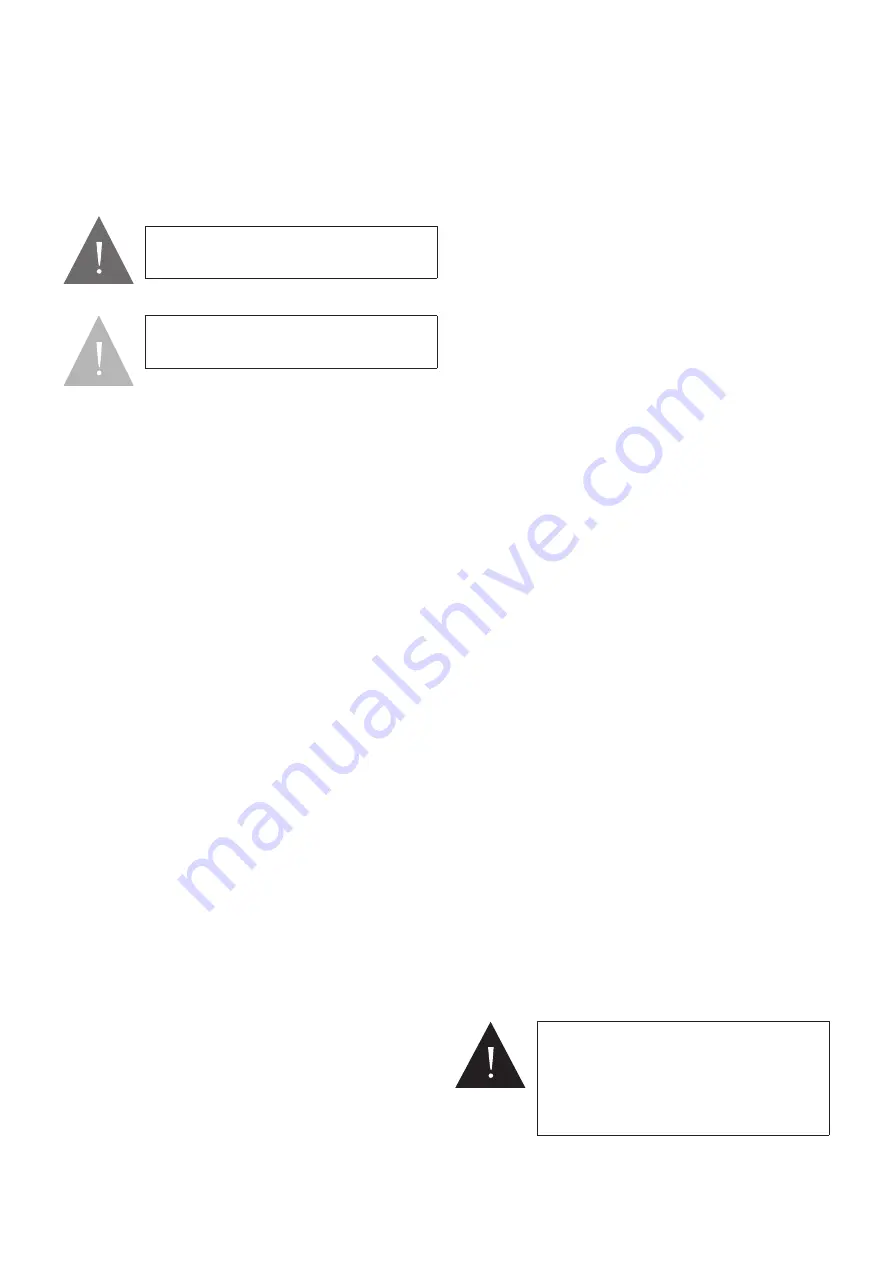
• Remove the diffuser/electrode assembly from the nozzle
holder. Refer to Figure 10-6.
• Disconnect both ignition leads from the electrodes.
4. Replace the nozzle (6). The nozzle should always be replaced
on an annual service. Refer to Table 2-2 for the correct nozzle
size and type for the required boiler output. Do NOT attempt
to clean the nozzle.
Use a 16 mm spanner to remove/re-fi t the nozzle, whilst
holding the nozzle holder using a 19 mm spanner
5. Inspect the ignition electrodes - loosen the electrode clamp
screw and withdraw the electrode assembly. Wipe clean
and check for any cracks in the ceramic insulation. Replace if
necessary.
6. Reconnect ignition leads to electrodes.
7. Re-fi t the diffuser/electrode assembly to the nozzle holder.
8. Check/adjust the diffuser position to give the correct gap (A)
between the nozzle and diffuser. Refer to Figure 10-5.
To adjust the diffuser position:
• Loosen the diffuser clamp screw.
• Slide diffuser along the nozzle holder to give the correct
gap (A).
• Tighten the diffuser clamp screw.
9. Check/adjust the electrode assembly to give the correct gap
(B) between the nozzle and electrodes. Refer to Figure 10.7
To adjust the electrode position:
• Loosen the electrode clamp screw.
• Slide the electrode assembly to give the correct gap (B).
• Tighten the electrode clamp screw.
10. Re-fi t the burner head. Refer to Figure 10.6.
• Locate the head fi xing screws in the countersunk slots in
the burner collar.
• Tighten the two screws (3) to secure the head (2) in
position on the burner.
11. Check the combustion head setting.
• The correct head setting depends on the required output
of the boiler. Refer to Table 2-2.
• This should be set to ‘0’ in all cases except when the
46/70 is set to maximum (70kw) output.
• In this case the head is set to ‘4’ (i.e. on the 4th line). Refer
to Figure 10.8.
12. To adjust the head setting:
• Loosen the two screws in the curved slots in outer ring
of the head (NOT the two head fi xing screws). Refer to
Figure 10.8.
• Rotate the end of the burner head until either ‘0’ or the 4th
line, as required.
• Tighten the two screws to fi x the head in the required
position.
13. Continue cleaning the other burner components as detailed in
Section 11.6.
11.6 CLEANING THE BURNER:
ALL
MODELS
Photodiode
The Photodiode is a push-fi t in the front of burner body. Refer to
Sections 11.9.1 and 11.9.2.
1. Holding the body of the Photodiode and NOT the cable,
carefully pull the Photodiode out of the burner.
2. Clean the sensor end of the Photodiode.
3. Replace Photodiode back in the burner and check that it is
fully pushed in.
Burner air inlet cover
This is located on the right hand side of the burner. Refer to Figure
11-5.
1. Unscrew and remove the two screws and remove the air inlet
cover from the burner.
2. Check inside and remove any debris, leaves, hair, fl uff, etc.
from the air inlet cover and air damper..
3. Check the condition of the rubber seal around the air inlet
cover. Replace if damaged or missing.
Burner fan housing
This is located over the fan impeller. Refer to Section 11.9.
With the burner air inlet cover already removed:
1. Unscrew and remove the four screws and remove the fan
housing from the burner.
2. Check and clean the fan impeller and remove any debris,
leaves, hair, fl uff etc.
3. Check/clean the fan housing is clean.
4. Check the rubber seal around the fan housing. Replace if
damaged or missing.
5. Re-fi t the fan housing to the burner and secure with the four
screws.
6. Check the air adjuster disc (15/26 model only). Refer to
Section 10.9 for details.
7. Re-fi t the air inlet cover to the burner and secure with the two
screws.
Oil pump fi lter
This is located under the end cover on the oil pump. Refer to Section
11.9.
1. Unscrew and remove the four cap screws securing the pump
end cover.
2. Remove the fi lter and wash in kerosene.
3. Check the O-ring seal around the end cover. Replace if
damaged.
4. Replace the fi lter and end cover.
5. Re-fi t the four cap screws, tightening evenly, to secure the end
cap.
11.7 AIR ADJUSTER DISC:
15/26
MODELS ONLY
Refer to Section 10.5.
11.8 RECOMMISSIONING
Servicing
Page 47
The use of an ill-fi tting spanner will damage
the nozzle and could lead to an incorrect fl ame
pattern and poor combustion.
CAUTION
Ensure that the nozzle is securely tightened
so that it does not leak but DO NOT OVER
TIGHTEN!
NOTE
WARNING
To ensure safe and effi cient operation of the
boiler it is important that re-commissioning
is carried out, especially combustion checks
(%CO
2
level, fl ue gas temperature and smoke
number) after the boiler has been serviced.
Refer to the Commissioning instructions in
Section 10.