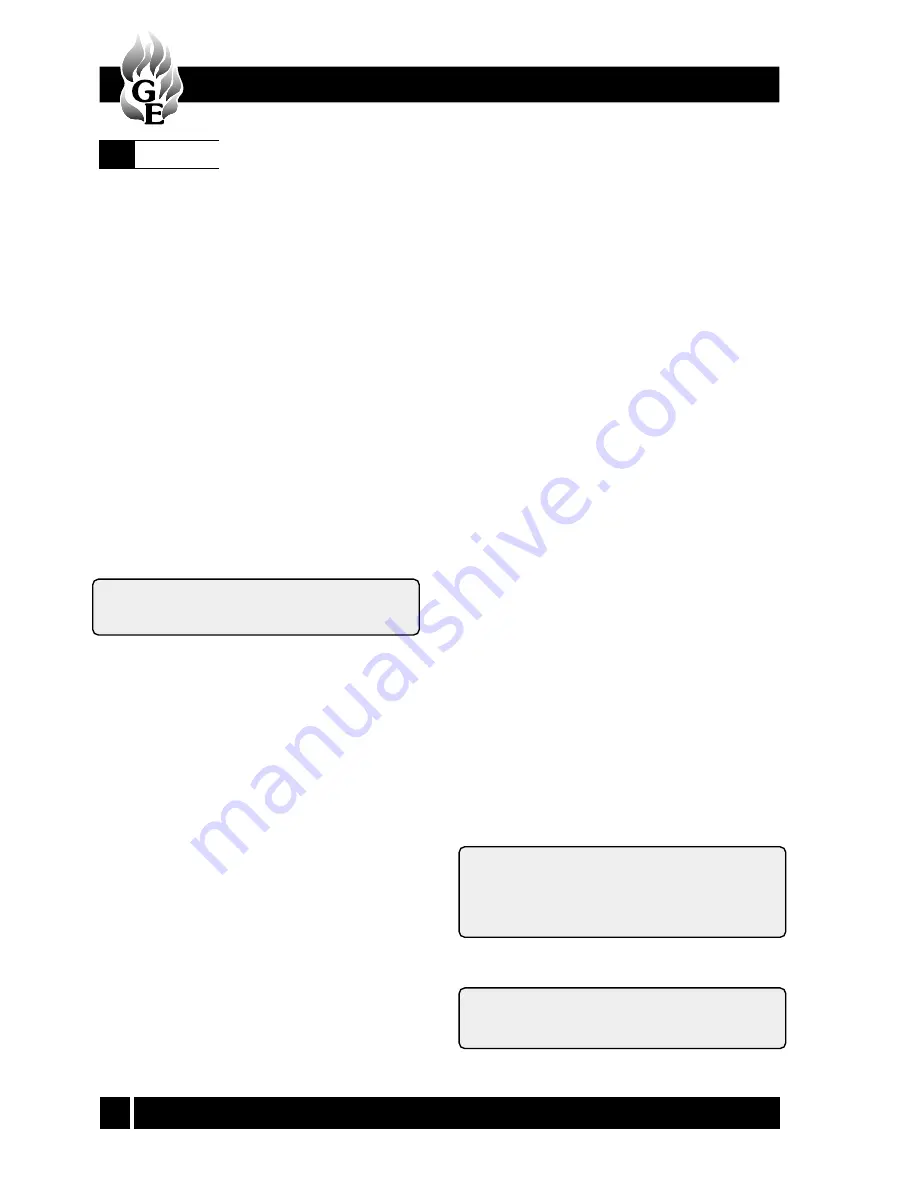
12
Multi Pass Oil Boilers
3.3.1 Fuel storage
A painted (outside only) storage tank must be
constructed to BS 799:5:1987 and OFST 200 and
should include the following:-
a
A fuel level gauge (not a glass type).
b
A vent pipe incorporating a weatherproof
termination (bend or cap) of a diameter not less
than the filling pipe.
c
A sludge valve.
d
An outlet valve at the opposite end of the tank
to the sludge valve.
The tank should be positioned in accordance with the
recommendations given in BS 5410:1:1997, which
gives details of filling, maintenance and protection
from fire.
The tank should be suitably supported so as to obtain a
slope of 20 mm per metre towards the sludge valve.
A galvanised tank must not be used.
A plastic tank may be used and must comply with
OFS T100.
Note: Plastic tanks should be adequately and
uniformly supported on a smooth level surface, across
their entire base area.
3.3.2 Fuel pipes
1
Fuel supply pipes should be of copper tubing with
an internal diameter of at least 8 mm.
Galvanised pipe must not be used.
2
Flexible pipes must not be used outside the boiler
case.
3
A remote sensing fire valve must be installed in the
fuel supply line (outside) where it enters the
building, with the sensing head located above the
burner. Recommendations are given in BS
5410:1:1997.
4
A metal bowl type filter with a replaceable
micronic filter must be fitted in the fuel supply line.
A shut-off valve should be fitted before the filter,
to allow the filter to be serviced.
5
A flexible fuel line, adaptor and
1
/
4
" BSP isolation
valve are supplied loose with the boiler for the final
connection to the burner. If a two pipe system or Tiger
Loop system is used, an additional flexible fuel line
(600 mm) and
3
/
8
" to
1
/
4
" BSP male adaptor are
available from Grant Engineering (UK) Limited.
3 - GENERAL BOILER INFORMATION
6
Flexible pipes should be inspected annually when
the boiler is serviced and replaced every two years.
7
The use of a 'Tankmaster' and Tiger Loop is an
ideal way of delivering an oil supply to the boiler.
The Tankmaster unit, fitted to the storage tank,
includes a filter, sight tube, shut-off valve and fire
valve. A separate fire valve is required in the fuel
line (outside) where it enters the building
containing the boiler. See Fig. 4.
3.3.3 Single pipe system - (See Fig. 2)
1
Where the storage tank outlet is above the burner
the single pipe system should be used. The height
of the tank above the burner limits the length of
pipe run from the tank to the burner.
2
As supplied the burner is suitable for a single pipe
system.
3.3.4 Two pipe system - (See Fig. 3)
1
When the storage tank outlet is below the burner,
the two pipe system should be used. The pipe runs
should be as shown in Fig. 3. The return pipe
should be at the same level in the tank as the
supply pipe, both being 75 to 100 mm above the
base of the tank. The pipe ends should be a
sufficient distance apart so as to prevent any
sediment disturbed by the return entering the
supply pipe.
2
Avoid the bottom of the tank being more than 3 m
below the burner.
3
A non-return valve should be fitted in the supply
pipe together with the filter and fire valve. A non-
return valve should be fitted in the return pipe if
the top of the tank is above the burner.
4
To be used with a two-pipe system, the burner
must be fitted with an additional flexible fuel line
(a flexible fuel line (600 mm) and
3
/
8
" to
1
/
4
" BSP
male adaptor are available from Grant Engineering
(UK) Limited). See Section 3.3.6.
5
The pump vacuum should not exceed 0.4 bar.
Beyond this limit gas is released from the oil.
For guidance on installation of top outlet fuel tanks and
suction oil supply sizing, see OFTEC booklet T1/139.
Available at www.oftec.org.uk
Fuel supply
3.3
Содержание 140/160
Страница 13: ...13 Multi Pass Oil Boilers 3 GENERAL BOILER INFORMATION Fig 3 Two pipe system Fig 2 Single pipe system...
Страница 19: ...19 Multi Pass Oil Boilers Fig 11 Typical conventional flue with brick chimney 3 GENERAL BOILER INFORMATION...
Страница 20: ...20 Multi Pass Oil Boilers 3 GENERAL BOILER INFORMATION Fig 12 External flue Green system...
Страница 41: ...41 Multi Pass Oil Boilers 7 BOILER SERVICING Fig 34 160 200 Baffle arrangement Left Right...
Страница 51: ...51 Multi Pass Oil Boilers...