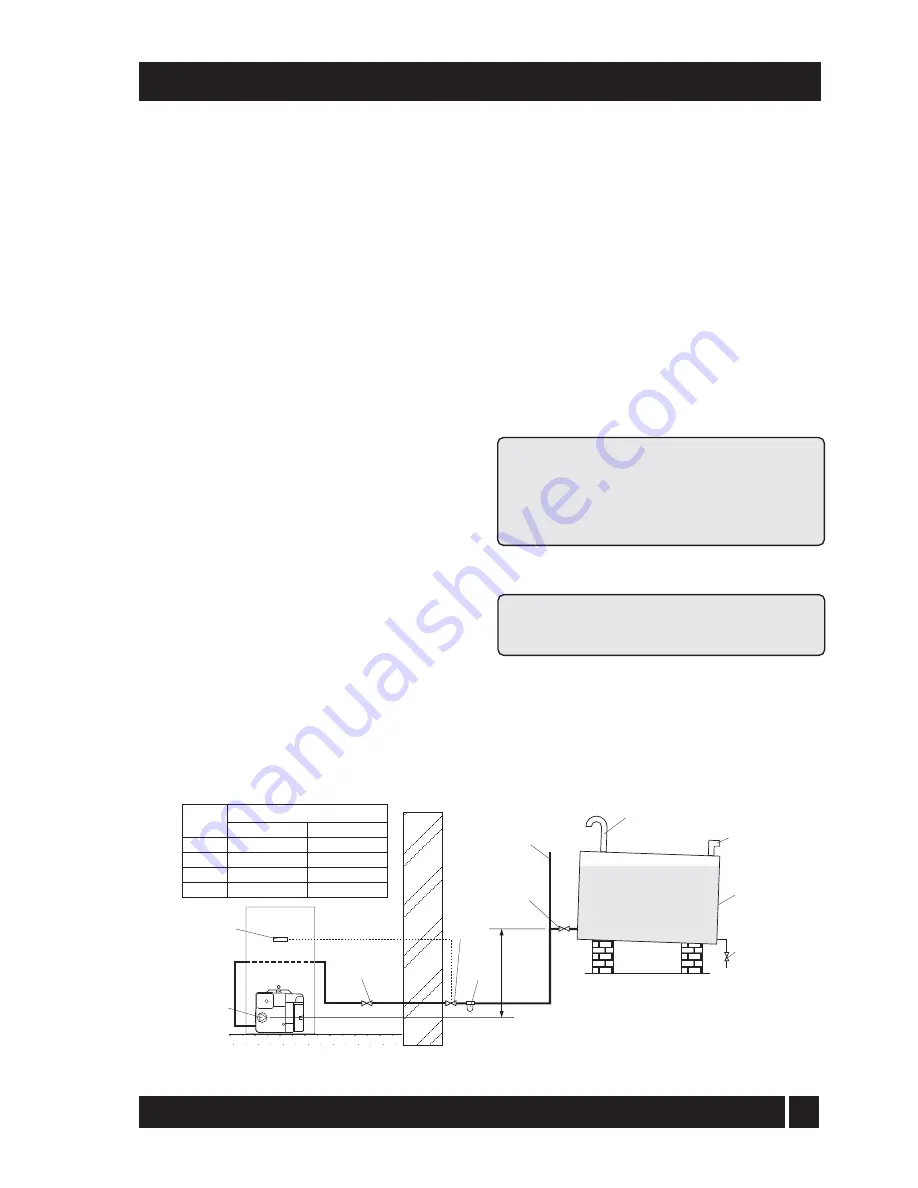
13
Grant Vortex Oil Boilers
4 - GENERAL BOILER INFORMATION
4.4.2 Fuel pipes
1
Fuel supply pipes should be of copper tubing with
an external diameter of at least 10 mm.
Galvanised pipe must not be used.
All pipe connections should preferably use flared
fittings. Soldered connections must not be used on
oil pipes.
2
Flexible pipes must not be used outside the boiler case.
3
A remote sensing fire valve must be installed in the
fuel supply line (outside) where it enters the building,
with the sensing head located above the burner.
Recommendations are given in BS 5410:1:1997.
4
A metal bowl type filter with a replaceable micronic
filter must be fitted in the fuel supply line adjacent to
the boiler. A shut-off valve should be fitted before the
filter, to allow the filter to be serviced.
5
A flexible fuel line, adaptor and
1
/
4
" BSP isolation
valve are supplied loose with the boiler for the final
connection to the burner. If a two pipe system or
'Tiger Loop' type de-aerator is used, an additional
flexible fuel line (600 mm) and
3
/
8
" to
1
/
4
" BSP male
adaptor are available to purchase from Grant
Engineering (UK) Limited, Part No. RBS104.
6
Metal braided flexible pipes should be replaced
annually when the boiler is serviced. Long life
flexible pipes should be inspected annually and
replaced at least every 60 months.
4.4.3 Single pipe system - (See Fig. 3)
1
Where the storage tank outlet is above the burner
the single pipe system should be used. The height
of the tank above the burner limits the length of
pipe run from the tank to the burner.
2
As supplied the burner is suitable for a single pipe
system.
4.4.4 Two pipe system - (See Fig. 4)
1
When the storage tank outlet is below the burner,
the two pipe system should be used. The pipe runs
should be as shown in Fig. 4. The return pipe
should be at the same level in the tank as the
supply pipe, both being 75 to 100 mm above the
base of the tank. The pipe ends should be a
sufficient distance apart so as to prevent any
sediment disturbed by the return entering the
supply pipe.
2
Avoid the bottom of the tank being more than 3 m
below the burner.
3
A non-return valve should be fitted in the supply
pipe together with the filter and fire valve. A non-
return valve should be fitted in the return pipe if
the top of the tank is above the burner.
4
To be used with a two-pipe system, the burner
must be fitted with an additional flexible fuel line
(a flexible fuel line (600 mm) and
3
/
8
" to
1
/
4
" BSP
male adaptor are available to purchase from Grant
Engineering (UK) Limited), Part No. RBS104. See
Section 4.4.6.
5
The pump vacuum should not exceed 0.4 bar.
Beyond this limit gas is released from the oil.
For guidance on installation of top outlet fuel tanks and
suction oil supply sizing, see OFTEC booklet T1/139.
Available at www.oftec.org.uk.
Fig. 3 - Single pipe system
Filter
Fire
valve
Shut-off
valve
Shut-off
valve
A
Sludge
valve
Fill
pipe
Vent
pipe
Level
gauge
Fuel
storage
tank
Fire
valve
sensor
Pump
Head A
(m)
Maximum pipe run (m)
0.5
1.0
1.5
2.0
10mm OD pipe
10
20
40
60
12mm OD pipe
20
40
80
100